Alloy steel stands at the forefront of material innovation, combining distinct elements to yield mechanical properties tailored for a plethora of applications. This comprehensive guide delves into the intricacies of alloy steel, unraveling its composition, classification, and the crucial role it plays across various industries. Utilization of this versatile metal has revolutionized sectors from automotive to aerospace – transcending conventional capabilities and setting new benchmarks in durability and performance.
What is Alloy Steel?
Alloy steel is a versatile and diversified type of steel that distinguishes itself from carbon steel through the addition of various alloying elements. These elements are integrated into the base iron and carbon composition to produce specific properties not achievable in plain carbon steels. Alloy steels are engineered to exhibit enhanced strength, hardness, wear resistance, and toughness, depending on the alloying elements used.
The primary distinction between alloy steel and other types of steel lies in its composition. While all steels contain carbon and iron, alloy steel also contains a deliberate amount of one or more other elements. These additional constituents serve to alter the material’s mechanical properties and contribute to its suitability for a wide range of applications.
For instance, adding chromium improves corrosion resistance and oxidative stability; nickel increases toughness; molybdenum enhances strength at high temperatures; vanadium contributes to wear resistance; and manganese improves hardenability as well as deoxidizes and desulfurizes the alloy. Each element serves a specific purpose, allowing manufacturers to tailor alloys to meet precise requirements.
Pros of Alloy Steel
Pros | Description |
---|---|
Enhanced Strength | Higher tolerance to stress ensures durability under heavy loads or impacts. |
Corrosion Resistance | Additional elements provide better resistance against rust and environmental degradation. |
Customization | Ability to develop specific attributes (hardness/toughness/temperature resilience) for tailored application needs. |
Good Weldability & Formability | Facilitates manufacturing complex parts with intricate geometries while maintaining material integrity during welding process. |
Improved Heat Treatment | Specialized heat treatments elevate mechanical properties like hardness and abrasion resistance further enhancing performance. |
Exceptional Wear Resistance | High-alloy variants with hard particulates in their structure offer superior longevity in wear-intensive use cases. |
Cons of Alloy Steel
Challenge | Explanation |
---|---|
Reduced Machinability | The presence of certain alloying elements can make alloy steel harder and tougher, which can lead to difficulties in machining and increased tool wear. |
Susceptibility to Corrosion | Some grades of alloy steel are not as resistant to corrosion as other materials, especially in environments with corrosive agents such as saltwater or chemicals. This limitation often requires additional coating or treatments. |
Cost | The process of adding alloying elements to enhance properties typically results in higher costs compared to carbon steels or other metals. Manufacturing processes involving heat treatment and surface treatments further add to the expense. |
Complexity in Heat Treatment | Alloy steel generally requires careful control during heat treatment processes such as quenching and tempering to achieve the desired mechanical properties. Inconsistent procedures may lead to issues like distortion or residual stresses. |
Weldability Concerns | Certain high alloy steels pose welding challenges due to their specific compositions, requiring specialized techniques and pre/post-weld heat treatment procedures for maintaining integrity. |
Availability of Material | Some specialized grades of alloy steel might not be readily available and may need to be special ordered, leading to longer lead times for projects. |

Alloying Elements & Their Effects
Alloy steel derives its versatile properties through the addition of various alloying elements, each contributing specific characteristics to the metal. The precise effects of these elements are crucial in determining the material’s suitability for different applications. Below is a detailed overview of common alloying elements and their individual impacts on alloy steel properties.
