In the realm of steel materials used in various manufacturing and engineering applications, A4 and P20 steels stand out for their distinctive properties and uses. A comprehensive understanding of the differences between these two types of steel is essential for industry professionals when selecting the most appropriate material for their specific needs. This article aims to delineate the key attributes, applications, and performance characteristics that set A4 and P20 steel apart, facilitating an informed choice based on project requirements.
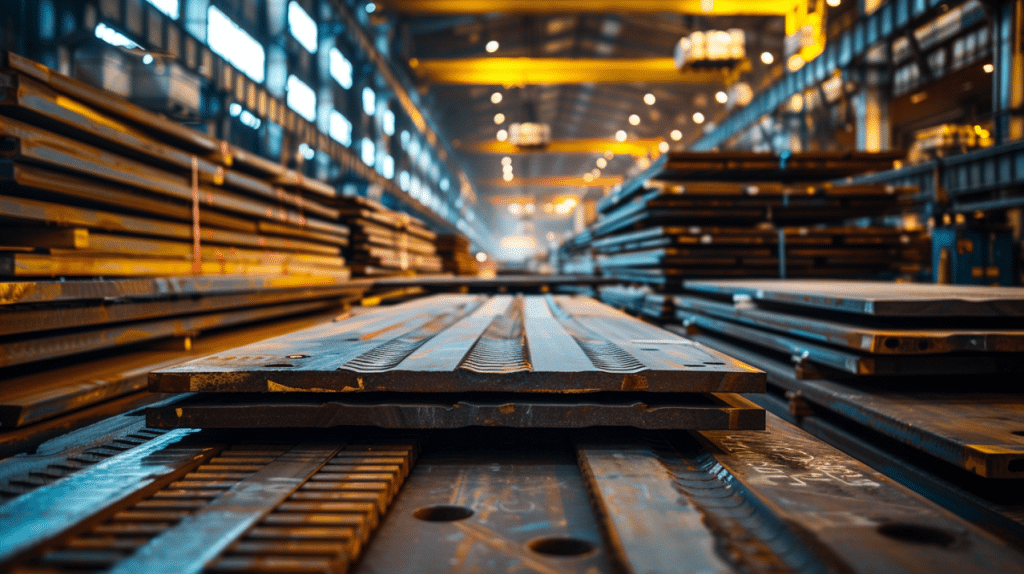
What Is P20 Steel
P20 steel, known for its versatility and widely used in the tooling and mold-making industry, stands out due to its distinctive combination of strength and ease of machining. This tool steel is a pre-hardened plastic mold steel that falls under the class of low-alloy steels. Its main appeal lies in its exceptional balance between hardness and toughness, making it an ideal choice for various manufacturing processes.
The composition of P20 steel is meticulously designed to facilitate both incredible toughness and sufficient hardness without necessitating further heat treatment after machining. This characteristic significantly reduces production times and costs associated with additional thermal processing.
Recognized for its reliable performance in cold-work tooling applications, P20 is frequently utilized in constructing holders, die sets, casings, and other components where resistance against breakage or wear is crucial. The steel’s adaptability extends beyond mere tool creation; it also finds application in injection molds where its polishability proves advantageous for creating high-quality surface finishes on molded parts.
A pivotal aspect contributing to the universal acceptability and use of P20 steel across various industries is its standardized quality. Despite fluctuating operational demands, this material maintains consistent performance levels thanks to its uniform hardening properties and robust structural integrity under stress.
Chemical Composition Of P20 Steel
P20 steel is classified as a low-carbon mold steel, and its composition is carefully balanced to optimize its performance. The primary elements found in P20 steel include carbon (C), chromium (Cr), molybdenum (Mo), and manganese (Mn). Carbon content in P20 ranges from 0.28% to 0.40%, which enhances the steel’s hardness while maintaining good ductility. This balance is crucial for mold steels that need to withstand repeated cycles without cracking or losing their shape.
