The comparison between 718 and P20 steel involves understanding the distinct properties, applications, and performance characteristics of each type. As tool steels with different compositional makeups, 718 and P20 serve in various industrial applications, ranging from mold making to aerospace engineering. This article aims to delineate the fundamental differences between these two materials, shedding light on their mechanical properties, heat treatment processes, and suitability for specific tasks within the manufacturing sector.
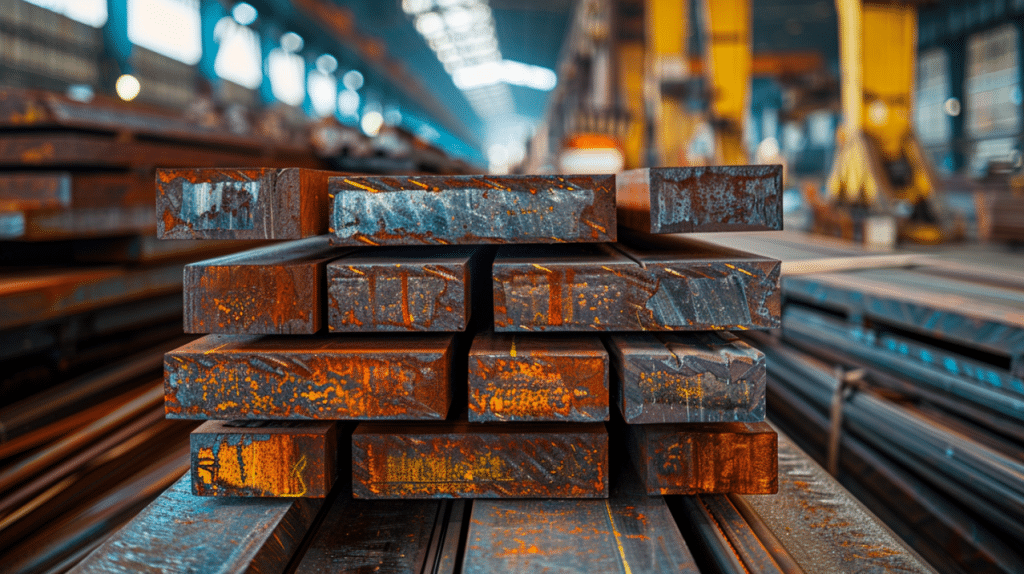
What Is P20 Steel
P20 steel is frequently classified as a versatile, low-alloy tool steel known for its distinctive properties that make it ideal for various industrial applications. This categorization of steel stands out due to its balanced composition, which delivers a unique blend of toughness, strength, and dimensional stability during the manufacturing process.
Historically designed for use in the plastic mold industry, P20 steel has gained widespread adoption due to its excellent machinability and relatively simple heat treatment requirements. The alloy’s formulation aims to offer an optimal combination of hardness and ductility, thereby minimizing risks associated with cracking or brittleness often encountered in competing materials. This balance ensures that tools and components fabricated from P20 steel can withstand considerable wear and tear under operational conditions without compromising their structural integrity.
One key characteristic of P20 steel is its pre-hardened state at the time of supply. This feature significantly reduces the necessity for further heat treatments post-manufacturing, thus streamlining the production process. The ability to be delivered ready-to-use not only expedites project timelines but also contributes to cost savings by eliminating additional processing steps required for other types of tool steels.
The adaptability of P20 steel extends beyond its application in mold making. It is utilized across a diverse range of industries including but not limited to automotive die casting, injection molding, tooling, and even in the creation of some high-strength structural components. This wide range of applications highlights the material’s flexibility to meet various engineering requirements while maintaining high performance standards.
Chemical Composition Of P20 Steel
At its core, P20 steel typically contains about 0.28% to 0.40% Carbon (C), which plays a crucial role in determining the hardness and strength of the steel. The presence of carbon at these levels ensures that the material can achieve a good balance between hardness and toughness – an essential characteristic for many tooling applications.
Furthermore, Manganese (Mn) is found in percentages ranging from 0.60% to 1.00%. Manganese enhances the hardenability of P20 steel, contributing to its strength and resistance to wear. This element also improves the steel’s response to heat treatment processes, allowing for more precise control over the final material properties.