Element | Effect on Alloy Steel |
---|---|
Carbon (C) | Increases hardness and strength; can reduce ductility if added in high amounts. |
Chromium (Cr) | Enhances corrosion resistance, hardenability, and wear resistance; often used in stainless steels. |
Manganese (Mn) | Improves tensile strength and hardenability; acts as a deoxidizer and helps eliminate sulfur impurities. |
Nickel (Ni) | Adds toughness, strength at high temperatures, and corrosion resistance; stabilizes austenitic microstructures. |
Molybdenum (Mo) | Increases creep strength and hardenability; helps steel resist softening at high temperatures. |
Vanadium (V) | Boosts strength, wear resistance, and increases toughness by refining grain size. |
Tungsten (W) | Raises hardness at elevated temperatures and improves cutting efficiency in tool steels. |
Silicon (Si) | Contributes to spring properties by increasing strength and magnetic permeability while also serving as a deoxidizer during steel production. |
Aluminum (Al) | Acts as a grain refiner and deoxidizer; can improve nitriding characteristics for surface hardening treatments. |
Boron (B) | Significantly enhances hardenability at low concentrations without significantly affecting other properties. |
Cobalt (Co) | Improves red-hardness in high-speed steels which allows them to maintain hardness under extreme heating from rapid cutting processes. |
In addition to these primary ingredients, other elements like Copper (Cu), Titanium(Ti), Niobium(Nb), Nitrogen(N), Zirconium(Zr), Lead(Pb), Cerium(Ce), and others can also be found in trace amounts or specifically added for certain technical benefits.
Each element serves to fine-tune the mechanical performance of alloy steels, tailoring them to demanding conditions or specialized tasks that require precise material qualities such as increased surface durability or improved performance at extreme temperatures.
How Much Carbon is in Alloy Steel?
Low alloy steels typically contain carbon levels from 0.05% to 0.25%, a composition that imparts increased hardness while maintaining adequate formability. This balance of properties makes low alloy steel suitable for many structural applications where some toughness is required alongside strength and wear resistance.
In contrast, high alloy steels have carbon content ranging from 0.25% to about 2%. High levels of carbon confer greater hardness and strength but at a trade-off with reduced ductility — meaning the steel can become more brittle. Such compositions are often utilized in tools or applications where high wear resistance is paramount, and the brittleness can be mitigated by design or operational conditions.
It is important to note that the specific amount of carbon present can vary within these general ranges depending on other alloying elements added to achieve desired mechanical properties. The interaction between carbon and elements like chromium, nickel, molybdenum, etc., results in a vast spectrum of available steel grades tailored for various uses.
The precise quantity of carbon within each class also determines the most effective heat treatment processes for those alloys — with higher carbon contents typically requiring more aggressive quenching protocols to develop full hardness potential without leading to excessive brittleness.
Steel Type | Carbon Content |
---|---|
Low Alloy | 0.05% – 0.25% |
High Alloy | 0.25% – ~2% |
What Are the Main Types of Alloy Steel?
Alloy steel is primarily categorized into two main types, each comprising distinct characteristics, chemical compositions, and applications. These categories are low alloy steels and high alloy steels.
1.Low Alloy Steels
Low alloy steels are characterized by their smaller proportion of alloying elements when compared to high alloy steels. Typically, the total concentration of alloying elements is less than 5%. These materials are engineered to provide better mechanical properties and greater resistance to atmospheric corrosion than conventional carbon steel.
Common Low Alloy Steels
AISI/SAE Designation | Primary Alloying Elements | Typical Applications | Advantages |
---|---|---|---|
4140 | Chromium, Molybdenum | Automotive parts, Tools | Variety within tensile strength, good toughness |
5140 | Chromium | Fasteners, Automotive shafts | Moderate strength, superior fatigue properties |
8620 | Nickel, Chromium, Molybdenum | Gears, Crankshafts | Balanced mix for surface hardness and wear resistance, tough core properties |
4130 | Chromium, Molybdenum | Aircraft components | Excellent balance between strength and ductility, suitable for welded tube structures under stress |
4340 | Nickel, Chromium, Molybdenum | Aerospace parts | Superior toughness due to higher nickel content, ideal for heavy-duty aerospace components |
2.High Alloy Steels
High alloy steels are distinguished by their significant alloy content which typically exceeds 10% of the total composition. These steels possess superior corrosion resistance, mechanical properties, and can achieve high levels of hardness and strength. Their compositional complexity allows them to operate effectively in hostile environments where they may be subjected to pressure, elevated temperatures, or corrosive substances.
