In the realm of high-performance metals, 52100 alloy steel stands out for its remarkable blend of strength and durability. Heralded as an exemplary material within industries requiring precision and resilience, this steel variant boasts a rich history and a spectrum of properties that contribute to its widespread utility. This guide provides an in-depth look at the nuances defining 52100 alloy steel, from its nuanced chemical composition to the thermal treatments that enhance its characteristics, laying a solid foundation for understanding its pivotal role across various applications.
What Is 52100 Alloy Steel?
52100 alloy steel is a high carbon, chromium-containing low alloy steel that stands out for its excellent wear resistance and high fatigue strength. As a grade of bearing steel, its properties are optimized to resist stress and friction, which makes it particularly well-suited for use in rolling-element bearings.
The fabric of this material interweaves the durability of carbon with the steadfastness of chromium. The combination results in an alloy capable of enduring significant loads without deforming – crucial for precision components where dimensional stability under stress is paramount.
From an engineering perspective, 52100 steel is ideal for applications demanding both hardness and resistance to wear. It has a consistent performance under temperature variations due to its stable physical properties at elevated temperatures. However, this does not imply that the steel is infallible; rather, it has been refined to respond predictably in challenging environments, thereby ensuring reliability in critical mechanical systems.
Typically hardened and tempered through a controlled heating process, 52100 alloy steels gain a refined microstructure that further enhances their inherent characteristics. They exhibit an admirable balance between toughness and hardness after heat treatment—a trait indispensable when selecting materials for components needing to withstand harsh operational conditions while also maintaining precise tolerances over prolonged use cycles.
Properties of 52100 Alloy Steel
The properties of 52100 alloy steel distinguish it as a highly reliable and robust material suitable for a variety of demanding applications requiring high wear resistance and durability. The following table outlines the key physical and mechanical properties of this alloy:
Property | Detail |
---|---|
Density | Approximately 7.81 g/cm³ |
Hardness (Rockwell C) | Typically 64 HRC when hardened |
Tensile Strength | Up to 325,000 psi |
Yield Strength | Up to 295,000 psi |
Elastic Modulus | Around 30 x 10⁶ psi |
Elongation | Usually in the range of 12% – 13% in a length of 2″ |
Reduction of Area | Around 40% |
Wear Resistance | High due to strong carbide concentration |
These characteristics stem from its chemical composition and specialized heat treatment processes that impart strength and resistance attributes essential for performance in severe conditions.
52100 steel also exhibits excellent fatigue life, quite suitable for dynamic or static loads over long periods. Its high carbon content grants the material superior hardness after heat treatment, yet it maintains a degree of toughness uncommon among other high-hardness steels.
Abrasion resistance is another property where 52100 excels, thanks to its uniform and fine-grained martensitic structure when properly quenched and tempered. This makes the steel less prone to chipping or cracking under stress or when handling impact forces.
It is these properties that allow designers to employ thinner cross-sections without sacrificing performance, leading to potentially lighter yet durable components. The alloy has low resistance to corrosion; hence protective finishing processes may be required for environments where exposure can lead to material degradation.
Pros of 52100 Alloy Steel
Advantage | Description |
---|---|
High Hardness | Its ability to attain high hardness makes it resilient against wear and abrasion, thus extending tool life. |
Excellent Fatigue Resistance | The material’s endurance limit is elevated, resisting fatigue in applications involving cyclic loading stresses. |
Good Dimensional Stability | It has low dimensional changes during heat treatment, maintaining the precision of components after manufacturing. |
Superior Wear Resistance | Thanks to its high carbon and chromium content, it has a strong resistance to surface wear. |
Strong Rolling Contact Fatigue Life | In bearings and other rolling elements, it can withstand repeated stress without succumbing to fatigue cracks easily. |

Cons of 52100 Alloy Steel
Difficulty | Issue |
---|---|
Corrosion | Susceptible to rust without protective measures |
Heat Treatment | Hardenability can cause distortion/cracking |
Thermal Shock | Sudden temperature changes may lead to fractures |
Machinability | Challenges with tool wear and achieving tolerances |
Weldability | Complex procedures required due to poor weldability |
What Is 52100 Alloy Steel Used For?
