In the realm of tool-making and manufacturing, material selection is pivotal to achieving desired outcomes in durability, efficiency, and overall performance. Among the plethora of steel grades available, A2 and P20 stand out for their respective applications in cold work tooling and mold making. However, distinguishing between these two can be challenging without a thorough understanding of their properties and applications. This piece will elucidate the differences between A2 and P20 steel, focusing on their compositional distinctions, mechanical properties, heat treatment processes, and typical uses in industry. Our goal is to provide a concise yet comprehensive comparison that aids stakeholders in making informed decisions regarding material choice for specific tooling or manufacturing needs.
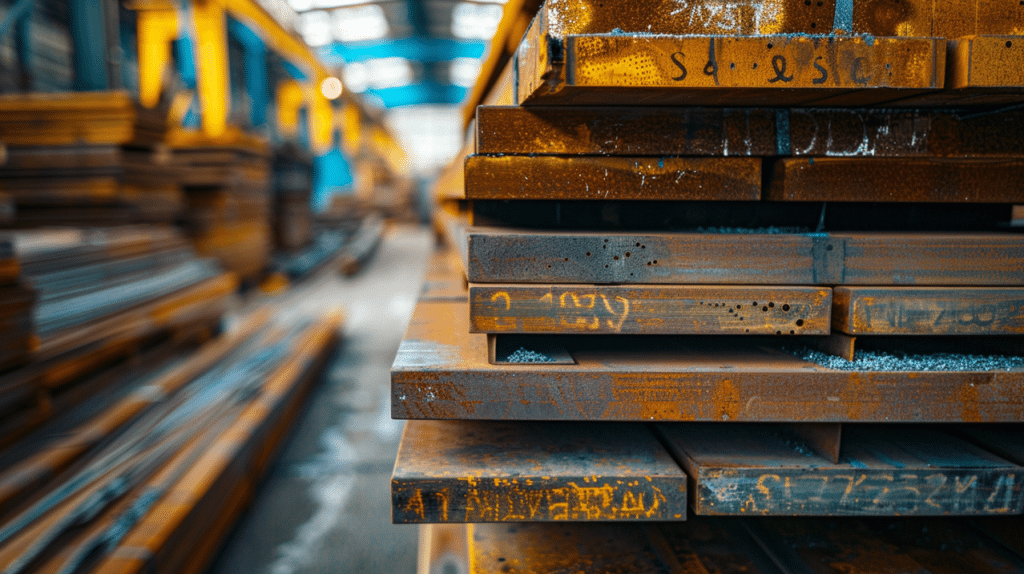
What Is P20 Steel
P20 steel is a widely recognized mold steel primarily utilized in the manufacturing of plastic injection molds and tooling. This material is well-appreciated for its excellent blend of strength, toughness, and wear resistance which are critical qualities for any material employed in mold-making. Its particular characteristics make it a go-to choice for industries working with plastics and similar materials requiring detailed molds.
The composition of P20 steel contributes significantly to its desirable properties. It is generally categorized as a low-carbon mold steel, with a carbon content typically around 0.4%. The alloying elements such as chromium, molybdenum, and nickel are added to enhance its hardness, toughness, and resistance to corrosive environments. These elements ensure that the steel can withstand the rigors of molding processes while providing a smooth surface finish on the molded products.
One of the distinguishing features of P20 steel is its ability to be used without further heat treatment. This pre-hardened state allows for immediate use in manufacturing processes without the need for additional treatments to achieve desired mechanical properties. Not only does this save time in the production cycle, but it also avoids potential distortion issues that may arise from heat treating already machined parts.
Additionally, P20 steel exhibits good machinability which simplifies the mold-making process. Its ability to be machined into complex shapes and sizes with precision makes it an invaluable resource in tooling applications where intricacy and accuracy are paramount. This level of machinability ensures that tools and molds can be produced efficiently and within tight tolerances – an essential requirement in high-quality plastic injection molding operations.
Chemical Composition Of P20 Steel
P20 steel is a versatile mold steel that is widely utilized in the tool and die industry. Its chemical composition is carefully engineered to offer a balanced combination of properties, making it suitable for a wide range of applications. The composition of P20 steel primarily includes carbon, chromium, molybdenum, and manganese.
