P20 steel is widely recognized for its remarkable moldability, robustness, and resilience, making it a preferred choice in various industries such as automotive and plastic molding. However, due to considerations such as cost, availability, or specific application requirements, alternatives to P20 steel are often sought after. This article explores viable substitutes that offer similar or enhanced properties for specific applications, providing insights into their characteristics, advantages, and potential drawbacks.
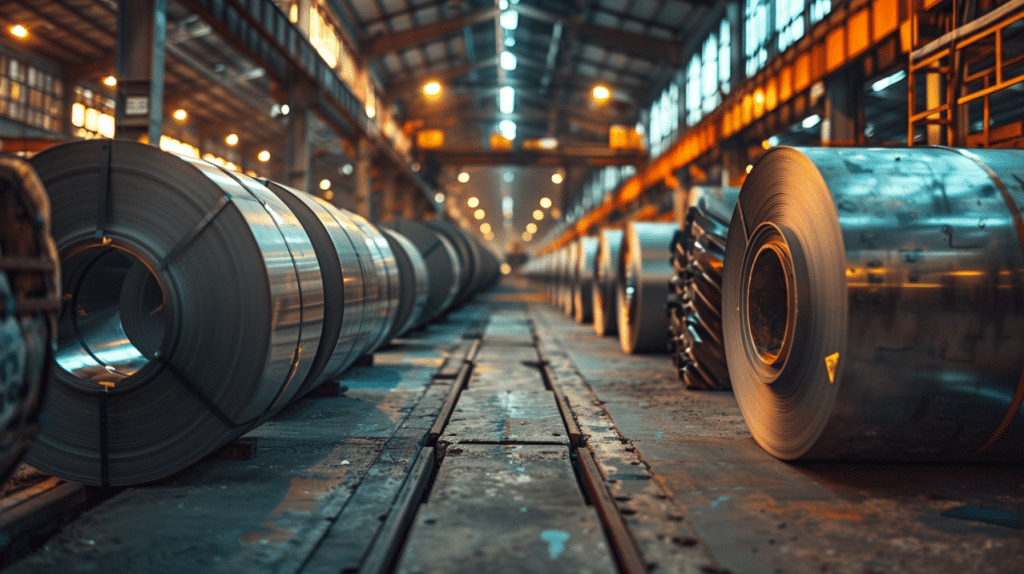
What Is S2 Steel?
S2 steel stands out in the realm of tool steels, characterized by its distinctive composition and properties which cater to specific application needs. This material is engineered for optimal performance under conditions that demand a high degree of reliability and durability.
The core of S2 steel’s composition lies in its alloying elements. Primarily, it is a high carbon and high chromium steel, enriched with significant amounts of vanadium and molybdenum. These elements are pivotal in refining the steel’s grain structure, enhancing its wear resistance, and boosting its overall strength. The precise balance between carbon and chromium ensures an exceptional hardness level while maintaining a good measure of toughness—a critical factor in resisting sudden impacts without fracturing.
From a mechanical standpoint, S2 steel exhibits remarkable characteristics that make it highly sought after in various industrial applications. Its hardness can be tempered to achieve varying degrees ranging from moderately hard to extremely hard, depending on the specific requirements of the application. This versatility extends to S2 steel’s toughness; it maintains integrity and resilience even under substantial stress or strain. Additionally, it showcases admirable wear resistance which prolongs its life span in abrasive environments.
The typical applications of S2 steel are as diverse as they are demanding. Predominantly used in the manufacturing of professional hand tools such as screwdrivers, wrenches, and drills, S2 steel’s properties ensure these tools perform reliably even under rigorous use. Beyond hand tools, this material finds relevance in industrial settings—contributing to the manufacturing processes that require precision and durability such as machining fabrication tools and injection molds.
Why Look For P20 Steel Alternatives?
The quest for alternatives to P20 steel arises from a blend of economic and performance-oriented factors. Cost-effectiveness is paramount in any manufacturing or engineering project. Seeking alternatives that offer comparable or superior qualities at a reduced cost impacts the bottom line positively, making it an attractive proposition for businesses.
Better mechanical properties for specific applications also drive the search for substitutes. Different projects may require materials with higher hardness, strength, or toughness levels than what P20 steel can offer. This pushes engineers and designers to look beyond P20 steel to find materials that better meet their specific application requirements.
Improved machining and welding characteristics are yet another reason to consider alternatives. Materials that are easier to machine or weld can significantly reduce production times and costs associated with labor and equipment wear. Certain alternatives may offer smoother machining experiences or more favorable welding qualities without compromising on material strength or durability.
Lastly, availability issues with P20 steel may necessitate looking into substitutes. Market fluctuations, supply chain disruptions, or regional availability can affect the accessibility of P20 steel. In such cases, finding readily available alternatives ensures that projects remain on schedule without significant delays.
