P20 steel is widely recognized for its strength, durability, and excellent machinability, making it a preferred material for mold making in various industries such as automotive, consumer electronics, and home appliances. Understanding the lifespan of P20 steel molds is crucial for manufacturers to anticipate maintenance requirements, replacement schedules, and overall production costs. This article provides an in-depth analysis of the factors affecting the longevity of P20 steel molds and outlines what users can expect in terms of service life under typical operating conditions.
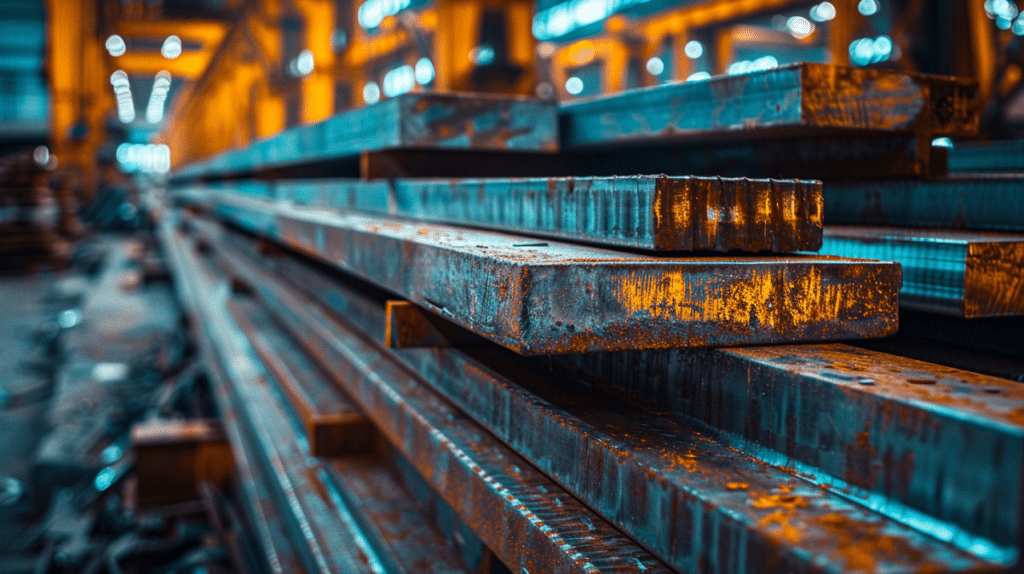
What Is P20 Steel?
P20 steel is a versatile pre-hardened plastic mold steel encompassing a series of characteristics that make it a prime choice for the mold manufacturing industry. Renowned for its excellent machinability, robustness, and uniform hardness across large sections, P20 stands as the default grade used for making tooling and molding applications.
The chemical composition of P20 steel includes chromium, molybdenum, and nickel which contribute to its outstanding properties such as good tensile strength, high toughness, and better wear resistance compared to other materials in similar applications. This unique blend ensures that the steel does not only perform well during the machining process but also maintains stability during thermal treatment processes.
One of the key advantages of using P20 steel in molds is its ability to receive a polish that results in a superior finish on the molded products. This characteristic is particularly beneficial when producing items that require high aesthetic standards or intricate detailing.
Due to its pre-hardened state, P20 reduces the need for heat treatment processes after machining which can save significant amounts of time and reduce costs in the mold-making cycle. It’s precisely this combination of hardness without brittleness and machinability that positions P20 as an adjustable fit for a wide array of molding tasks ranging from simple prototypes to complex production tools.
Average Lifespan Of P20 Steel Molds
Typically, a well-manufactured P20 steel mold can last anywhere from 300,000 to 1,000,000 cycles under ideal conditions.
Factors Influencing The Lifanspan Of P20 Steel Molds
The durability and performance lifespan of P20 steel molds are influenced by several critical factors, each contributing in its unique way to the overall efficiency and longevity of the mold. Understanding these variables is essential for optimizing mold use and extending its operational life.
Quality Of P20 Steel And Manufacturing Precision
The foundational element impacting a mold’s lifespan begins with the quality of P20 steel utilized and the precision involved during its manufacturing process. High-quality P20 steel, recognized for its excellent machinability, toughness, and wear resistance features, forms the core basis for a durable mold. Precise manufacturing practices ensure that each part of the mold meets stringent specifications, reducing potential defects that could compromise longevity.