Carbon plays a crucial role in the hardness and strength of the steel. In P20 steel, the carbon content typically ranges around 0.28% to 0.40%. This moderate amount of carbon contributes to good machinability while still maintaining decent hardness and toughness.
Chromium is another key component found in P20 steel, usually around 1.4% to 2.0%. Chromium enhances the steel’s hardness, tensile strength, and resistance to wear and corrosion. This makes P20 steel more durable under harsh working conditions.
Molybdenum content in P20 steel ranges from 0.2% to 0.5%. It significantly improves the material’s toughness and resistance to thermal shock by preventing brittleness at high temperatures. Molybdenum also increases the hardenability of the steel which allows it to be more uniformly hardened through heat treatments.
Lastly, manganese is present within a range of 0.6% to 1.0%. Manganese improves hardenability and counteracts brittleness from sulfur contamination in the manufacturing process. It also contributes to strength and wear resistance properties.
The tailored balance of these elements gives P20 steel its notable qualities such as good dimensional stability, excellent machinability, and robust versatility for various tooling applications including plastic injection molds, die casting dies, forging dies, and other types of industrial tools.
Mechanical Properties of P20 Steel
P20 steel is widely recognized for its distinctive mechanical properties that make it an ideal choice for various industrial applications. This tool steel is characterized by its impressive blend of toughness, strength, and durability, attributes that are crucial in mold making, tooling, and manufacturing sectors.
The core mechanical property of P20 steel is its excellent hardness. Typically delivered in a pre-hardened state, it exhibits a uniform hardness across the section. This property significantly reduces the need for further heat treatment processes post-machining which can save both time and costs. The hardness level in its as-supplied condition usually ranges between 280 to 320 Brinell (around 29 to 34 HRC), which makes it adept at resisting wear and tear during operation.
Another pivotal characteristic of P20 steel is its outstanding toughness. Unlike some other tool steels that may offer higher hardness levels but at the expense of increased brittleness, P20 maintains good toughness. This balance ensures that tools or molds made from P20 steel can withstand pressure and shock without fracturing or cracking under stress. Its resilience makes it particularly suitable for cavities and cores in injection molds where constant clamping pressure is applied.
Moreover, P20’s tensile strength falls within the medium range among tool steels. This means it has a commendable resistance to being pulled apart or elongated before breaking. It effectively bridges the gap between too brittle high-carbon steels and softer steels lacking sufficient wear resistance for many tooling applications.
Thermal conductivity is another important aspect when considering mechanical properties. P20 steel offers moderate thermal conductivity, facilitating efficient heat dissipation during processing activities such as plastic injection molding. This trait helps in maintaining mold temperature stability, enhancing part quality and consistency.
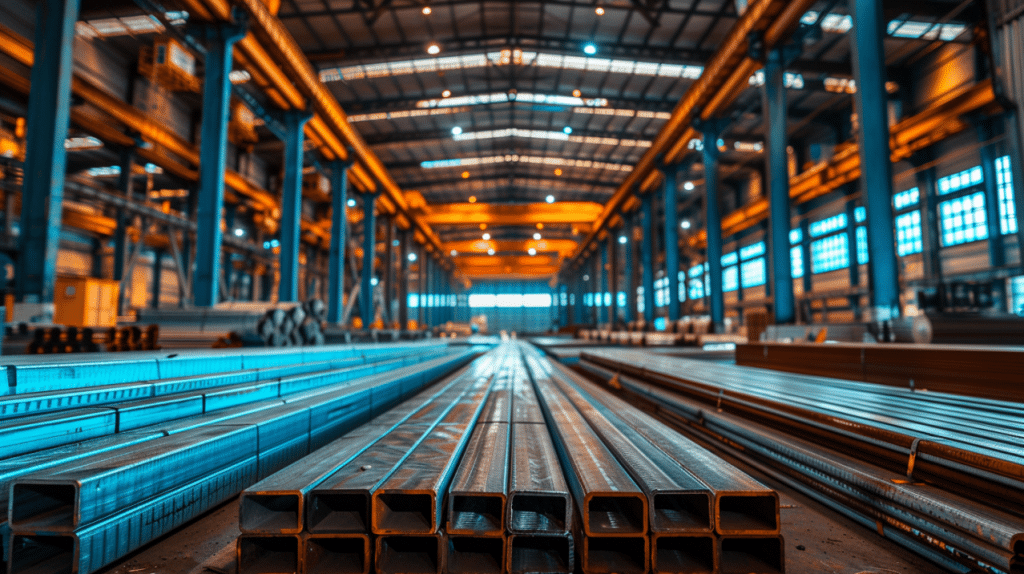
Applications Of P20 Steel
P20 steel is prominently known for its versatile applications in the tool and die industry. This unique steel grade boasts a well-balanced mixture of toughness, strength, and abrasion resistance which makes it a sought-after material in various manufacturing sectors.
