P20 steel, a versatile tool steel commonly used in various manufacturing processes, particularly in mold making for plastic injection molding, is known for its excellent balance of strength, hardness, and toughness. One crucial aspect affecting its performance characteristics and application potential is heat treatment. This article aims to clarify whether P20 steel can undergo heat treatment and outline the implications of such processes on its properties.
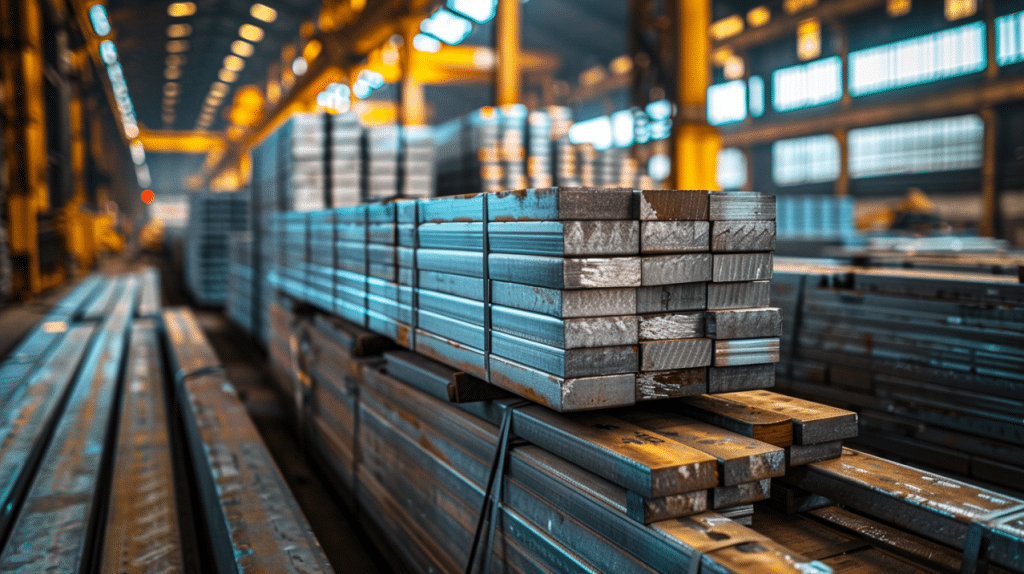
Importance Of Heat Treatment For Tool Steels
Heat treatment plays a pivotal role in the manufacturing and longevity of tool steels, which are extensively used in various industrial applications due to their durability, resistance to abrasion, and capacity to withstand high pressures. The primary rationale behind employing heat treatment processes for tool steels rests on its ability to significantly alter and enhance the material’s mechanical properties. Through meticulous thermal manipulation, manufacturers can achieve desired hardness, toughness, and strength levels in tool steels, making them more efficient and reliable for specific tasks.
One critical aspect of heat treatment is its ability to improve the wear resistance of tool steels. This improvement is achieved by changing the microstructure of the steel through processes such as annealing, quenching, and tempering. Each process serves distinct purposes; annealing reduces hardness and relieves stresses thereby increasing ductility; quenching increases hardness; while tempering adjusts the properties obtained from quenching to find a balance between hardness and toughness.
Additionally, heat treatment enhances the performance efficiency of tool steels by ensuring a uniform distribution of carbides throughout their structure. This homogeneity is essential for maintaining consistent performance across the entire surface of tools made from these steels, thereby minimizing any potential weak points that could lead to premature failure under operational stress.
Furthermore, processing tool steels via heat treatment also facilitates easier fabrication by improving machinability. Softening the material through certain heat treatment techniques makes it simpler to cut or shape, allowing for more precise manufacturing with reduced effort and lower costs.
Lastly, extending the lifespan of tools is another significant advantage offered by appropriate heat treatments. By optimizing their structural integrity and resistance to environmental factors such as corrosion or extreme temperatures, tools made from properly treated steel can maintain their functionality over longer periods without necessitating frequent replacements.
Types Of Heat Treatment Processes (Annealing, Quenching, Tempering)
Heat treatment processes are essential in modifying the properties of tool steels to suit specific applications. Among these processes, annealing, quenching, and tempering stand out due to their widespread use and significant impact on material properties.
Annealing
Annealing is a heat treatment process designed to reduce hardness, increase ductility, and relieve internal stresses within the steel. This process involves heating the steel to a specific temperature, usually above its critical point, and then allowing it to cool slowly. The slow cooling rate is crucial as it ensures the formation of a uniform microstructure, resulting in improved machinability and reduced brittleness.
Quenching
Quenching contrasts with annealing through its rapid cooling phase. This heat treatment process aims at increasing the hardness and strength of the steel. After being heated to an appropriate temperature—usually higher than that used in annealing—the steel is quickly cooled using water, oil, or air blast. The quick cooling leads to the formation of a hard martensitic structure but can introduce internal stresses and brittleness.
Tempering
Tempering follows quenching and seeks to balance out some of its downsides. In tempering, quenched steel undergoes reheating but only to a temperature below its critical point. This reheating serves to adjust the hardness attained through quenching while reducing internal stresses and increasing toughness. The specific temperature and duration of the tempering process are tailored according to desired material properties.
Can You Heat Treat P20 Steel?
Yes, it can be heat treated. This alloy is known for its excellent machinability in the annealed condition and ability to be modified through heat treatment processes. The primary goal when heat treating P20 steel is to enhance its mechanical properties for more demanding uses while retaining its machinability and stability.