Application Sector | Specific Uses |
---|---|
Bearings | Ball bearings, roller bearings |
Cutting Tools | Knives (especially precision knives), blades |
Automotive Industry | Parts subject to high stress |
Aerospace | Critical components |
Heavy Machinery | High-strength machine parts |
This high-carbon, chromium-containing alloy steel is primarily famous for being the go-to choice for manufacturing all types of bearings. Its ability to withstand both radial and axial loads without deforming makes 52100 alloy steel particularly suitable for bearings used in automotive and aerospace industries where performance under stress is essential.
The fine grain structure of this steel allows for a sharp and durable edge, advantageous when producing precision blades and cutting tools. In highly specialized knives, such as those required in custom or high-end culinary applications, the properties of 52100 make it favorable among professionals who seek exceptional sharpness retention.
Moreover, certain components within the automotive industry rely on the strength provided by 52100 alloy steel. These include elements that are subjected to significant levels of stress but cannot afford to fail under pressure. The consistent performance of these parts is critical to both safety and functionality.
In heavy machinery settings where components experience tremendous forces and potential wear due to friction, this steel’s hardenability ensures that large cross-sections can be effectively hardened—contributing significantly to the longevity of machine parts that must resist wear over time.
Aerospace engineers also capitalize on the asset of reliability associated with 52100 alloy steel when designing critical aircraft components. Where any component failure could lead to catastrophic consequences, the rigorous standards fulfilled by this type of steel render it integral in designs prioritizing safety and endurance.
To summarize, thanks to its specific properties like extreme hardness after heat treatment and effective resistance against deformity under load or abrasiveness, 52100 alloy steel stands out as an indispensable material across several demanding sectors.
How Is 52100 Alloy Steel Made?
Initially, raw materials such as iron ore, carbon, chromium, and other elements are melted together in an electric arc furnace (EAF). During this melting process, the precise chemical composition is achieved by adding the exact amounts required to obtain 52100’s characteristics.
Once the melt reaches the desired chemical balance, it is refined to remove impurities and cast into ingots or continuous cast billets. These ingots or billets then undergo a series of hot and cold working processes to improve their microstructure. The steel is hot-forged or rolled at high temperatures to shape it into the desired form while maintaining its internal integrity.
Subsequently, a controlled cooling (annealing) process follows to relieve internal stresses developed during hot working. This annealing also prepares the alloy for further machining and hardening processes.
The next step includes machining where the material can be cut or shaped according to requirements. Since 52100 alloy steel can be tough on cutting tools due to its hardness, specific carbides or high-speed tool steels are commonly used for machining operations.
Finally, heat treatment processes such as quenching and tempering are applied to achieve optimal hardness and toughness levels in accordance with industry standards. Quenching involves heating the steel to a required temperature followed by rapid cooling whereas tempering adjusts hardness levels by re-heating under lower temperatures and then cooling at a specific rate.
Throughout these stages, quality control measures including chemical analysis and mechanical testing ensure that the produced 52100 alloy steel meets all specified properties before being shipped for use in various applications.
What Is the Chemical Composition of 52100 Alloy Steel?
Element | Weight Percentage (%) |
---|---|
Carbon (C) | 0.98 – 1.10 |
Chromium (Cr) | 1.30 – 1.60 |
Manganese (Mn) | 0.25 – 0.45 |
Silicon (Si) | 0.15 – 0.35 |
Sulfur (S) | ≤0.025 |
Phosphorus (P) | ≤0.025 |
It’s crucial to note that minor variations in these percentages can occur depending on the exact requirements of the intended application or specific manufacturer standards.
