In the realm of material science and engineering, selecting the appropriate material is critical for achieving desired mechanical properties, durability, and cost-effectiveness in manufactured products. P20 steel and aluminum are two widely used materials, each with distinct characteristics that make them suitable for various applications. This comparison aims to delineate the fundamental differences between P20 steel, a pre-hardened mold steel known for its excellent machinability and toughness, and aluminum, a lightweight metal renowned for its corrosion resistance and electrical conductivity. Understanding these differences is crucial for engineers, designers, and manufacturers to make informed decisions based on the specific requirements of their projects.
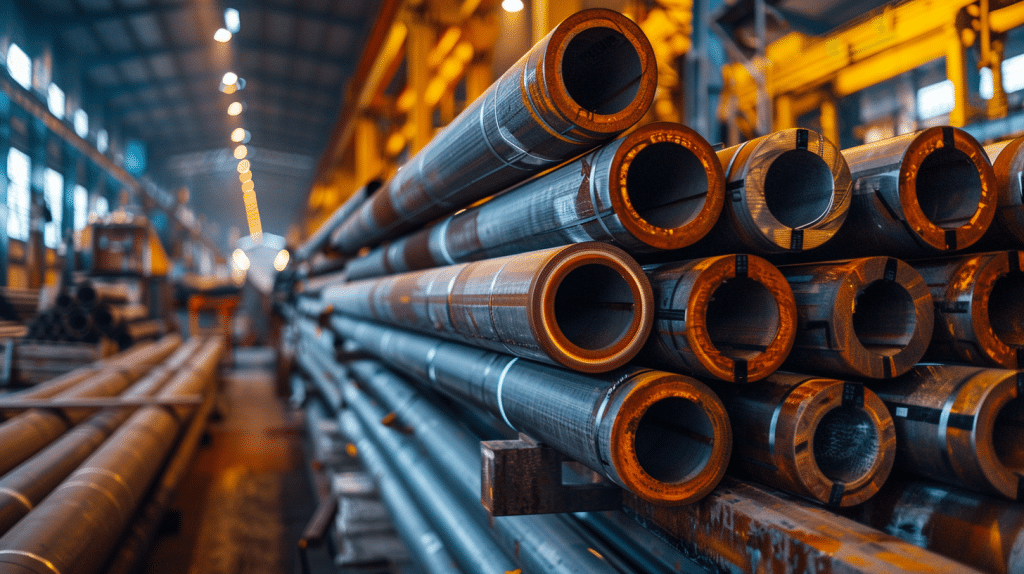
What Is P20 Steel?
P20 steel is a versatile, low-alloy tool steel that is widely utilized in the mold-making industry. Distinct for its unique combination of toughness, strength, and ductile properties, P20 steel stands out as a preferred choice for many engineers and manufacturers. This classification of steel is pre-hardened, meaning it doesn’t require any further heat treatment after machining, which significantly simplifies the manufacturing process.
The composition of P20 steel includes a mix of chromium, molybdenum, and nickel, which contributes to its excellent machinability and stable performance under stress. The presence of chromium adds corrosion resistance to its list of beneficial properties, while molybdenum enhances strength and hardness. Nickel is added to improve toughness—a critical factor when crafting molds that undergo frequent or heavy use.
One of the key appeals of P20 steel lies in its ability to be machined into complex shapes with minimal risk of distortion during the cooling phase. This feature is particularly valuable in the mold-making process, where precision and reliability are paramount. Furthermore, due to its pre-hardened state, molds made from P20 steel can be put into production much quicker compared to those requiring post-machining heat treatment.
Given these characteristics, P20 steel emerges as an indispensable material in industries where durability and speed are crucial factors. Its balanced composition ensures that it can withstand wear and tear while maintaining integrity over extensive use cycles—traits that underscore its prominence in mold making and tool crafting sectors.
Properties Of P20 Steel
- Good Machinability: One of the key attributes of P20 steel is its good machinability. This characteristic is particularly valuable in the manufacturing process because it allows for easier shaping and molding of the material into intricate designs without compromising its integrity or leading to significant wear on tools.