Chromium is another vital element in P20 steel, present in the range of 1.4% to 2.0%. Chromium increases the steel’s hardness, toughness, and wear resistance, qualities essential for prolonging the life of molds and dies under harsh working conditions. Besides enhancing corrosion resistance, chromium also improves the steel’s response to heat treatment processes.
Molybdenum, ranging between 0.30% and 0.55%, plays a critical role in refining the grain structure of the steel and increasing its toughness. It helps improve the material’s strength at high temperatures, making it suitable for plastic injection molding processes that involve elevated temperatures.
Manganese content varies from 0.60% to 1.00% in P20 steel. Its presence contributes to improved hardenability and strength without making the steel too brittle—a key consideration for manufacturing large or complex molds that require precise dimensional stability.
In addition to these main elements, P20 may contain small amounts of silicon (Si) and phosphorus (P), with silicon aiding in strength and flexibility while phosphorus increases wear resistance.
Mechanical Properties Of P20 Steel
The hardness of P20 steel typically falls within the range of 28-32 HRC (Rockwell Hardness Scale) in its pre-hardened state. This level of hardness ensures that the steel can withstand significant wear and tear while still being relatively easy to machine, contributing to its popularity.
Tensile strength, or the resistance of the material to breaking under tension, is another critical mechanical property. For P20 steel, the tensile strength usually lies around 900-1100 MPa. This feature means that components made from P20 can endure substantial stresses without failure, making it suitable for use in molds that need to stand up to high pressures during the injection molding process.
Furthermore, P20 exhibits excellent ductility – the ability to stretch or deform without breaking. This property is vital in mold-making where precision and reliability are paramount. The enhanced ductility reduces cracking risks during manufacturing, ensuring longevity and reducing maintenance requirements.
Impact resistance is an essential consideration for materials used in tooling and molding operations since they often encounter sudden forces. P20’s good impact resistance supports its use in applications requiring high reliability under challenging conditions.
In terms of thermal properties, P20 maintains favorable characteristics. It has a relatively stable response to thermal cycling, which is common in injection molding processes where the mold repeatedly heats up and cools down. This stability helps prevent warping or distortion over time, further enhancing mold life.
Applications Of P20 Steel
P20 steel is renowned for its versatile applications in the tooling and mold industry, primarily due to its exceptional blend of toughness, hardness, and ductility which makes it a preferred choice for various manufacturing needs.
One of the primary uses of P20 steel lies in the fabrication of injection molds. Its ability to withstand the pressures and mechanical stresses associated with the injection molding process makes it an ideal material for creating large volume production parts that require minimal surface defects and high uniformity. Molds made from P20 steel are commonly employed in producing plastic components that find applications across automotive, consumer electronics, and household goods industries.
Apart from injection molding, P20 steel is also extensively used in making die casting dies. The consistent performance under thermal cycling conditions — heating and cooling — encountered during the die casting process ensures longevity and reliability of dies crafted from this material.
Furthermore, P20 steel finds its utility in constructing tool holders and guide rails owing to its excellent machinability. This allows seamless fabrication of intricate details without compromising on structural integrity or inducing undue stress on the tools being used.
Additionally, its adaptability to various finishing techniques including electroplating and polishing enhances its use in cosmetic molds where aesthetic considerations are paramount. This trait ensures that parts not only meet functional requirements but also appeal aesthetically when used in visible components of finished products.
Pros Of P20 Steel
- Superior machinability: P20 steel can be easily machined into complex shapes with minimal effort, reducing manufacturing time and cost.
- Excellent polishability: This steel offers outstanding polishability, making it ideal for applications requiring high surface finishes.
- Remarkable dimensional stability during heat treatment: Components made from P20 steel maintain precise dimensions even after thermal processes, ensuring uniformity and reliability in final products.
- Optimal balance between hardness and toughness: P20 steel exhibits a good balance between hardness and toughness, providing resistance to wear and the ability to absorb impact without fracturing.