Factors To Consider When Choosing An Alternative
Compatibility With Existing Applications
When searching for an alternative to P20 steel, it’s essential to ascertain the compatibility of the new material with existing applications. This ensures that the switch does not adversely affect product quality or require significant modifications to manufacturing processes, which could lead to increased costs and production delays.
Mechanical Properties
The mechanical properties of a material—including its strength, hardness, and toughness—are crucial parameters that determine its performance in specific applications. An ideal alternative should offer equal or superior mechanical properties compared to P20 steel to meet or exceed the requirements of the intended application.
Machinability and Weldability
Machinability and weldability are important aspects of a material’s workability. Materials that are easier to machine and weld can reduce production times and costs. Therefore, when considering alternatives to P20 steel, evaluating these characteristics ensures that the selected material can be efficiently integrated into current manufacturing processes.
Corrosion Resistance
Corrosion resistance is another vital factor for many applications. Depending on the environment in which the final product will be used, selecting a material with adequate corrosion resistance is necessary to prolong the lifespan of the component and maintain its functionality over time.
Cost and Availability
Finally, cost and availability are practical considerations that cannot be overlooked. The chosen alternative should be readily available in sufficient quantities and at a cost that is justifiable based on the benefits it offers over P20 steel. This includes taking into account both initial costs as well as potential savings in production due to improved workability or durability of the material.
In summary, when seeking an alternative to P20 steel, it is key to thoroughly evaluate potential materials based on their compatibility with current applications, mechanical properties (strength, hardness, toughness), machinability and weldability, corrosion resistance, as well as their cost and availability. These criteria help ensure a smooth transition while maintaining or enhancing product quality.

Popular Alternatives to P20 Steel
P20 steel, known for its versatility in the tool and die sector, occasionally faces challenges that necessitate the exploration of alternatives. The quest for materials with better performance or cost-efficiency drives the industry towards a range of other metals and alloys that can serve as suitable replacements under specific circumstances.
Tool Steels (e.g., D2, H13)
Tool steels are a popular alternative to P20 steel, offering a range of properties that cater to different industrial applications. Among them, D2 and H13 are widely recognized for their distinct characteristics and advantages in specific contexts.
D2 is known for its high wear resistance and ability to retain hardness after heat treatment. It contains between 1.4% to 1.6% carbon and 11% to 13% chromium, which contribute to its impressive durability and corrosion resistance. Its high chromium content makes it somewhat difficult to machine compared to P20 steel but offers superior performance in applications where abrasion resistance is crucial.
On the other hand, H13 tool steel stands out due to its exceptional hot hardness and thermal shock resistance, making it ideal for tools exposed to drastic temperature changes. With a typical composition that includes about 0.4% carbon, 5% chromium, 1.3% molybdenum, and 1% vanadium, H13 exhibits remarkable toughness and fatigue strength at elevated temperatures. This enables its use in hot-work applications such as die casting tools, extrusion dies, and forging dies.
When comparing these alternatives with P20 steel, users must weigh the benefits of enhanced performance characteristics against the potential challenges related to machinability and cost. P20 steel is often preferred for its ease of machining and lower cost relative to many tool steels; however, D2’s superior wear resistance or H13’s high-temperature stability may justify their selection for demanding environments.
Choosing between D2 or H13 over P20 depends greatly on the specific requirements of the application – whether greater importance is placed on wear resistance, toughness, or the ability to withstand high temperatures without losing hardness.
The transition from working with P20 steel to employing tool steels like D2 or H13 requires careful consideration of machining practices due to differences in material properties. Adjustments in cutting speeds, feeds, cooling systems, and tooling materials may be necessary to effectively process these harder steels while achieving desired finishes and dimensional accuracy.
Stainless Steels (E.g., 420)
When considering alternatives to P20 steel, stainless steels, such as grade 420, present an attractive option. This type of steel is well-regarded for its high chromium content, which contributes significantly to its excellent corrosion resistance properties. The specific composition of 420 stainless steel includes a notable amount of chromium—at least 12%—which is the primary factor behind its rust-resistant capabilities. This feature makes it particularly suited for applications where the material is exposed to corrosive environments.
Aside from corrosion resistance, 420 stainless steel also boasts commendable strength and hardness after heat treatment. It can achieve a hardness up to 50 HRC, making it capable of withstanding considerable wear and stress. Such characteristics render it suitable for components that require both durability and resistance to corrosive elements.
The typical applications of 420 stainless steel span various sectors. In the industrial context, it’s commonly utilized in tooling and mold-making operations thanks to its ability to maintain sharp edges and provide a smooth surface finish. It’s also prevalent in the medical sector for surgical instruments due to its high hygiene standards facilitated by its corrosion resistance.
However, despite these advantageous properties, there are considerations when comparing it directly with P20 steel. While both materials serve in tooling applications, the choice between them often hinges on the specific requirements of the task at hand concerning corrosion resistance, strength, machinability, and cost.