Carbon is a principal element in this steel variety, effectively enhancing hardness and tensile strength when heat treated, which makes the steel well-suited for bearing applications that demand high durability and resistance to deformation under stress.
Chromium adds robustness to the corrosion resistance and hardenability, ensuring that even with thin cross-sections, there will be thorough hardening during heat treatment processes.
Manganese contributes to improvements in hardenability as well while serving to deoxidize the steel during its production process.
Silicon serves dual purposes: assisting in deoxidation along with manganese and also increasing strength by reinforcing the steel matrix.
Trace amounts of sulfur and phosphorus are typically kept at bay because they can potentially create weaknesses within the metal’s structure if present in higher concentrations.
What Is the Carbon Content of 52100 Alloy Steel?
Specifically, 52100 steel has a carbon content that typically ranges from 0.98% to 1.10%. This relatively high level of carbon is instrumental in achieving the desired hardness and wear resistance that this type of steel is known for.
It is this percentage of carbon that aids in creating a microstructure within the steel that can be hardened through heat treatment processes, such as quenching and tempering. The precise amount of carbon also contributes to the steel’s ability to maintain a sharp edge, making it particularly valuable for applications requiring high levels of durability against deformation or abrasive wear.
Machinability Rating of 52100 Alloy Steel
The machinability of steels is often expressed as a percentage relative to a standard. In this case, the standard is usually AISI B1112 steel which is considered 100% machinable. The machinability rating for 52100 alloy steel typically falls around 50-55%, signifying that it is more challenging to machine than B1112.
This lower machinability is due in part to the high hardness and strength of 52100 alloy steel, which includes high carbon and chromium content that contributes to its wear resistance properties. As a result of these attributes, machining operations on 52100 might require more robust and wear-resistant tools, slower speeds, or specialized cutting fluids.
Alloy | Machinability Rating |
---|---|
AISI B1112 (Standard) | 100% |
52100 Alloy Steel | 50-55% |
To ensure efficient machining of 52100 alloy steel, certain considerations must be implemented:
- Tooling: Utilize carbide or other hard material tipped cutting tools for better performance.
- Speeds: Employ lower machining speeds to mitigate tool wear.
- Coolants: Apply appropriate coolants generously to reduce heat stress on tools and workpiece.
- Technique: Adaptive control strategies may also help manage tool load during difficult cuts.
Thermal Properties of 52100 Alloy Steel
52100 alloy steel possesses distinctive thermal properties that are critical for its performance in various applications. A relevant parameter in this context is the coefficient of thermal expansion, which denotes how the material expands when heated and contracts when cooled. For 52100 alloy steel, this value is approximately 7.3 to 13.9 (10^-6/K) over a temperature range of -100 to 730°C.
The thermal conductivity of this material governs heat flow through it and is essential for determining suitability in applications where heat dissipation is crucial. Typically, the thermal conductivity for 52100 steel lies around 46.6 W/(m·K) at room temperature.
Another key thermal property is the specific heat capacity, which reflects how much energy is required to raise the temperature of a unit mass by one degree Celsius or Kelvin. This value varies with temperature but generally hovers around 0.46 J/(g·K) for 52100 alloy steel.
Moreover, considerations such as the critical temperature points including Ac1 (the temperature at which austenite begins to form during heating) and Ac3 (the temperature above which the steel is fully austenitic) are fundamentally important when tempering or heat treating this steel alloy. In the case of 52100 alloy steel, these temperatures are typically around 727 °C (Ac1) and about 800 °C (Ac3).
52100 alloy steel also has a relatively high melting point compared to some other steels, which can influence its use in high-temperature applications or processing techniques like casting or forging.