Chromium (Cr) constitutes approximately 1.40% to 2.00% of P20 steel’s chemical composition. Chromium increases corrosion resistance and hardness, making the material more durable under challenging working conditions. It also aids in maintaining strength at elevated temperatures.
Molybdenum (Mo) at about 0.30% to 0.55% enhances tensile strength, hardenability, and toughness of the alloy. This element is critical in preventing brittleness and ensuring that P20 steel can withstand rigorous operational demands without compromising performance.
Additionally, P20 steel includes minor amounts of Silicon (Si) around 0.20% to 0.80%. Silicon contributes to strengthening the matrix of the metal and improves magnetic properties, which can be advantageous in certain applications.
Lastly, small quantities of Sulfur (S) and Phosphorus (P), generally below 0.030%, are present in P20 steel’s composition. While these elements are kept minimal due to their potential adverse effects on quality and performance if concentrations are too high, they play vital roles in improving machinability and reducing brittleness.
Properties of P20 Steel
P20 steel is prominently recognized for its distinctive blend of properties that make it an optimum choice for various tooling applications. Noteworthy among these are its excellent machinability, outstanding dimensional stability during heat treatment, and notable toughness. These characteristics derive from its unique chemical composition, tailored to deliver a balance of wear resistance and ductility.
One of the principal attributes of P20 steel is its remarkable ability to resist deformation under mechanical stress. This property is particularly beneficial in applications requiring precise dimensional control, such as injection molds and die-casting tools. The steel’s inherent toughness also minimizes the risk of crack formation during machining or operational use, thus extending the lifespan of tools made from P20.
Additionally, P20 steel exhibits a moderate level of hardness after quenching and tempering, which can be further optimized through specific heat treatment processes. Such a hardness level makes it resilient against surface wear while still allowing for repairs and alterations without significant difficulty. This characteristic is critical for prolonging tool life in rigorous working conditions.
Another advantageous property of P20 steel is its prehardened state when supplied. This prehardening eliminates the need for further heat treatment in many cases, thereby reducing production time and cost. Consequently, manufacturers can expedite the fabrication process of molds and dies without compromising on quality or performance.
The thermal conductivity of P20 steel merits attention as well. Superior thermal conductivity ensures more uniform heating and cooling during the manufacturing process, which aids in preventing thermal stress and maintaining the integrity of the workpiece’s dimensions.
Applications Of P20 Steel
P20 steel finds extensive application across various industries due to its optimal balance between cost, quality, and performance. This versatility is a defining aspect of P20 steel, allowing it to be used in numerous projects and products.
In the tooling industry, P20 steel is often the material of choice for injection molds and die casting. Its excellent machinability combined with good thermal stability makes it suitable for crafting complex shapes and designs which are fundamental in creating intricate parts and components. This makes it highly valuable for manufacturing molds that are used in the production of plastic products, where precision and durability are paramount.
Additionally, the automotive sector benefits greatly from the use of P20 steel. It is utilized in forming tools, holder blocks, and other components where resistance to wear under stress is required. The steel’s ability to withstand repeated cycles of heating and cooling without losing its integrity makes it ideal for manufacturing parts that must endure harsh operating conditions.
The electronics industry also takes advantage of the properties of P20 steel in creating casings and structural components for electronic goods. Its capacity to be polished to a high sheen enables manufacturers to achieve desired aesthetic qualities alongside functional requirements.
Furthermore, P20 steel’s adaptability extends to the manufacturing of prototype parts where speed and cost-effectiveness are crucial factors. Because it does not require rigorous heat treatments post-machining or during modification processes, timelines are significantly reduced without compromising on quality – making P20 a go-to option for rapid prototyping applications.
Despite its wide application range, selecting P20 steel necessitates consideration of its characteristics relative to project requirements ensuring optimal performance under specific conditions. Therefore, understanding its mechanical properties and limitations is essential when deciding on its use for industrial or commercial purposes.
Pros Of P20 Steel
- Excellent Machinability: P20 steel offers outstanding machinability, making it easier to cut and shape compared to many other tool steels. This property reduces manufacturing time and costs.
- Uniform Hardness: P20 steel maintains uniform hardness throughout, ensuring consistent performance and longevity of molds or tools. This minimizes the risk of unexpected failures and associated downtime.
- Exceptional Weldability: P20 steel exhibits strong weldability without the need for preheating, simplifying welding procedures and reducing preparation time.