Common High Alloy Steels
Steel Grade | Main Alloying Elements | Key Characteristics |
---|---|---|
Stainless Steel (300 series) | Chromium (18%), Nickel (8%) – also known as 18/8 stainless | Excellent corrosion resistance, good formability |
Tool Steels (e.g., D2) | High carbon content, Chromium (>12%), Vanadium | High hardness and wear resistance |
Maraging Steel | Low carbon content, Nickel, Molybdenum, Cobalt | Exceptional strength and toughness; age-hardenable |
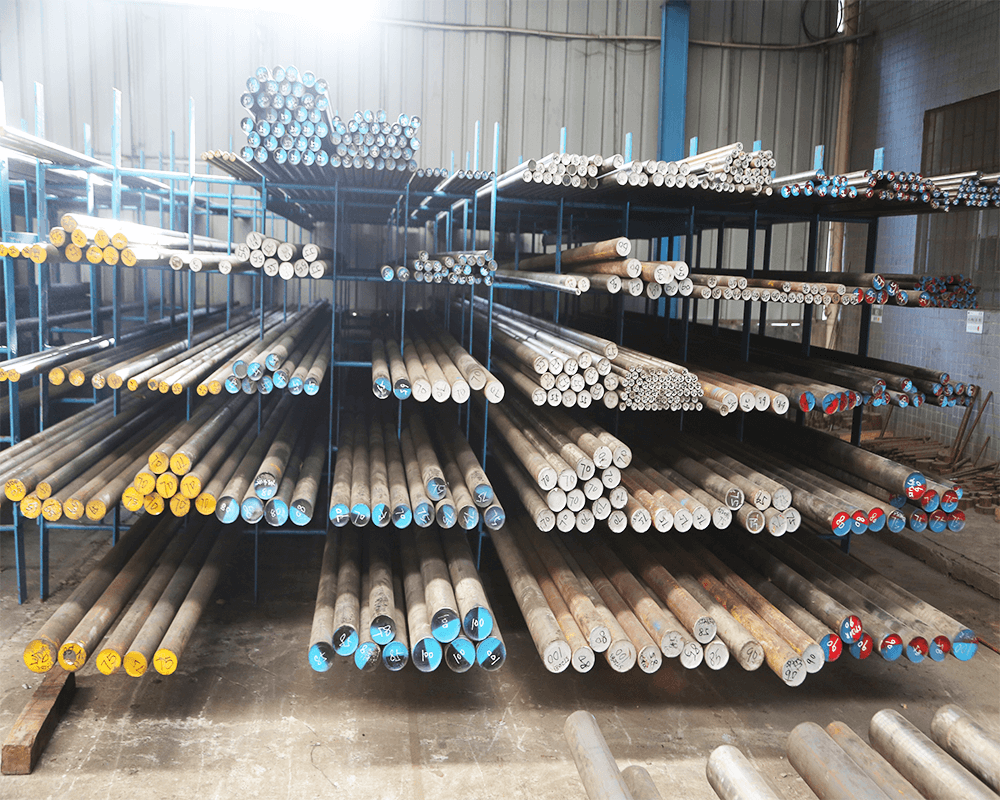
High & Low Steel Alloy Differentiating Qualities
The distinction between these categories primarily lies in their composition—specifically the percentage of alloying elements incorporated within the steel.