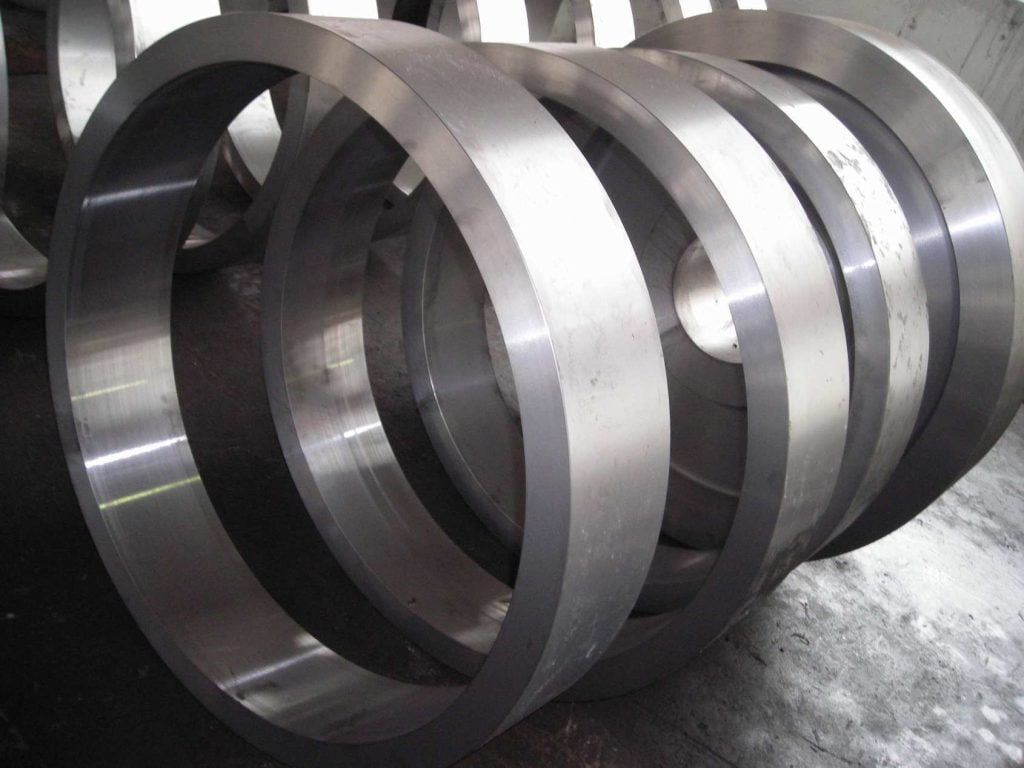
What Are Equivalents of 52100 Alloy Steel?
Various international standards organizations have their own designated equivalents for this high carbon, chromium steel, primarily utilized where high levels of durability and precision are required.
In table format, we identify some of the most recognized equivalents from different standard-setting bodies:
Country/Standard | Steel Grade Equivalent |
---|---|
USA (AISI / SAE) | 52100 |
Germany (DIN) | 1.3505 |
Japan (JIS) | SUJ2 |
International (ISO) | 100Cr6 |
Europe (EN) | 102Cr6 |
Difference Between 52100 Alloy Steel and 1095 Alloy Steel
Property | 52100 Alloy Steel | 1095 Alloy Steel |
---|---|---|
Composition | Higher chromium content along with carbon | Primarily high carbon content |
Hardness | Enhanced hardness due to chromium; better deep hardening | Carbon-based hardening; generally less hard than 52100 |
Impact Toughness | Typically higher due to alloying elements | Lower compared to 52100 due to lack of alloying elements |
Wear Resistance | High, attributed to chromium forming hard carbides | Lower, primarily due to carbon content |
Machinability | More challenging because of toughness and wear resistance | Easier to machine due to lack of additional alloy elements |
What Is the Difference Between 52100 Alloy Steel and D2 Alloy Steel?