- Strong Wear Resistance: Tools and molds made from P20 steel demonstrate robust wear resistance, enabling them to withstand rigorous use over extended periods. This durability contributes to longer product lifecycles and cost savings.
- Easy Availability: P20 steel is widely recognized and used in various industrial sectors, making it readily available from suppliers. This accessibility ensures projects can proceed without delays caused by sourcing issues.
Cons Of P20 Steel
- Low hardness: Compared to other tool steels, P20 steel has relatively low hardness, which may result in quicker wear and potentially increased maintenance needs.
- Reduced toughness at higher hardness levels: While P20 steel is machinable, it can become more brittle when heat-treated to increase hardness, making it prone to cracking or breaking under high stress or impact.
- Weldability concerns: Although P20 steel is weldable, improper welding techniques can weaken the weld joint, leading to potential cracking issues.
- Limited resistance to corrosion: P20 steel has limited resistance to corrosion, which may require additional protective coatings or alternative materials in corrosive environments.
- Balancing advantages and limitations: While P20 steel offers several advantages for tooling applications, its limitations regarding hardness, brittleness, weldability, and corrosion resistance must be considered when choosing materials for specific projects.
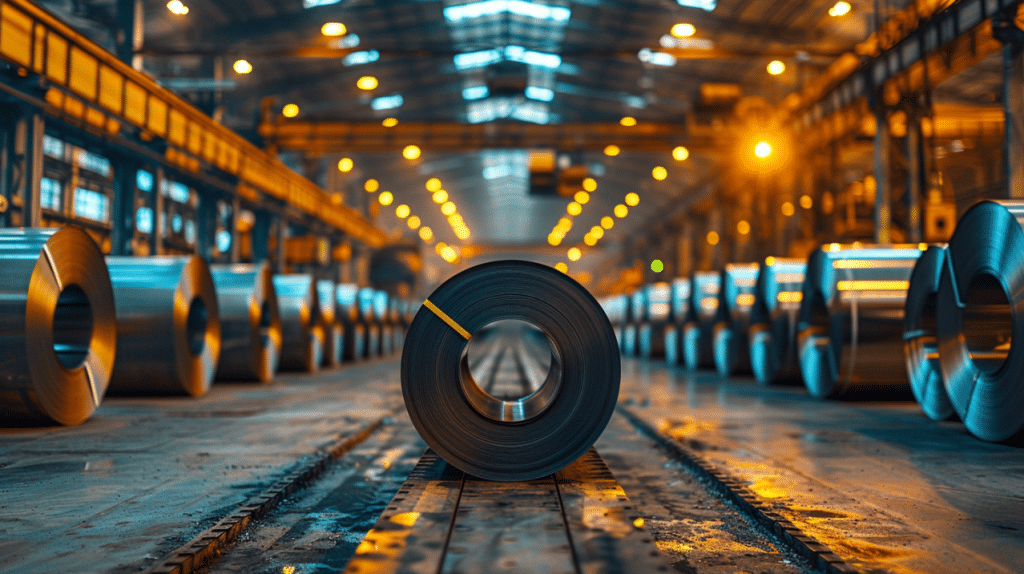
What Is 718 Steel
718 steel, often recognized in the industry for its remarkable versatility and performance, stands out as a distinguished material used across various high-demand applications. This particular alloy is engineered to offer a unique balance of strength, ductility, and resistance to corrosion and wear. It has become a cornerstone in the fields requiring materials that can withstand harsh conditions while maintaining their integrity over extended periods.
A distinguishing feature of 718 steel is its ability to retain considerable strength at elevated temperatures. This characteristic is due to its sophisticated chemical composition, which carefully balances elements such as nickel, chromium, and molybdenum. The presence of these elements not only imparts exceptional mechanical properties but also contributes to 718 steel’s renown for durability and longevity under stress.
Another key aspect of 718 steel lies in its adaptability during fabrication processes. Despite its substantial toughness, this alloy can be efficiently worked using standard machining techniques. This workability makes it an appealing option for industries that demand precision-engineered components with complex geometries.
Moreover, 718 steel exhibits excellent weldability. This feature simplifies the construction and repair of components made from this material, ensuring that structures or parts can be seamlessly joined without compromising their operational integrity. The ease with which it can be welded opens up further possibilities for its application in designs that require robust yet intricate assemblies.