- Toughness: The toughness of P20 steel is another defining feature. It exhibits a robust resistance against cracking, which is critical in applications that demand high durability and longevity from the material. This toughness also contributes to P20’s good fatigue resistance, lending itself well to cycles of repeated stress without succumbing to failure.
- Optimal Hardness Balance: From a hardness perspective, P20 steel strikes an optimal balance that allows it to maintain structural integrity under pressure while still being flexible enough to withstand impacts without fracturing. This balance ensures that products made from P20 steel can endure demanding conditions while retaining their shape and functionality.
- High Thermal Conductivity: Thermal conductivity is yet another attribute where P20 steel excels. It has a relatively high rate of thermal conductivity compared with many other tool steels, facilitating efficient dissipation of heat during machining or when used in molds for plastics processing. This property significantly reduces cycle times during manufacturing processes by speeding up cooling periods.
- Weldability: Lastly, weldability is an important property of P20 steel that should not be overlooked. The material can be easily welded with minimal pre-heating, offering convenient repair options and adjustments during the tool-making process without compromising the final product’s performance.
Benefits Of P20 Steel
- Excellent Machinability: One significant advantage of P20 steel is its excellent machinability. This property allows for faster and more efficient processing in manufacturing environments, which can significantly reduce production timelines. The ease with which P20 steel can be machined also contributes to lower manufacturing costs, as less wear and tear on tools translates into savings on equipment maintenance and replacement.
- Durability: Durability is another hallmark of P20 steel, offering high strength and resistance to abrasion. This robustness ensures that tools and molds made from P20 steel can withstand rigorous use over extended periods without compromising integrity or performance. The material’s durability also means that products require less frequent replacements, providing long-term cost efficiencies for businesses.
- Excellent Polishability: P20 steel is distinctive for its excellent polishability, a critical feature in the creation of molds requiring smooth finishes. This characteristic ensures high-quality aesthetics in final products, making P20 an ideal choice for industries where surface finish is paramount, such as automotive and consumer goods manufacturing.
- Uniform Hardness: The uniform hardness of P20 steel across large sections further enhances its desirability. This attribute facilitates consistent performance across entire workpieces, thereby improving the reliability of products manufactured with this material. Uniform hardness also simplifies the heat treatment process, making it easier to achieve desired material properties without risking distortion or surface defects.
Applications Of P20 Steel
- Mold Making Industry: P20 steel is renowned for its excellent blend of toughness, strength, and machinability, making it a favored material in various industrial applications. Notably utilized in the mold-making industry, P20 steel offers the resilience and durability required for crafting high-quality molds. These molds are key components used in the production of plastic products, ranging from household items to intricate automotive parts.
- Tooling and Die-Casting Sectors: In addition to its predominant use in mold making, P20 steel finds applications in tooling and die-casting sectors. Its capacity to withstand prolonged exposure to moderately elevated temperatures without losing hardness makes it suitable for creating tools and dies that can endure rigorous manufacturing processes. This characteristic is particularly beneficial in industries where precision and longevity of tools are paramount.
- Construction Industry: The adaptability of P20 steel extends further into the manufacturing of holder blocks and formwork used in construction. Its ability to maintain structural integrity under stress while being easily machined into complex shapes allows for its use in producing components that require a balance between strength and flexibility.
- Special Machinery Parts: Furthermore, P20 steel’s unique properties facilitate its application in special machinery parts where wear resistance is critical. The automotive industry benefits from this aspect by incorporating P20 steel in the development of durable components capable of withstanding the harsh conditions of daily operation.
