Purchase D2/1.2379 mold steel solve the corrosion problem of molds with 30% glass fiber added.
This customer’s mold is injection molded of PA6 + 30% glass fiber. Previously, SKD61 mold steel was used for 300,000 mold times, and serious nap and gas corrosion occurred.
1. Adding 30% glass fiber to the rubber will seriously corrode and wear the mold. If the hardness of the mold steel is not high and the wear resistance is not good, it will be corroded quickly, causing the mold to be roughened. Repeated repairs will not work also.
2. The alloy composition of SKD61 mold steel is 4Cr5MoSiV1, with a carbon content of 0.38%. The quenching hardness is HRC50-52.
The hardness is low and the carbon content is low. After quenching and hardening, a large amount of hard carbide structure cannot be obtained and the wear resistance is poor. Therefore, It cannot resist the erosion of the mold by adding 30% glass fiber rubber.
The mold is easily eroded, causing burrs on the molded product.
3. For plastic molds that add 30% glass fiber, you must choose mold steel with non-stick material, high hardness (HRC54-58), and high carbon content to resist the erosion of the mold by 30% glass fiber.
4.D2 mold steel is an electroslag steel with no carbide segregation. The mold has a good finish and will not stick to materials.
There will be no adhesive wear of sticky materials and the mold will not be roughened.
It has high carbon content and a quenching hardness of HRC55-58, which can obtain a large amount of mold.
Hard carbide with good wear resistance can resist the erosion of the mold by adding 30% glass fiber.
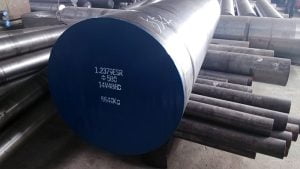
This customer used to make fiberglass molds using H13, SKD61, Cr12MoV and other mold steels to make fiberglass molds.
Because the molds always had burrs, they were often complained by customers. Later, they used D2 mold steel to solve the problem!