Cons Of P20 Steel
- Sensitive to overheating: P20 steel can lose its temper if not properly managed during heat treatment, leading to reduced hardness and strength, requiring precise temperature control and potentially increasing manufacturing complexity and cost.
- Weldability challenges: While weldable with appropriate techniques, P20 steel requires special care to avoid cracking or distortion at weld sites, necessitating preheating and post-heating measures that can increase time and cost.
- Limited wear resistance: Compared to premium tool steels like D2 or S7, P20 steel may not offer the same level of durability against abrasive wear, potentially necessitating alternative materials for high-wear environments.
- Machinability limitations: While its lower initial hardness may seem advantageous for machining, the softer nature of pre-hardened P20 steel might limit its suitability for high-precision applications requiring rigidity and tight tolerances.
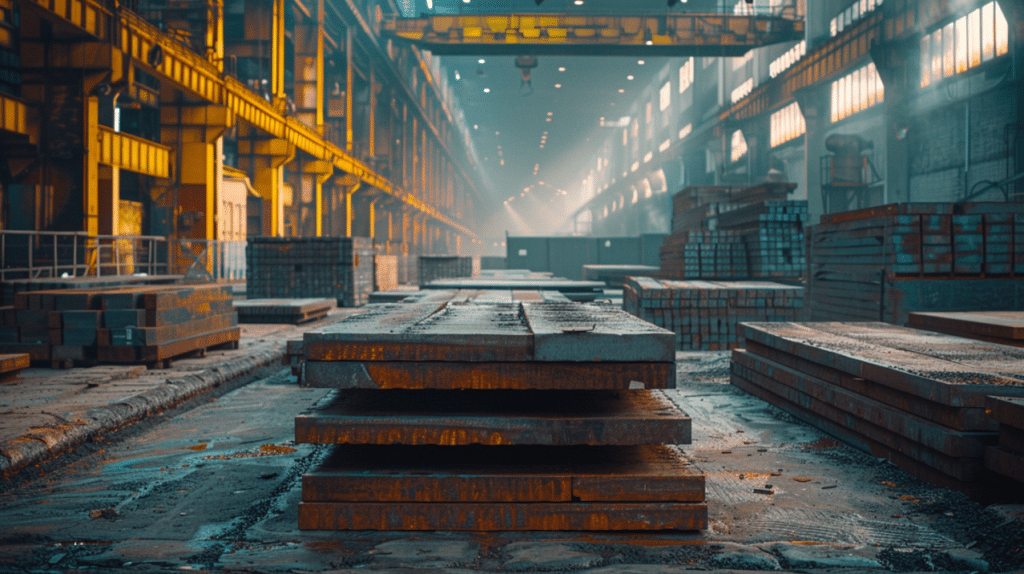
What Is A4 Steel
A4 steel, often recognized for its use in stainless steel fastener applications, stands as a noteworthy embodiment of high corrosion resistance and durability. Distinctively characterized by its chemical composition that facilitates enhanced performance in harsh environmental conditions, this grade of stainless steel is part of the larger 316 group. Its prominence arises from the balanced integration of elements that confer an exceptional level of protection against rust and decay.
The core attributes that define A4 steel pivot around its resilience and robustness, particularly in maritime environments where exposure to saltwater is a regular occurrence. This adaptability is not solely attributed to its innate corrosion resistance but also emerges from the meticulous alloying process it undergoes. The selection and proportioning of elements such as chromium, nickel, molybdenum, and others are meticulously calibrated to achieve this high degree of sustainability against corrosive agents.
Among the manifold advantages associated with A4 steel is its versatility. While primarily heralded for applications necessitating prolonged endurance against moisture and corrosive compounds, it exhibits qualities making it suitable for a wide spectrum of uses beyond mere fasteners. Surgical instruments, marine hardware, and components within the chemical processing industry underscore just a few realms where A4 steel finds relevance.