In terms of applications, 718 steel finds widespread use in environments where materials are subjected to extreme pressures and temperatures. From aerospace engineering to petrochemical industries, this alloy continues to play an essential role in innovations that push the boundaries of modern technology and industrial capabilities. Given its comprehensive set of desirable attributes, 718 steel remains a preferred choice among engineers and designers seeking to optimize the performance and reliability of their projects.
Chemical Composition Of 718 Steel
The primary elements found in 718 steel include nickel (Ni), chromium (Cr), and iron (Fe) as the base constituents. Nickel, making up a substantial percentage of the alloy, is pivotal for enhancing the material’s overall strength and resistance to a wide range of temperatures. Chromium contributes to the alloy’s excellent corrosion resistance, making it more durable in harsh working environments.
In addition to these elements, 718 steel also contains smaller but significant amounts of molybdenum (Mo), which enhances the material’s tensile strength and hardness. Furthermore, niobium (Nb) combined with titanium (Ti) and aluminum (Al) are included to facilitate age-hardening processes that significantly improve mechanical properties such as fatigue strength and creep resistance.
Phosphorus (P) and sulfur (S) are present in minimal amounts, generally controlled at low levels to avoid adverse effects on the steel’s ductility and toughness. Meanwhile, carbon (C) is also kept at moderate levels to ensure an optimal balance between hardness and machinability.
This intricate blend of elements within 718 steel’s composition carefully balances its mechanical properties to meet stringent performance criteria required by various industrial sectors. The synergy between these components makes 718 steel a versatile material capable of performing under extreme conditions while maintaining integrity and reliability.
Properties of 718 Steel
718 steel is renowned for its remarkable combination of properties that make it highly valuable across various high-performance applications. This special tool steel stands out for its exceptional hardness, which directly translates into superior wear resistance. This property alone makes 718 an ideal material for tools and dies that encounter high levels of stress and abrasion during operation.
Another notable feature of 718 steel is its impressive toughness. Unlike some materials that may be hard but brittle, 718 maintains a level of flexibility. This toughness helps avoid sudden failure or cracking under impact or stress, ensuring reliability in demanding conditions.
Furthermore, 718 steel showcases good dimensional stability during heat treatment processes. This characteristic is critical for precision components, where exact dimensions must be maintained despite the application of high temperatures. The ability to resist thermal distortion means components made from 718 steel retain their specified tolerances and shapes even after thermal cycling.
Additionally, thermal resistance is a key attribute of 718 steel, allowing it to maintain structural integrity and mechanical properties at elevated temperatures. This quality is especially valuable in applications such as aerospace and automotive industries where materials are often subjected to harsh operating environments.
Lastly, the corrosion resistance of 718 steel extends its utility by providing durability in corrosive environments, reducing the need for frequent replacements and maintenance. Whether exposed to acidic substances or moisture-heavy environments, 718 continues to perform effectively, which enhances lifespan and reliability.
Applications Of 718 Steel
718 steel, often recognized for its remarkable utility in specialized sectors, boasts a wide range of applications that underscore its versatile nature. This particular variety of steel is commonly utilized in industries where superior strength and corrosion resistance are paramount. Its noteworthy attributes make it an ideal candidate for use in the aerospace sector, where components require both durability and reliability under extreme conditions. Specifically, 718 steel is extensively employed in the manufacturing of gas turbine engines and high-strength fasteners, components that play crucial roles in aircraft operation.
In addition to its prominence in aerospace engineering, 718 steel finds significant applications within the energy field. Due to its excellent performance in high temperatures and pressures, it is well-suited for crafting equipment used in nuclear reactors and oil drilling operations. The material’s resilience against wear and tear ensures that machinery can operate efficiently for extended periods without succumbing to environmental stressors.
The automotive industry also capitalizes on the benefits offered by 718 steel. High-performance automotive parts such as gears, shafts, and other critical components are frequently made from this material owing to its ability to withstand rigorous conditions without compromising integrity. This not only enhances vehicle performance but also contributes to safety standards by ensuring component longevity.
Furthermore, the chemical processing industry appreciates 718 steel for its exceptional corrosion resistance, making it an excellent choice for fabricating containers that store corrosive substances. Its capacity to maintain structural integrity even when exposed to harsh chemicals underscores its value in environments where material degradation is a concern.