Attribute | 52100 Alloy Steel | D2 Alloy Steel |
---|---|---|
Primary Composition | High carbon, chromium | High carbon, high chromium |
Carbon Content | Approximately 1.0-1.1% | Slightly more at approximately 1.4-1.6% |
Chromium Content | About 1.3-1.6% | Higher at around 11-13% |
Hardness | Reached up to ~64 HRC after heat treat | Can go up to ~60-62 HRC after heat treatment |
Toughness | Good considering the high hardness level | Generally lower than 52100 due to higher hardness |
Wear Resistance | Excellent; ideal for rolling elements | Superior; partially due to higher chromium levels |
Machinability | Fairly machinable before heat treatment | Lesser than 52100; its high carbide content makes it more difficult to machine |
While both steels are often used in the creation of cutting tools or precision bearings, D2 is typically favored in environments where abrasion resistance is paramount due to its higher levels of chromium resulting in a denser volume of carbides within the material. Contrastingly, the somewhat lower chromium content in 52100 provides a good balance making it tough while still having sufficient wear resistance for applications like rolling element bearings.
It’s worth noting that for items requiring sharp edges such as knives or blades, while both might be utilized depending on specific requirements, users may prefer one over the other based on desired qualities—D2 offering longer edge retention but possibly being more brittle when compared with the relative toughness yet adequate edge-holding capacity of 52100.
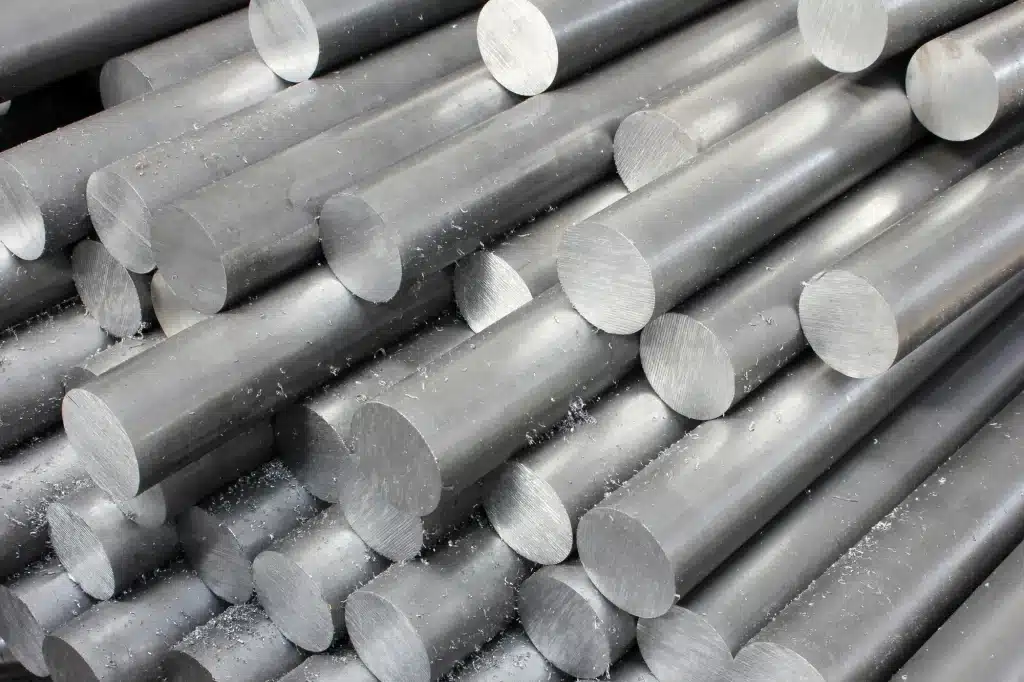
What Is the Difference Between 52100 Alloy Steel and S30V Alloy Steel?
The differentiation between 52100 alloy steel and S30V alloy steel is primarily evident in their chemical composition, performance characteristics, and intended applications. 52100 alloy steel is well-known for its excellent wear resistance and toughness due to its significant chromium content; however, it lacks the level of corrosion resistance that is inherent in S30V stainless steel.