Low Alloy Steels | High Alloy Steels | |
---|---|---|
Alloy Content | Typically less than 5% total alloy content | Generally more than 8% total alloy content |
Carbon Content | Usually lower, often below 0.3% | Can vary significantly |
Strength | High strength compared to carbon steel | Very high strength, often at the expense of ductility |
Hardness | Hardened by heat treatment | May require more complex heat treatments |
Corrosion Resistance | Better than carbon steel but lower than high alloys | Excellent corrosion resistance |
Weldability | Good with pre and post-weld heat treatment | May require special welding techniques |
Cost | Generally less expensive | More expensive due to higher alloying component |
Low alloy steels usually contain one or more alloys such as chromium, nickel, or molybdenum which impart certain characteristics like enhanced strength and corrosion resistance. These traits make them suitable for use in environments where they’ll face stress but don’t necessarily require the utmost in corrosion resistance.
High alloy steels, on the other hand, typically have a considerable amount of elements such as chromium and nickel. Stainless steels fall within this category due to their minimum of 10-12% chromium content, which imparts remarkable anti-corrosive properties suitable for a wide range of applications even in very aggressive environments.
Manufacturing Processes of Alloy Steel
The manufacturing processes of alloy steel involve several steps that ensure the final product meets required specifications and performance expectations. Key stages include:
Melting and Casting
The initial stage in alloy steel production involves melting the scrap steel and iron, along with the specified alloying elements, in an electric arc furnace (EAF) or a blast furnace. Once molten, the steel is cast into molds to form ingots or it can be cast as a continuous strand which is subsequently rolled or forged into various shapes.
Hot Rolling
Following casting, hot rolling takes place, where the reheated ingots or continuously cast strands are passed through rollers at high temperatures. The desired thicknesses and shapes are achieved as the material becomes more malleable under heat.
Cold Rolling
For more precise dimensions and improved surface finishes, cold rolling is employed after hot rolling. This process occurs at room temperature using cold roll mills that compress the steel to thinner gauges without heating it.
Forging
To create parts of specific shapes and sizes with enhanced strength, forging is utilized. Heated to high temperatures but below the melting point, alloy steels are hammered or pressed into dies that shape the metal.
Annealing
In order to relieve internal stresses developed during cooling and to improve ductility for further processing, annealing may be performed. It involves heating steel to a particular temperature before slow cooling.
Heat Treatment
Heat treatment processes like hardening and tempering adjust mechanical properties such as hardness and toughness. Controlled heating followed by quenching rapidly cools down the material; tempering then re-heats it at lower temperatures to reduce brittleness while retaining its hardened state.
Machining
To achieve precision features, machining processes such as milling, drilling, turning or grinding remove excess material from alloy steel components to result in close-tolerance finishes.
Each process plays a crucial role in conferring certain characteristics on the final product — making it suitable for specific applications where strength-to-weight ratio, corrosion resistance or wear resistance are critical considerations. All steps must adhere to rigid quality control standards ensuring consistency and reliability of alloy steel materials used across various industries.
Is Alloy Steel Suitable for Injection Molding?
Alloy steel is not traditionally used for injection molding due to its high melting point and the complexity of handling and processing this durable material in its molten state. Metals commonly used in injection molding are typically non-ferrous like aluminum or zinc alloys because they have lower melting points and are easier to work with during the injection process.
For metal injection molding (MIM), which is suitable for small-sized complex components, alloy steels can be mixed with polymers (binders) to create a feedstock that can be more readily shaped at lower temperatures compared to pure alloy steel. After shaping, a secondary process removes the binder, and the component undergoes sintering at high temperatures, resulting in a final metal part.
Alloy steel’s density also poses greater challenges and costs related to equipment wear when undergoing an injection molding process; specialized machinery may be required to handle the increased stress associated with this durable metal.
What Temperature is Required to Harden Alloy Steel?
Hardening alloy steel is a critical heat treatment process that involves heating the steel to a specific temperature before cooling it rapidly, typically in water, oil, or air. The exact temperature required for hardening depends on the composition of the alloy steel and must be tailored to achieve the desired balance of hardness and toughness. Generally, this process occurs at temperatures between 750°C (1382°F) and 1300°C (2372°F).