Complexity And Design Of The Mold
The complexity and intricate design of a mold strongly correlate with its potential wear and durability concerns. More complex molds with tight tolerances or small features tend to face higher stress levels during operation. Such designs necessitate regular scrutiny to preempt failure modes linked to fatigue or mechanical wear. Simple designs usually afford easier maintenance routines and potentially longer lifespans due to reduced structural stress.
Type Of Plastic Material Being Molded
Different plastics exert varying stresses on molds based on their physical characteristics such as viscosity, abrasiveness, and required processing temperatures. Engineering plastics that are inherently abrasive or need high temperatures for shaping can accelerate wear in molds, especially if not designed with these conditions in mind. Selecting appropriate mold materials and design relative to the plastic being molded is crucial in minimizing undue stress on the tool.
Frequency Of Use And Cycle Time
The operational schedule of the mold – specifically, how often it is used and its cycle time – directly affects its service life. High-frequency use with short cycle times subjects molds to continuous thermal cycles and mechanical stress, hastening wear and tear processes. Adjusting operational parameters to manageable levels can significantly decelerate deterioration rates.
Maintenance Practices And Handling
Lastly, diligent maintenance practices alongside careful handling of P20 steel molds play a pivotal role in extending their usable life. Regular cleaning ensures that residues do not build up within the cavities; proper lubrication minimizes friction-related wear while storing molds under optimal conditions prevents rust formation or material degradation over time.
How To Extend The Life Of Your P20 Steel Mold
- Regular Cleaning and Inspection:
- Ensure thorough cleaning after each use to remove dirt, debris, and residual plastic material.
- Regular inspections help identify any potential issues early on.
- Lubrication of Moving Parts:
- Apply appropriate lubricants regularly to reduce friction and prevent premature wear and tear.
- Temperature Control:
- Monitor and control temperature during the molding process to prevent thermal fatigue and structural damage.
- Comprehensive Maintenance Schedule:
- Maintain detailed records of cleaning, repairs, modifications, and inspections.
- Early identification of issues allows for timely intervention to prevent significant damage.
- Proper Storage Conditions:
- Store molds in a dry, controlled environment to prevent rusting or corrosion.
- Personnel Training:
- Educate personnel on careful handling techniques to avoid accidental damage.
- Optimization of Molding Parameters:
- Fine-tune injection speed, pressure, and cooling time to reduce stress on the mold and enhance product quality.
Signs Of Wear And When To Replace Your Mold
- Surface cracks or visible lines on the mold: These are often the first telltale signs of wear. They can transfer onto the molded plastic parts, affecting their aesthetic and structural integrity. If these cracks become deep or widespread, it compromises the mold’s ability to accurately shape parts, signaling a need for replacement.
- Increased cycle times: As molds wear out, they may not close as tightly or move as smoothly, leading to longer production times per part. Observing a gradual increase in cycle times can suggest that wear and tear on the mold are impacting its operational efficiency.
- Changes in part dimensions or increasing instances of defective products: These are clear indications that a mold has worn beyond its optimal condition. Over time, erosion within the mold cavity can alter its dimensions slightly but significantly enough to affect product uniformity and precision.
- Ejector pin issues: Sticking or misalignment of ejector pins point towards excessive wear. The ejector system is crucial for removing finished parts from the mold; thus, any inconsistency here could lead to damage both to the parts and eventually to the mold itself due to increased force requirements during ejection.
- Escalation in maintenance requirements: If a mold needs frequent repairs or more intensive cleaning than usual to operate correctly, this could indicate that it is nearing the end of its useful life.
In Conclusion
In summary, the longevity of P20 steel molds is largely influenced by factors such as maintenance practices, usage intensity, and the specific application it is designed for, generally providing service for up to hundreds of thousands of cycles under optimal conditions.
To ensure your operations benefit from the full potential of P20 steel molds, consider engaging with reputable professionals for your mold design and maintenance needs. Reach out today to explore how we can support the durability and efficiency of your manufacturing processes.