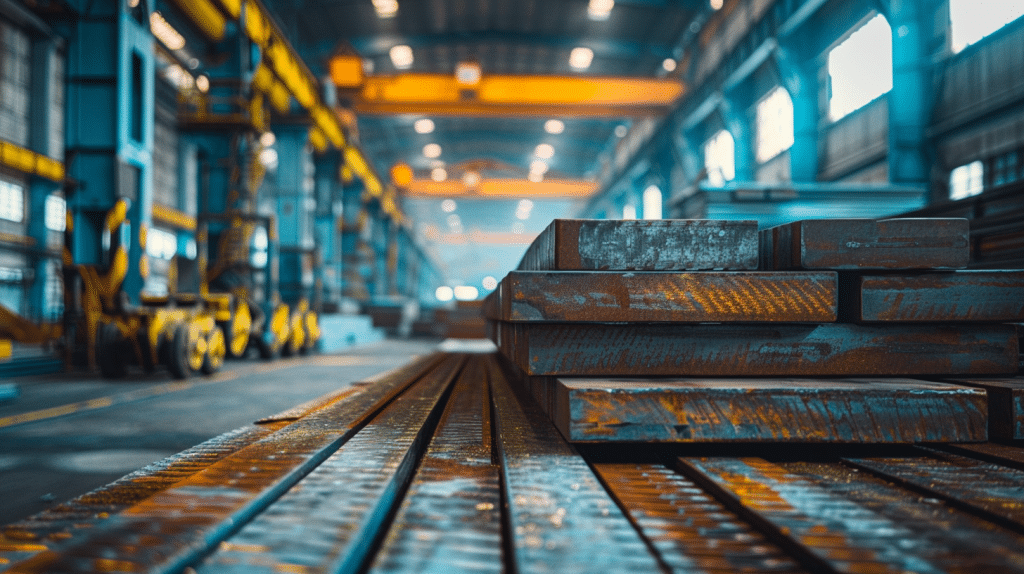
What Is Aluminum
Aluminum is a chemical element, represented by the symbol Al and atomic number 13. It is a silvery-white, soft, nonmagnetic metal that constitutes about 8.2% of the Earth’s crust and stands as the third most abundant element after oxygen and silicon. Due to its abundance, aluminum plays a crucial role in various industries and applications.
Aluminum is renowned for its lightweight properties compared to many metals, with approximately one-third the density and stiffness of steel. This characteristic makes it an ideal material for applications where weight reduction is necessary without sacrificing strength significantly.
Chemically, aluminum is highly reactive; however, it exhibits excellent resistance to corrosion due to the formation of a thin surface layer of aluminum oxide when exposed to air. This protective layer helps prevent further oxidation, making aluminum durable under varying environmental conditions.
Thermal conductivity is another notable property of aluminum. It conducts heat effectively, which is beneficial in applications such as heat exchangers in cars or cooling systems in electronic devices. Besides heat conduction, aluminum also possesses good electrical conductivity, making it a valuable material for electrical transmission lines.
From a manufacturing perspective, aluminum stands out for its workability. It can be cast, machined, formed into shapes with relative ease compared to many other metals. This flexibility in formability allows for its extensive use across numerous sectors.
Recycling holds particular importance when discussing aluminum; it is 100% recyclable without loss of quality. The recycling process consumes just 5% of the energy required to produce aluminum from raw materials, emphasizing its role in sustainable manufacturing practices.
Given these properties – lightweight nature, corrosion resistance, thermal and electrical conductivity, malleability/formability, and recyclability – aluminum has carved a significant niche for itself across various domains including automotive industries, construction fields, packaging solutions, and more.
Properties of Aluminum
- The low density of aluminum stands out as one of its most significant features. This metal boasts a density approximately one-third that of steel, making it ideal for applications where weight reduction is crucial without compromising strength. Its lightweight nature contributes to enhanced fuel efficiency in automotive and aerospace designs.
- Another noteworthy property of aluminum is its excellent corrosion resistance. When exposed to air, aluminum forms a protective oxide coating that shields the metal from further degradation. This natural barrier makes it particularly suitable for outdoor applications and in environments prone to corrosion.
- Aluminum also demonstrates outstanding ductility, allowing it to be easily formed into various shapes. This malleability enables manufacturers to utilize aluminum in a wide range of product designs, from thin foil packaging materials to complex aircraft components.
- Thermal conductivity is another area where aluminum excels. It effectively conducts heat, making it an invaluable material in heat exchange systems such as radiators and air conditioners. Additionally, this property is advantageous in cookware, where even heat distribution is essential.
- Electrical conductivity is yet another beneficial attribute of aluminum. Though not as conductive as copper, its significantly lower weight makes it an attractive alternative for power transmission lines.