Alloy steels are classified into different grades based on their properties and chemical composition which also informs their hardening temperatures. For instance:
- 4140 Grade: A medium-carbon alloy steel, popular for its balance of strength and toughness, usually requires a hardening temperature in the range of 830°C to 880°C (1526°F to 1616°F).
- 4340 Grade: A high-strength alloy known for its superior toughness and high fatigue strength, typically has a hardening temperature from about 800°C to 870°C (1472°F to 1598°F).
- 52100 Grade: Commonly used in bearing manufacturing due to its high wear resistance, often hardened at temperatures ranging from 790°C to 820°C (1454°F to 1508°F).
The process parameters such as heating rate, holding time at peak temperature, and quenching medium also play pivotal roles. Precise control over these factors ensures that distortion and stresses are minimized while achieving optimal hardness throughout the material.
To establish an exact hardening temperature for specific alloy steel grades, consultation with material data sheets or manufacturer recommendations is necessary. These resources will provide detailed guidelines on heat treatment practices aligned with the predefined characteristics of each grade. It’s important for engineers and metalworkers to access this information so they can apply appropriate treatments that maintain integrity while enhancing performance capabilities.
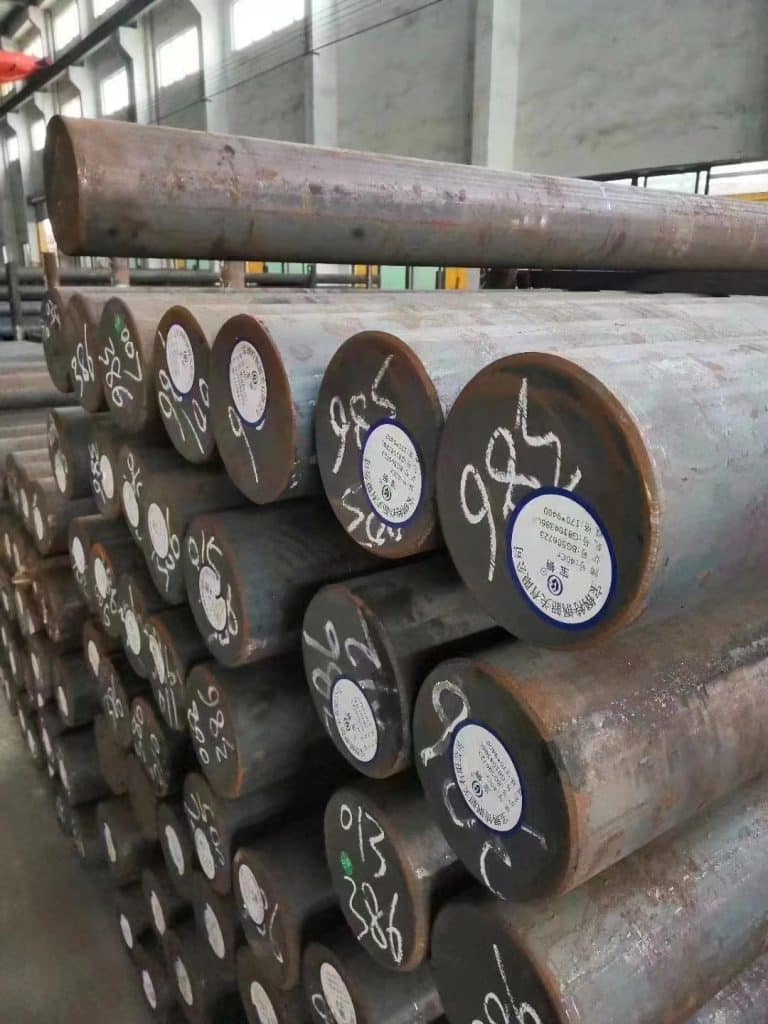
Applications of Alloy Steel
Alloy steel, known for its ductility, hardness, and tensile strength, is extensively used across various industries. Each sector capitalizes on the intrinsic properties that alloy steel provides, making it a versatile material for numerous applications. Here’s an overview of where you’re likely to find alloy steel being put to extensive use:
Industry | Applications of Alloy Steel |
---|---|
Automotive | Engine parts, gearboxes, frame components |
Construction | Beams, pipelines, reinforcing bars |
Energy | Drilling equipment for oil and gas extraction |
Aerospace | Turbine components, landing gears |
Railroad Engineering | Rails, wheels |
Defense and Military | Naval vessels, tanks |
Toolmaking Industry | Cutting tools such as drills and endmills |
Heavy Machinery Industry | Components subject to high stress like earthmoving equipment |
Alloy Steel Shape & Material Options
Alloy steel is highly versatile, not only in its composition but also in the range of shapes and material options available to industry professionals. Manufacturers offer alloy steel in numerous forms to meet various application requirements, such as sheets, plates, bars, rods, and tubes. Each form can be tailored through the addition or variation of alloying elements to possess specific properties needed for different industrial tasks.