In the realm of injection molding, P20 steel stands out as a preferred choice due to its exceptional polishability and photo-etching properties. These attributes allow manufacturers to achieve high-quality finishes on molds, which is crucial for producing intricate designs and smooth surfaces on plastic products. The ability to be polished to a very high standard renders P20 particularly suitable for clear or high-gloss components encountered in automotive lenses, consumer electronics casings, and medical devices.
Another significant application area of P20 steel lies within the construction of tooling for die casting. Its excellent machinability allows for the fabrication of complex dies that can withstand the stresses involved in casting metals under high pressure. The durability and wear resistance of P20 prolongs the life of dies, making it cost-effective for long production runs.
Additionally, P20 steel finds utility in the manufacture of holder blocks and mount plates used in complex tooling assemblies. Its dimensional stability during heat treatment makes it an ideal candidate for parts that demand precise tolerances.
Beyond the mold-making horizon, P20 steel is employed in making low-volume prototype models where materials with good machinability and minimal distortions post machining are paramount. This extends its applicability into sectors engaged in rapid prototyping where speed from design to production is critical without compromising on quality.
Overall, the spectrum of applications for P20 steel spans across various industries from automotive and consumer electronics to medical equipment manufacturing. Its selection as a material solution is often driven by its balance between formability, resilience, and aesthetic finish capabilities which are key requirements in modern manufacturing processes.
Pros Of P20 Steel
- Excellent polishability: P20 steel is known for its ability to achieve smooth finishes and high aesthetic quality, making it ideal for creating molds for products with superior surface qualities.
- Good machinability: P20 steel can be easily machined into complex shapes and sizes without compromising structural integrity, leading to quicker machining times and reduced production costs.
- Consistent hardness: P20 steel maintains uniform hardness distribution throughout the material, ensuring consistent performance and reliability, especially in applications requiring precise dimensional stability and mechanical strength.
- Good toughness: P20 steel exhibits good toughness, preventing cracks during machining or under stress conditions, and prolonging the life span of tools or components made from it.
Cons Of P20 Steel
- Lower hardness: Compared to other tool steels like A2, P20 steel has relatively lower hardness, impacting wear resistance and potentially requiring more frequent replacements or maintenance under heavy use conditions.
- Susceptibility to corrosion: P20 steel lacks the same level of corrosion resistance as some other tool steels due to its chemical composition, necessitating additional protective measures or coatings in corrosive environments.
- Reduced toughness: While P20 steel offers excellent machinability and ease of welding, it may exhibit reduced toughness under high impact forces or shock loading, limiting its use in applications requiring high impact resistance.
- Cost considerations: Although generally cost-effective due to its machining ease and lesser need for heat treatments, the initial expense of P20 steel may still be higher than some alternatives, which could be a concern for budget-constrained projects or applications where its superior qualities aren’t necessary.
What Is A2 Steel
A2 steel stands as a notable variant within the realm of tool steel, distinguished for its remarkable balance between toughness and wear resistance. This air-hardening tool steel finds its classification under the Cold Work category, attributed to its proficiency in operations that do not generate significant amounts of heat. The unique composition and treatment processes bestow upon A2 steel its esteemed position in industries where precision and durability are paramount.
The essence of A2 steel’s capability stems from its specific chemical makeup. Comprised primarily of carbon and chromium, it exhibits an ideal blend that facilitates both hardness and stability under working conditions. The presence of other elements such as manganese, molybdenum, and vanadium enhances its characteristics further, offering a refined structure that excels in demanding applications.
In terms of application, A2 steel is extensively utilized across various sectors due to its versatile properties. It is particularly favored for the manufacture of industrial tools and dies where high durability against wear is required without compromising toughness. The material proves itself indispensable in the creation of punches, gauges, and other precision instruments that demand a high degree of accuracy and longevity.