- Reflectivity is also among the unique properties of aluminum. It efficiently reflects both light and heat, which finds practical applications in lighting fixtures and thermal insulation materials.
Benefits of Aluminum
- Strength-to-weight ratio: Aluminum boasts a remarkable strength-to-weight ratio, making it ideal for applications where reducing weight is crucial, such as automotive, aerospace, and structural industries.
- Corrosion resistance: Aluminum naturally forms a protective oxide coating, enhancing its durability and longevity, particularly in corrosive or weather-exposed environments.
- Conductivity: Aluminum is an excellent conductor of both electricity and heat, making it suitable for electrical transmission lines, radiators, air conditioners, and other cooling or heating devices.
- Recyclability: Aluminum can be recycled indefinitely without losing its properties, reducing environmental impact and making it a sustainable choice for eco-conscious projects.
- Ductility: Aluminum’s ductility allows it to be easily processed and shaped into various forms, enabling high levels of customization and precision in manufacturing processes.
- Aesthetic appeal: Aluminum’s capacity for surface treatments like anodizing or painting adds to its aesthetic appeal, making it suitable for a wide range of applications, from construction to consumer electronics.
Applications of Aluminum
- Automotive Industry: Aluminum is increasingly utilized in manufacturing parts such as engines, frames, and wheel rims in the automotive sector. Its lightweight nature significantly contributes to fuel efficiency and reduces greenhouse gas emissions without compromising performance or safety.
- Aerospace: Aluminum remains a material of choice for airframes, fuselage, wings, and other structural components in aerospace due to its high strength-to-weight ratio. This enables the production of lighter yet fuel-efficient aircraft capable of handling flight stresses.
- Construction Sector: Aluminum is favored in building materials for its resistance to corrosion, making it ideal for roofing sheets, window frames, doors, and structures exposed to harsh environmental conditions. Its ductility allows it to be molded into various shapes, suitable for architectural features requiring both aesthetics and durability.
- Consumer Electronics: Aluminum is heavily relied upon for casings and frames in consumer electronics due to its excellent heat dissipation properties. Products like smartphones, laptops, TVs, and home appliances often feature aluminum bodies, providing a balance between lightweight design and effective cooling capabilities.
- Packaging Materials: Aluminum is used in packaging materials such as foil containers or beverage cans, offering a sterile medium that protects food items from contamination while being fully recyclable. This addresses hygiene concerns in food packaging and promotes sustainability goals by reducing waste.
- Power Transmission Lines: Aluminum is utilized in power transmission lines for its excellent conductivity and lower costs compared to copper. This application underscores aluminum’s role in global energy efficiency efforts by enabling effective power distribution networks.
Key Differences Between P20 Steel And Aluminum
When deliberating between P20 steel and aluminum for a project, it’s essential to understand the key differences that could impact the material selection process. These differences span across durability and production life, heat conduction and cooling times, machinability and modification, as well as cost.
Durability and Production Life
P20 steel is renowned for its exceptional durability, which directly translates to a longer production life. This level of resilience makes it an ideal choice for tooling applications where wear resistance is crucial. On the contrary, aluminum, while being durable in its own right, does not quite match up to the robustness exhibited by P20 steel. This distinction in durability can significantly influence material selection based on the longevity requirements of the application.
Heat Conduction and Cooling Times
A notable property of aluminum is its high thermal conductivity, which means it can dissipate heat quickly compared to P20 steel. This characteristic is particularly beneficial in applications where rapid cooling of the material is desired. P20 steel, with its comparatively lower thermal conductivity, cools at a slower rate. The difference in cooling times can affect cycle times in manufacturing processes, making aluminum a preferred option when speed is of essence.
Machinability and Modification
Both materials present pros and cons regarding machinability and ease of modification. Aluminum stands out for its ease of machining due to its softness compared to P20 steel. This property allows for faster machining speeds and reduced wear on cutting tools. However, P20 steel offers superior stability during machining operations which might be required for producing intricate parts with high precision.