Shape | Description |
---|---|
Sheet | Flat and thin; suitable for cutting into custom sizes and shapes |
Plate | Thicker than sheet; used where greater durability or heavier loads are involved |
Bar | Long piece with rectangular cross-section; often used for structural applications |
Rod | Circular or hexagonal cross-section; utilized in components requiring detailed machining |
Tube/Round Tubing | Hollow cylindrical shape; applied in structures needing a combination of strength and functionality |
Material options are closely tied to these shapes, varying primarily based on carbon content and the presence of specific alloying elements – each chosen for their contributions to hardness, ductility, tensile strength, resistance to wear and corrosion among other characteristics. Common alloying elements include chromium (Cr), nickel (Ni), molybdenum (Mo), vanadium (V), tungsten (W), cobalt (Co), aluminum (Al), manganese (Mn) and silicon (Si).
The alloy bar is a particularly prominent product form with grades such as 4140 and 4340 being widely recognized for their balanced attributes including toughness along with good fatigue strength – essential qualities for mechanical parts subjected to high stress conditions.
Industry-users must select the appropriate shape and material based on the operational needs they face. Whether it’s maintaining structural integrity under high pressure or ensuring longevity against environmental exposure, there’s an alloy steel configuration suitable for nearly every scenario encountered across diverse sectors like aerospace, automotive manufacturing, construction, and energy industries.
The Most Commonly Used Grades of Alloy Bar
Grade | Composition and Characteristics | Typical Applications |
---|---|---|
4140 Alloy Steel | Contains chromium, molybdenum, and manganese. Excellent toughness and high fatigue strength. | Automotive parts, gears, shafts, tools |
4340 Alloy Steel | High nickel content, exceptional tensile strength and toughness. | Aerospace components, aircraft landing gear |
304 Stainless Steel | Significant chromium content, corrosion-resistant. | Food processing equipment, chemical containers |
316 Stainless Steel | Enhanced corrosion resistance due to added molybdenum. | Marine equipment, pharmaceuticals, chemical industry |
D2 Tool Steel | High carbon and chromium content, superior wear resistance. | Cutting tools, dies, punches, industrial knives |
O1 Tool Steel | Good wear resistance, easier to sharpen than D2. | Woodworking tools, cutlery, hand tools |
These grades of alloy steel and stainless steel offer a range of properties suited to various industrial applications, allowing manufacturers to choose the most appropriate material for their specific needs.
In conclusion
In conclusion, alloy steel plays a pivotal role across diverse industries, offering a versatile blend of strength, durability, and corrosion resistance that caters to numerous applications. Understanding the vast range of grades and types is crucial in selecting the perfect material for your specific needs. Embrace the potential of custom-engineered solutions by leveraging our expertise in alloy steel.
For an in-depth consultation or to explore our extensive inventory tailored to meet your project demands, we encourage you to visit our website or contact us directly. Our dedicated professionals are on standby to provide you with insights and assistance that will shape the success of your endeavors. Make an informed decision by allowing us to guide you through the complexities of alloy steels with precision and excellence.