The pros encompassing A2 steel include an admirable wear resistance that ensures prolonged service life of tools crafted from it. Additionally, its ability to retain a sharp edge marks it as a preferred choice for cutting instruments. Despite these strengths, potential cons involve considerations like the material’s comparatively more challenging machinability relative to some other types of tool steels due to its hardness.
Chemical Composition of A2 Steel
The chemical composition of A2 tool steel is pivotal in defining its properties, performance, and applications. A2 steel, belonging to the group known as air-hardening, medium-alloy, cold work tool steels, features a distinctive blend of elements that contribute to its hardness, durability, and resistance to wear.
Carbon (C) content in A2 steel typically ranges from 0.95% to 1.05%, which is responsible for the material’s hardness and ability to retain an edge. Its chromium (Cr) content varies between 4.75% and 5.50%, offering enhanced corrosion resistance and increased toughness. Manganese (Mn), present in amounts from 0.40% to 1.00%, improves the steel’s tensile strength and hardenability.
Furthermore, molybdenum (Mo) at levels of 0.90% to 1.40% contributes significantly to the material’s strength at high temperatures and its resistance to wear. Vanadium (V), with a concentration around 0.15% to 0.50%, refines the grain structure and increases hardness by promoting carbide formation.
Silicon (Si) also plays a role, albeit smaller, usually found within a range of 0.10% to 0.50%. This element aids in strengthening the steel further without significantly affecting its toughness.
Phosphorus (P) and sulfur (S), while not major components, are kept at very low levels in A2 steel—typically below or close to 0.03%. These elements are generally considered impurities but can slightly enhance machinability when present in controlled quantities.
Each component within A2’s chemical makeup has been carefully balanced to produce an alloy known for its excellent stability during heat treatment, superior edge retention compared with other tool steels of similar hardnesses, commendable wear resistance even under adverse conditions, and satisfactory level of toughness against chipping upon impact.
Through this precise combination of elements, A2 steel distinguishes itself as an adaptable tool material used extensively across various industries for manufacturing tools that demand both durability against wear and resilience under impact stress.
Mechanical Properties of A2 Steel
A2 steel, known for its remarkable blend of properties, stands out due to its specific mechanical characteristics. This tool steel is highly appreciated for its toughness and ability to retain a sharp edge, which are essential qualities in various industrial applications.
One of the most notable mechanical properties of A2 steel is its excellent wear resistance. The presence of high carbon and chromium content contributes to this characteristic, providing durability in harsh working conditions. This feature ensures that tools and components made from A2 steel have a longer lifespan compared to those made from less wear-resistant materials.
Additionally, A2 steel displays considerable hardness after heat treatment, typically achieving levels around 57-62 HRC (Rockwell Hardness). This high hardness level makes it suitable for manufacturing cutting tools, dies, and punches where maintaining a sharp edge under stress is crucial.
The impact resistance of A2 steel is another critical factor contributing to its utility. Despite its hardness, this material can withstand significant impacts without cracking or chipping. This balance between hardness and impact resistance makes A2 a versatile choice for many demanding applications.
However, it’s important to note that while A2 steel has high toughness compared to many other tool steels, it may still be somewhat less tough than certain other options on the market. When selecting a material for specific applications, users must consider the trade-offs between hardness/wear resistance and impact toughness.
Applications Of A2 Steel
A2 steel, known for its resilience and durability, has a wide array of applications that capitalize on its unique properties. This tool steel is highly favored in industries requiring tools which endure wear and tear while maintaining precision.
One of the primary areas where A2 steel shines is in the manufacturing of cutting tools. Its exceptional wear resistance makes it an ideal material for the production of punches and dies used in the metalworking industry. These tools are subjected to high stress and need to maintain sharp edges and precise shapes over extended periods, making A2 steel’s ability to resist deformation under stress invaluable.
Beyond the scope of cutting tools, A2 steel finds its purpose in the fabrication of injection molds. The combination of toughness and wear resistance ensures that molds made from A2 steel can sustain numerous cycles without losing their integrity or causing defects in the products being molded. This reliability is crucial for manufacturers who rely on consistent output quality.
In woodworking, A2 steel’s toughness is advantageous for crafting durable woodworking tools such as plane blades and chisels. The material’s ability to hold an edge under extreme duress allows woodworkers to achieve clean cuts with minimal effort, enhancing both productivity and workmanship.