Cost
The decision between using P20 steel or aluminum often comes down to cost considerations as well. Generally speaking, aluminum tends to be more cost-effective than P20 steel due to differences in raw material costs and processing requirements. However, the initial savings gained by choosing aluminum might be offset over time due to its shorter lifespan compared to the more durable P20 steel.
Choosing The Right Material For Your Application
Selecting the ideal material for your specific application involves a careful consideration of various factors, each significant to the project’s success. P20 steel and aluminum, while both popular choices across industries, serve different purposes and their characteristics distinctly influence their suitability for particular applications.
When deliberating between P20 steel and aluminum, it’s crucial to weigh aspects such as the intended use of the finished product, the environment in which it will operate, and budget constraints. Each material brings its own set of advantages and limitations that could impact performance and longevity.
For applications that demand high durability and resistance to wear and tear, P20 steel is often favored due to its robustness. Its ability to withstand considerable stress makes it an excellent choice for tooling and molding operations that require a longer production life. However, if the primary concerns are weight reduction and corrosion resistance, aluminum emerges as the superior option. Its lightweight nature is particularly advantageous in automotive and aerospace industries where it contributes to fuel efficiency and ease of handling.
The production process itself should also be taken into account. Aluminum generally offers a quicker cooling time due to its excellent heat conduction properties which can significantly reduce manufacturing durations. On the other hand, P20 steel may require more complex machining but is easily modified which can be beneficial for bespoke projects or when modifications are anticipated during the lifecycle of the product.
Cost considerations cannot be overlooked as they often play a decisive role in material selection. Aluminum may offer cost savings both in terms of raw material expenses and shipping due to its lighter weight. Conversely, while P20 steel might come with higher initial costs, its durability could translate into lower replacement costs over time, presenting a better long-term investment.
In conclusion, choosing between P20 steel and aluminum hinges on a comprehensive assessment of the specific requirements of your application including mechanical properties needed, environmental conditions faced by the end product, manufacturing capabilities available, and budgetary limitations. A thorough analysis will enable you to make an informed decision that aligns with your project goals ensuring optimal performance and cost-efficiency.
What Is P20 Steel Equivalent To?
P20 steel is a popular choice in the mold-making industry, recognized for its exceptional blend of features. This material is equivalent to AISI P20 or DIN 1.2311, both known for their mold quality alloy steels. The characteristics of P20 steel, such as its excellent machinability, outstanding polishability, and solid hardness, make it a preferred option for professionals in mold making.
This steel doesn’t just meet the standard requirements; it is the benchmark. Its unique composition ensures that those working on intricate parts or needing a dependable material for their projects can rely on the consistency and high quality of P20 steel, synonymous with AISI P20 and DIN 1.2311.
Which Is Better Steel Or Aluminum?
Choosing between steel and aluminum hinges on the specific needs and priorities of your project. If your primary concern is strength and durability, steel typically takes the lead. Known for its robustness, steel is a go-to material for projects requiring long-lasting performance. Its strength makes it an excellent choice for heavy-duty applications. However, its heavier weight may be a disadvantage for certain projects.
Aluminum, in contrast, is lighter and boasts superior corrosion resistance. These properties make aluminum an ideal option for projects where minimizing weight and enduring the elements are paramount. Additionally, aluminum’s ease of machining and shaping allows for more design flexibility.
What Is The European Equivalent Of P20 Steel?
If you’re seeking a material akin to P20 steel for a project in Europe, look towards 1.2311 or 40CrMnMo7. This European grade mirrors the characteristics of P20 steel, known for its ease of machining and superior polishability. Both are pre-hardened mold steels, crafted specifically for mold creation, offering an admirable mix of toughness, strength, and thermal conductivity. These attributes render them suitable for a variety of uses, not limited to mold making alone.
Choosing 1.2311 in Europe is a practical move for projects requiring a material comparable to P20 steel. This option is widely accessible across Europe, ensuring your project’s needs are met without hassle.
What Is The Main Advantage Of Using P20 Steel For Injection Molds?
Choosing P20 steel for injection molds comes with a significant advantage: its outstanding durability. This robustness ensures that the molds can withstand high-volume production without showing signs of wear such as cracks. This feature is crucial for maintaining a smooth and efficient production line.