Given its myriad uses across several high-demand fields, 718 steel stands out as a material of choice for applications demanding unsurpassed strength, reliability, and resistance against environmental challenges. Its adaptability across diverse industrial sectors highlights not just its physical qualities but also its integral role in advancing technological progress and innovation.
Pros Of 718 Steel
- Exceptional high-temperature strength: Maintains integrity under significant thermal stress, making it ideal for aerospace applications.
- Excellent corrosion resistance: Resistant to rust and corrosive elements, suitable for marine and chemical environments.
- High fatigue strength: Withstands considerable mechanical stress and cyclic loading conditions, enhancing reliability and lifespan.
- Good weldability: Simplifies fabrication process, allowing for greater design flexibility and efficiency in manufacturing operations.
- Cost-effective: Despite advanced properties, it is relatively cost-effective considering its lifespan and reduced maintenance needs.
Cons Of 718 Steel
- Cost factor: Due to its superior properties and complex production process, 718 steel generally comes at a higher price point compared to other tool steels like P20.
- Difficulty in machining: 718 steel’s exceptional hardness and toughness make it more challenging to machine than softer materials, often requiring specialized tools and techniques, leading to increased manufacturing time and costs.
- Precision required in heat treatment: Achieving desired mechanical properties requires careful control over heat treatment parameters, with an incorrect process potentially resulting in suboptimal material properties or failure.
- Challenges in weldability: Specific composition and potential for cracking during welding require special procedures and precautions to minimize risks, adding complexity to its use.
What Is The Difference Between 718 Steel And P20 Steel
Machinability and Workability
When comparing 718 steel to P20 steel in terms of machinability and workability, distinct differences emerge. P20 steel is widely renowned for its excellent machinability, which can be attributed to its uniform hardness throughout the material. This characteristic ensures a reliable and predictable process when machining, making it highly favored for complex tooling applications.
On the other hand, 718 steel also exhibits good machinability but tends to require more specific conditions to achieve optimal results. Factors such as cutting speed, feed rate, and the choice of cutting tool material can significantly impact the machining process of 718 steel.
Heat Treatment Processes
The heat treatment processes for 718 and P20 steels also present notable differences. P20 steel benefits from pre-hardening, which eliminates the need for further heat treatment after machining. This feature significantly reduces the risk of distortion or warping during the manufacturing process.
Contrastingly, 718 steel undergoes precipitation hardening, a heat treatment that enhances its strength and hardness. This method involves heating the steel to a high temperature followed by controlled cooling, which requires precise management to avoid compromising material properties.
Weldability and Formability
When considering weldability and formability between these two types of steel, P20 generally offers superior weldability without necessitating preheating. This makes it exceptionally suitable for various industrial applications where welding is critical.
Although 718 steel can be welded successfully, it demands greater attention to detail in terms of welding procedure specifications (WPS), including preheat and post-weld heat treatment (PWHT) requirements. Hence, welding operations with 718 might involve more complexities compared to working with P20.
Formability-wise, both steels exhibit good characteristics; however, due to its inherent hardness and strength properties after heat treatment, forming operations on 718 may require more robust equipment or specific techniques than those used for shaping P20 steel.
Cost
Finally, the cost factor significantly influences the choice between 718 and P20 steels. Generally speaking, P20 steel tends to be more affordable than 718 due to simpler production processes and widespread availability. Its cost-effectiveness combined with excellent mechanical properties makes it a popular choice for various applications within budget constraints.
In contrast, the price of 718 steel reflects its superior properties such as enhanced durability and resistance to extreme temperatures. These advanced features justify its higher cost; thus making it an investment in applications demanding these specific capabilities.
Understanding these critical differences—machinability workability,heat treatment processes,weld ability,and form ability,cost—between 718 steel and P20 steel aids in making informed decisions suitable for specific project requirements while balancing performance needs against budget considerations.
In Conclusion
In essence, 718 and P20 steel types serve distinct applications in the industry due to their differing mechanical properties and chemical compositions.
Explore our comprehensive guide on material selection for more insights on choosing the right steel type for your applications. Contact our team today to discuss how we can assist in optimizing your project’s performance with the most suitable materials.