Benefits Of Heat Treating P20 Steel
Increased Hardness
Heat treating P20 steel results in heightened hardness through processes like quenching and tempering. This increased hardness is crucial for tools and dies to withstand wear and tear over time, maintaining their shape and functionality.
Enhanced Toughness
Despite its increased hardness, heat-treated P20 steel retains or improves its toughness, crucial for tools facing high impact or stress. This balance prevents brittleness and reduces the risk of premature failure.
Improved Machinability
Post-heat treatment, P20 steel exhibits improved machinability, reducing tool wear and tear during machining. This efficiency leads to cost savings on tool replacement and labor while maintaining precision.
Better Dimensional Stability
Heat-treated P20 steel offers improved dimensional stability during service, reducing risks associated with dimensional changes due to temperature variations. Tools maintain their dimensions better over time, enhancing reliability and performance.
Resistance Against Fatigue Failure
Heat treatment improves P20 steel’s resistance against fatigue failure, increasing its cyclical load-bearing capacity. This makes it ideal for applications with repeated stress cycles, prolonging tool lifespan and ensuring consistent performance.
Heat Treatment Process For P20 Steel
The heat treatment process for P20 tool steel is a critical method used to achieve desired mechanical properties such as hardness, strength, and toughness. This operation enhances the material’s performance, especially in demanding industrial applications. The procedure typically involves several key steps: preheating, heating (austenitizing), quenching, and tempering.
Preheating
Preheating is the initial phase where P20 steel is gradually heated to a temperature range between 840°C (1544°F) and 870°C (1598°F). This step is crucial for minimizing thermal shock when the steel is subjected to higher temperatures. It also ensures more uniform heating during the austenitizing phase.
Austenitizing
During the austenitizing phase, the temperature is raised above the material’s critical point – usually between 870°C (1598°F) and 900°C (1652°F). At this juncture, the structure of the steel transforms to austenite. The duration at this temperature needs careful control to prevent grain growth which can negatively impact toughness.
Quenching
Following austenitization, quenching swiftly cools the P20 steel to create a hard martensitic structure. The cooling medium could be oil or forced air. Rapid cooling is imperative to achieve desired hardness levels but it introduces internal stresses and brittleness.
Tempering
To alleviate these stresses and reduce brittleness while retaining a good level of hardness, tempering is performed. This involves reheating the steel at a lower temperature range – typically between 550°C (1022°F) and 650°C (1202°F). The specific temperature within this range depends on the required balance between hardness and toughness for the application.
Each of these stages—preheating, austenitizing, quenching, and tempering—contributes significantly to enhancing P20’s final characteristics making it suitable for various tools and dies applications. Properly executed, these processes result in improved wear resistance, strength-to-weight ratios, and fatigue life of P20 steel components.
Precautions And Considerations In Heat Treating P20 Steel
When undertaking the heat treatment of P20 steel, a variety of precautions and considerations must be forefront in the planning process to ensure safety, material integrity, and desired outcomes. This high-quality tool steel is widely favored for its excellent machinability, stability, and toughness. However, achieving these desirable properties requires a meticulous approach to its heat treatment.
One of the initial considerations involves understanding the chemical composition and mechanical properties of P20 steel. This knowledge aids in predicting how the material will respond to various heat treatment processes such as annealing, quenching, and tempering. The precise control over heating rates, soak times, and cooling rates are critical factors that influence the success of the heat treating process.
Temperature management represents another crucial aspect. Overheating can lead to undesirable alterations in microstructure such as grain growth, which could potentially compromise mechanical properties like toughness and ductility. Therefore, maintaining an optimal temperature below the material’s melting point during heat treatment operations is essential.
Atmospheric control within the heating environment also demands attention. Protective atmospheres or vacuum furnaces might be employed to prevent unwanted surface reactions such as oxidation or decarburization. These surface changes can significantly impact fatigue strength and dimensional stability.
Moreover, post-heat treatment handling practices should not be overlooked. Rapid cooling or improper tempering temperatures may induce residual stresses within the P20 steel component leading to distortion or cracking during service life. Thus care must be taken in cooling procedures as well as subsequent tempering stages to mitigate these effects.
Given its versatile applications from injection molds to die casting tools, it’s imperative that any modifications through heat treating should aim at preserving or enhancing specific characteristics tailored to end-use requirements while avoiding detrimental alterations in structure or performance caused by improper thermal processing.
What Is The Melting Point Of P20 Steel?
P20 steel, known for its balanced ductility, toughness, and temperature resistance, has a melting range rather than a specific melting point. This characteristic is typical of alloy steels due to their complex compositions. For P20 steel, the melting range typically begins around 1,420°C (2,588°F) and extends up to approximately 1,460°C (2,660°F). This range can slightly vary depending on the specific composition and manufacturing process of the P20 steel in question.
What is P20 Steel Coefficient Of Thermal Expansion?
The coefficient of thermal expansion (CTE) of P20 steel is a critical property that defines how the material expands when heated and contracts when cooled. P20 steel, widely used in tool and mold making, has a CTE that typically ranges from about 11 to 13.5 x 10^-6/K (k-1) over the temperature range of 20°C to 200°C. This property is essential for designers and engineers to consider when developing components that will undergo temperature variations during their service life.
In Conclusion
In summary, P20 steel can indeed be heat-treated to enhance its hardness, toughness, and durability, making it suitable for various applications requiring high performance in molds.
To learn more about the specific procedures for heat treating P20 steel or to explore its applications further, please do not hesitate to contact us or visit our website. Our team of experts is ready to provide you with tailored solutions that meet your project’s unique needs.