Another key benefit of P20 steel is its excellent machinability. This quality allows for easy modifications and repairs of molds, ensuring they maintain their integrity and perform optimally over time. The ability to quickly adapt or fix molds without compromising their quality can significantly reduce downtime and maintain productivity levels.
P20 steel also excels in resisting thermal fatigue. Injection molding processes involve frequent temperature changes, which can lead to damage in less resilient materials. P20 steel’s resistance to these fluctuations means molds made from this material maintain consistent quality across many production cycles. This durability reduces the need for frequent mold replacements, offering cost savings in the long term.
Opting for P20 steel for injection molds means choosing a material that combines reliability with cost-effectiveness. Its toughness, machinability, and resistance to thermal fatigue make it an ideal choice for sustaining high-quality, efficient production processes.
Can Aluminum Molds Be Used For High-Volume Production?
When considering the suitability of aluminum molds for high-volume production, it’s essential to focus on their distinct advantages. Aluminum stands out for its excellent thermal conductivity. This property significantly reduces cooling times, which can boost production speed. Such an increase in efficiency is a key factor for manufacturers aiming to meet the demands of large-scale production.
Aluminum molds also have the benefit of being lighter and more manageable than steel molds. This ease of handling can streamline various stages of the manufacturing process, from setup to actual production runs.
Despite potential concerns about their durability, advancements in aluminum alloys have addressed these issues. Modern aluminum alloys are designed for enhanced strength and wear resistance. These improvements ensure that aluminum molds can endure the rigorous conditions of high-volume production without compromising quality or performance.
How Does The Choice Of Material Affect The Overall Production Cost?
Selecting the right material for your project plays a critical role in determining the overall production costs. The decision between P20 steel and aluminum, for instance, has implications beyond the initial pricing.
Aluminum may attract you with its lower price tag, but it’s essential to factor in its physical properties. This material’s softer nature means it’s prone to quicker deterioration, which could lead to increased expenses over time due to the need for frequent replacements or repairs.
Conversely, P20 steel, despite its higher upfront cost, offers a level of durability that can translate into long-term savings. The strength of P20 steel reduces the likelihood of early wear and tear, potentially minimizing the need for costly maintenance or early replacement.
In making a material choice, it’s vital to look ahead. Consider not only the purchase cost but also how the material’s characteristics will impact maintenance expenses and the lifespan of the project. This broader perspective helps in making an informed decision that balances initial investment against future financial implications.
What Factors Should Be Considered When Deciding Between P20 Steel And Aluminum For A Specific Project?
When choosing between P20 steel and aluminum for your project, several crucial factors must be taken into account to ensure the success and efficiency of the final product.
The intended use of your product plays a significant role in material selection. If your project demands outstanding strength and longevity, P20 steel stands out as the superior option. Its robustness makes it ideal for high-impact applications. On the other hand, if minimizing weight is a priority without significantly compromising strength, aluminum emerges as the preferable material. Its lighter nature is beneficial for applications where ease of handling or fuel efficiency is critical.
The manufacturing process also influences the choice between these two materials. Aluminum is renowned for its ease of machining and forming, potentially reducing production times and associated costs. This characteristic of aluminum can lead to significant savings in both time and money during the manufacturing phase.
Cost considerations extend beyond the initial investment in materials. It’s essential to evaluate the total lifecycle and maintenance costs associated with your choice. While P20 steel may have higher upfront costs due to its durability and strength, aluminum could offer savings in terms of lower transportation and machining costs. However, it’s also important to consider the longer-term maintenance and replacement costs, especially in environments where the material may be subject to wear and tear.
Balancing these factors—end-use requirements, manufacturing processes, and cost implications—will help you make an informed decision between P20 steel and aluminum for your project, aligning with your specific needs and goals.
In Conclusion
In summary, while P20 steel offers exceptional durability and moldability for industrial applications, aluminum stands out for its lightweight and corrosion-resistant properties, making each material suited to specific needs.
Explore the advantages of P20 steel and aluminum in further detail to make an informed choice for your next project. Contact our experts today for professional guidance tailored to your specific requirements.