Its popularity also extends into architectural realms where both functional integrity and aesthetic considerations are paramount. Facade claddings, handrails, and support structures benefit greatly not only from its durability but also from its ability to maintain appearance over time despite exposure to environmental stressors.
Chemical Composition Of A4 Steel
A4 steel, commonly known as marine grade stainless steel, stands out for its remarkable resistance to corrosion and its wide utilization in environments prone to harsh weather conditions and saltwater. The chemical composition of A4 steel plays a pivotal role in granting it these valuable properties. Primarily composed of iron, A4 steel is alloyed with a significant amount of chromium (approximately 16-18%), which imparts the material with its distinct anti-corrosive characteristics.
Alongside chromium, nickel makes up about 10-14% of A4 steel’s composition. Nickel enhances the alloy’s formability and increases its corrosion resistance, particularly in alkaline environments. Additionally, the presence of molybdenum (2-3%) further boosts the steel’s resilience against chloride attacks – a common issue in marine settings.
Manganese is found in A4 steel at levels up to 2%, contributing to the material’s strength and hardness. Silicon, present up to 1%, improves strength without compromising flexibility. Moreover, carbon content in A4 steel is deliberately kept low (below 0.08%) to enhance weldability while minimizing carbide precipitation during welding processes.
Trace amounts of phosphorus and sulfur are also part of A4 steel’s makeup; however, their concentrations are strictly controlled. Phosphorus (up to 0.045%) improves machinability slightly but excessive amounts can reduce ductility. Sulfur content is maintained below 0.03% to avoid adverse effects on corrosion resistance.
Mechanical Properties of A4 Steel
A4 steel, often associated with stainless steel grade 316, stands out due to its remarkable corrosion resistance, attributed to its high molybdenum content. This feature makes it particularly suitable for use in environments exposed to chemicals and saline water. Furthermore, A4 steel exhibits excellent tensile strength, a critical attribute that describes the material’s ability to withstand tension without failing.
Yield strength is another pivotal mechanical property of A4 steel, representing the stress at which a material begins to deform permanently. This characteristic is essential for engineers when designing components that must not experience deformation under load conditions. A4 steel offers a favorable yield strength, ensuring reliability for structural applications where permanent deformation risks must be minimized.
Moreover, A4 steel delivers impressive elongation capabilities, indicating how much it can stretch before breaking. This ductility ensures that the material can undergo significant deformation before failure, an important aspect in applications requiring bending or shaping of the metal.
The impact resistance of A4 steel highlights its ability to absorb energy during impacts without fracturing. This property is invaluable in constructing safety-critical components that may experience sudden shocks or stresses.
In terms of hardness, A4 steel typically presents a balance between being hard enough to resist surface wear while remaining somewhat malleable. This balance prevents brittleness in applications where both durability and formability are needed.
Each mechanical property of A4 steel contributes to its suitability across various industries such as construction, marine environments, chemical processing, and any field demanding high corrosion resistance combined with reliable mechanical performance. These characteristics assure designers and engineers of a versatile material capable of meeting stringent project requirements.
Applications Of A4 Steel
A4 steel is extensively used in environments that demand high resistance to corrosion and a robust performance under adverse conditions. This grade of stainless steel, known for its formidable durability, finds applications across a broad range of industries and projects, underscoring its versatility and reliability.
In marine engineering, A4 steel is often the material of choice due to its exceptional resistance to saltwater corrosion. It is utilized in the manufacture of boat fittings, screws for wooden decks, and other hardware exposed to marine conditions. Its ability to withstand the corrosive effects of seawater makes it indispensable in this sector.
The architectural field also benefits from the use of A4 steel. It is selected for constructing facades, handrails, and fixtures that are exposed to the elements or human traffic. The aesthetic appeal of A4 steel combined with its resilience against weathering and corrosion contributes to its popularity in architectural designs.