Furthermore, A2 steel is employed in the production of non-cutting tools such as shear blades, thread rolling dies, and coining dies. Each application benefits from the material’s distinctive blend of wear resistance and toughness, ensuring that tools perform well under the pressures of deformation and abrasion.
Additionally, certain specialty applications take advantage of A2 steel’s properties. These include but are not limited to cold forming tools, dowel pins, gauges, and even specific parts within automotive applications that demand high strength and durability.
Pros Of A2 Steel
- Excellent wear resistance and toughness: A2 steel offers a remarkable combination of these qualities, making it suitable for applications requiring durability and resistance to erosion or deformation under impact.
- High degree of hardness after heat treatment: A2 steel can achieve significant hardness levels, ensuring that tools and components maintain sharp edges and endure abrasive conditions over prolonged periods.
- Resistance to softening at high temperatures: This property enhances its appeal for high-performance applications where exposure to elevated temperatures is common.
- Air-hardening property: A2 steel is less prone to cracking during the cooling process compared to other high-carbon steels, simplifying heat treatment and contributing to the uniformity and stability of the end product.
- Good machinability: While slightly more challenging to machine due to its hardness, A2 steel maintains a balance that allows for the production of highly precise parts with minimal wear on cutting tools.
- Wide applicability: A2 steel finds usage in various industries including stamping, forming tools, punches, slitters, knives, and injection molding blades, highlighting its versatility across diverse operational needs.
Cons Of A2 Steel
- Susceptibility to corrosion: A2 steel has modest chromium content, which doesn’t provide the best resistance against corrosion. This requires diligent maintenance and preventive measures, such as regular oiling or coating, especially in moist environments.
- Difficulty in machining: A2 steel’s high toughness and wear resistance make it challenging to machine compared to softer materials. This can lead to increased time and cost in manufacturing processes requiring precise machining or shaping.
- Complex heat treatment: Achieving optimal properties in A2 steel through heat treatment requires precise control of temperatures and times. Incorrect heat treatment can result in reduced toughness or hardness, affecting its performance.
- Limited low-temperature impact resistance: A2 steel may not be ideal for applications requiring extreme impact resistance at very low temperatures. Other tool steels may outperform A2 in such conditions.
What Is The Difference Between A2 Steel And P20 Steel
Machinability And Workability
When analyzing the machinability and workability of A2 steel versus P20 steel, distinct characteristics emerge. A2 steel, known for its air-hardening property, typically presents more challenges in machining due to its higher hardness and abrasion resistance. Its rigidity often requires more robust tooling or specific machining strategies to efficiently work with the material without causing undue wear on tools. In contrast, P20 steel is pre-hardened and thus more malleable, facilitating easier machining and modification. This inherent tractability makes P20 a preferred choice in scenarios demanding intricate shapes and detailed mold work.
Heat Treatment Processes
The heat treatment processes for each type of steel reveal another layer of differentiation. A2 steel undergoes air hardening, which involves cooling in still air after being heated to a critical temperature. This process contributes to its dimensional stability but requires precise control over temperature to avoid potential warping or cracking. Conversely, P20 steel’s heat treatment is comparatively straightforward due to its pre-hardened nature, often only necessitating stress relieving after extensive machining or when welding is involved.
Weldability And Formability
Regarding weldability and formability, the distinctions continue. P20 steel offers superior weldability without the need for preheating; this quality, combined with its excellent formability, makes it highly suitable for complex molds and dies that require joining operations. A2 steel’s higher carbon content complicates welding efforts; it usually demands pre-heat and post-heat treatments to mitigate cracking risks—factors that can impact project timelines and costs.
Cost
Finally, cost considerations between these two steels factor into decision-making processes. Generally speaking, A2 steel tends to be pricier than P20 due to its higher alloy content and the more complex heat treatment it requires for optimal performance. However, the ultimate choice between A2 and P20 will depend on the project requirements—specifically considering where trade-offs between durability (favoring A2) against ease of use (favoring P20) might lie.
In Conclusion
In summary, A2 and P20 steels differ greatly in their applications and properties, with A2 being preferred for its wear resistance and P20 standing out in mold making due to its excellent machinability and polishability.
To fully appreciate the benefits of A2 and P20 steel for your specific needs, we encourage you to delve deeper into their characteristics. Reach out to our experts for a more detailed analysis on which steel type best suits your project requirements.