On one hand, we have 52100 steel primarily composed of carbon (0.98%-1.10%) which gives it remarkable hardness and strength. The presence of manganese, chromium, silicon, and small amounts of phosphorus and sulfur contribute to its microstructure stability and wear-resistance capacities. This makes it an ideal choice for heavy-duty rolling bearings or tools where high durability is a necessity.
In contrast, S30V steel is a martensitic stainless powder-made grade known for its balanced features with a sophisticated additive mix including carbon (1.45-1.55%), molybdenum (2.0 – 4.0%), vanadium (3.0% – 4.0%), as well as higher chromium levels compared to 52100 (>14%). These elements amplify the material’s corrosion resistance drastically making it highly suitable for knife blades that are exposed to harsh environments.
Below you will find a comparison table highlighting key differences:
Property | 52100 Alloy Steel | S30V Stainless Steel |
---|---|---|
Carbon Content | High (∼1%) | Higher (∼1.5%) |
Chromium Content | Moderate (∼1.5%) | High (>14%) |
Wear Resistance | Excellent | Very Good |
Toughness | Very Good | Good |
Corrosion Resistance | Moderate | Excellent |
Primary Applications | Bearings, Heavy-Duty Tools | Premium Knife Blades |
Machinability | Fairly Difficult | Moderately Difficult |
What is the difference between 4140 and 52100 alloy steel?
Property | 4140 Alloy Steel | 52100 Alloy Steel |
---|---|---|
Main Chemical Composition | Medium-carbon steel with chromium, molybdenum, and manganese. | High-carbon, chromium steel. |
Carbon Content | Approximately 0.40% carbon. | Higher carbon content at around 1.00%. |
Primary Characteristics | Well-renowned for toughness, high torsional strength, and good fatigue strength. | Notable for wear resistance, high hardness after heat treatment, and excellent fatigue life. |
Typical Applications | Common in automotive applications like axles, crankshafts, gears as well as in oil and gas industries for drilling equipment. | Predominantly used in bearing manufacturing due to its excellent rolling-contact fatigue performance. |
Hardening Ability | Good hardenability with pre-heating typically unnecessary prior to quenching to achieve high core strengths. | Exceptional surface hardening ability while maintaining a tough core; requires precise control in heat-treating processes. |
Ductility & Toughness | Displays a fine balance between ductility and toughness which can be adjusted with heat treatment parameters. | Slightly less ductile when compared to 4140 but offers enhanced surface hardness post-heat treatment. |
Machinability | Good machinability allowing easier shaping through cutting tools without sacrificing too much tool life. | More challenging to machine given its high carbon content which leads to increased tool wear rate. |
While both steel types have their own set of advantages depending on their intended use, they contrast mainly in terms of the carbon content that affects their hardness after heat treating: 52100 typically becomes harder than 4140 due to higher levels of carbon providing more carbide formation during tempering treatments. This makes it preferable for applications requiring excellent wear resistance such as bearings where surface strength is paramount.
In contrast, the versatility of 4140 comes from a combination of good fatigue life, torsional strength, and impact resistance making it suitable for various demanding applications outside of those exclusively requiring maximum surface hardness or dimensional stability under high stress.
In conclusion
In conclusion, 52100 alloy steel is a versatile and reliable material that serves a wide range of industries with its superior hardness, strength, and fatigue resistance. Whether you are in the business of creating precision bearings or crafting high-quality knives, understanding the properties and potential applications of this steel can greatly influence the success of your products. However, choosing the right material for your specific needs requires careful consideration and expert guidance.
We encourage you to explore further how 52100 alloy steel can benefit your projects and contribute to your success. Visit our website for an extensive look at this remarkable material’s specifications, real-world applications, processing techniques, and much more. Should you have any questions or need personalized advice on selecting the proper steel grade for your operations, do not hesitate to contact us directly.
Leverage our expertise to ensure that you are making the most informed decisions when it comes to integrating 52100 alloy steel into your designs. Reach out today—our team is ready to assist you with exceptional support