Furthermore, A4 steel plays a critical role in the food processing industry. It’s used in equipment and appliances that come into contact with food products because it does not react with foods and maintains a clean surface that’s easy to sanitize. This non-reactivity ensures that there is no contamination or alteration in the taste or quality of the food being processed.
Another significant application area for A4 steel is within the medical industry. Surgical instruments, implants, and hospital equipment made from this type of stainless steel benefit from both its anti-corrosive properties and ease of sterilization. The high degree of cleanliness required in medical applications makes A4 steel an ideal choice.
Environmental management systems also rely on A4 steel for components like waste treatment plant machinery or atmospheric monitoring equipment where resistance to corrosive substances is crucial. In these contexts, durability means extended service life and reliability under challenging conditions.
Pros Of A4 Steel
- Excellent corrosion resistance: Particularly against chlorides and marine environments, making it ideal for marine applications.
- High temperature resistance: Can withstand temperatures up to approximately 870°C (1598°F) in continuous service, and intermittent service up to 925°C (1697°F).
- Strong and durable: Maintains structural integrity under high stress and impact conditions, reducing the need for maintenance over its lifecycle.
- Recyclable: Highly recyclable without degradation of quality, contributing to sustainability efforts.
- Aesthetic appeal: Surface finish enhances visual appeal and resistive properties, making it suitable for applications requiring cleanliness standards.
Cons Of A4 Steel
- Cost: A4 steel tends to be more expensive than many other types of steel due to its high chromium and nickel content.
- Machining difficulty: A4 steel is harder to cut, form, and machine compared to less alloyed steels, leading to increased labor costs and the need for specialized machinery or tools.
- Corrosion resistance limitations: While A4 steel offers excellent resistance to rusting and staining in many environments, it may not perform as well under extreme conditions or when exposed to certain chemicals.
- Reduced flexibility: A4 steel’s strength can lead to decreased malleability compared to other steels, making it less suitable for applications requiring significant bending or shaping without cracking.
What Is The Difference Between A4 Steel And P20 Steel
When evaluating the distinctions between A4 steel and P20 steel, we consider several crucial factors, namely machinability and workability, heat treatment processes, weldability and formability, along with cost variations. These elements play a vital role in determining the choice of material for various industrial applications.
Machinability and Workability
A4 steel is known for its impressive corrosion resistance which makes it a preferred material in environments subject to corrosive elements. However, this characteristic can sometimes affect its machinability compared to P20 steel. P20 steel, on the other hand, offers excellent machinability due to its uniform hardness. This makes it easier to shape and mold into various forms without significant wear on cutting tools.
Heat Treatment Processes
The heat treatment process also highlights significant differences between these two types of steel. A4 steel can undergo standard hardening processes but requires caution to prevent changes in its corrosion-resistant properties. Conversely, P20 steel is pre-hardened during production which minimizes the necessity for further heat treatment. This inherent hardness allows for immediate use in manufacturing without compromising structural integrity or needing extensive post-processing treatments.
Weldability and Formability
In terms of weldability and formability, both steels exhibit distinct characteristics that make them suitable for different applications. A4 steel’s chemical composition offers excellent weldability with appropriate techniques; however, care must be taken to avoid thermal distortion due to its lower thermal conductivity. P20 steel exhibits good weldability too but stands out more in terms of formability. Its consistent hardness allows it to be easily molded into intricate shapes without risking cracks or breaks.
Cost
Cost considerations often significantly impact the choice between A4 and P20 steels. Generally speaking, A4 steel tends to be more expensive than P20 due to its alloying elements that provide superior corrosion resistance. On the flip side, the cost-effectiveness of P20 steel makes it a go-to option for many manufacturers looking for a balance between performance and expense.
In Conclusion
In essence, A4 steel offers superior corrosion resistance ideal for maritime applications, while P20 provides excellent moldability and hardness suitable for tool and die making.
Discover the best material for your next project by considering the distinct advantages of A4 and P20 steel. Contact our expert team today to explore our range and find the perfect steel solution tailored to your needs.