Machinability is another aspect where 420 might differ from P20; while generally considered good, the higher hardness levels after heat treating can make machining more challenging than P20 steel. Consequently, it requires careful planning when selecting tools and machining parameters.
In terms of availability and cost, stainless steels like 420 tend to be readily available in various forms due to their widespread use across industries. However, pricing may fluctuate based on market conditions for chromium and other alloying elements but usually remains competitive within specialty steel markets.
Aluminum Alloys (E.G., 7075)
The 7075 aluminum alloy is renowned for its exceptional strength-to-weight ratio. When evaluating materials for aerospace or automotive applications where reducing weight without compromising strength is paramount, 7075 stands out. Its composition includes zinc as the primary alloying element, contributing significantly to its strength.
In terms of machinability, 7075 aluminum alloys offer favorable characteristics. They can be machined efficiently with proper tooling and process parameters, although not as easily as some softer aluminum grades due to their high strength. Regarding welding, it is worth mentioning that 7075 tends to be more challenging to weld than other aluminum alloys, requiring specific methods such as friction stir welding for effective joining without weakening the material.
Another aspect where 7075 distinguishes itself from P20 steel is corrosion resistance. Aluminum inherently offers better resistance to oxidation than steel, making it suitable for applications in corrosive environments. However, it’s critical to note that while 7077 has good corrosion resistance overall, certain conditions can lead to susceptibility if not properly protected or treated.
Concerning cost and availability, aluminum alloys like 7075 are generally more readily available than specialized tool steels like P20. The pricing may vary based on market fluctuations and specific supplier dynamics but investing in 7075 could offer long-term benefits owing to its durability and performance characteristics.
High-Speed Steels (E.g., M2)
High-speed steels, particularly M2, present an attractive alternative to P20 steel for various applications requiring superior wear resistance and toughness. Known for their ability to retain hardness at high temperatures, M2 high-speed steels are an excellent choice for cutting tools, dies, and punches where the working conditions can lead to rapid wear of softer materials.
M2 steel stands out due to its composition, which includes molybdenum. The presence of molybdenum significantly enhances the material’s strength and heat resistance, making it capable of performing under strenuous conditions without losing its integrity. This characteristic is especially beneficial in industries where precision and durability are paramount.
In comparison to P20 steel, M2 offers improved hardness and heat resistance, which can be crucial for high-demand applications. However, this comes with a trade-off in machinability. Due to its hardness, machining M2 steel requires more time and specialized equipment than P20 steel. Welding of M2 is also more challenging due to its susceptibility to cracking if not handled with appropriate preheating and post-heating practices.
Despite these challenges in machining and welding, M2’s exceptional performance in wear resistance makes it a worthy contender for applications that push materials to their limits. It’s also worth noting that the cost-effectiveness of using M2 can vary depending on the specific requirements of the application; its higher initial costs may be offset by longer service life and reduced downtime.
Pros and Cons of Each Alternative in Comparison to P20 Steel
When considering alternatives to P20 steel, it’s vital to assess the advantages and disadvantages of each option. This analysis enables a more informed decision, ensuring that the chosen material meets the specific needs of your application. Below is a detailed comparison of popular alternatives including tool steels (D2, H13), stainless steels (420), aluminum alloys (7075), and high-speed steels (M2) against P20 steel.
Alternative | Pros | Cons |
---|---|---|
Tool Steels (D2, H13) | – D2 offers excellent wear resistance and retains its hardness up to 425°C. – H13 is renowned for its toughness and high-temperature strength. – Both have superior abrasion resistance compared to P20. | – D2 can be difficult to machine due to its high abrasion resistance. – H13, while tough, requires precise heat treatment for optimal properties. |
Stainless Steel (420) | – 420 provides outstanding corrosion resistance. – Ability to be polished to a high finish for excellent surface quality. | – Harder and more expensive to machine than P20. – Requires stringent heat treatment processes for desired mechanical properties. |
Aluminum Alloys (7075) | – Exceptionally lightweight yet strong, suitable for weight-critical applications. – Excellent machinability and thermal conductivity, reducing cycle times. | – Lower hardness and wear resistance compared to steel counterparts. – Potentially higher initial costs. |
High-Speed Steel (M2) | – Maintains high hardness at elevated temperatures. – Good toughness and wear resistance. | – More challenging to machine compared to P20. – Specific machining strategies or tools may increase production costs. |
How To Transition From P20 Steel To An Alternative
Making a shift from P20 steel to an alternative material involves careful consideration of several factors to ensure that the transition is smooth and beneficial for your specific applications. Follow these steps to facilitate a successful shift:
Assess Compatibility and Requirements: Begin by evaluating the compatibility of potential alternatives with your existing applications. This includes reviewing the mechanical properties such as strength, hardness, and toughness, along with machinability, weldability, and corrosion resistance of the alternative materials compared to P20 steel. Ensure that the alternatives meet or exceed the performance requirements of your projects.
Material Analysis: Conduct a detailed analysis of the material properties of potential alternatives. This involves comparing strength, hardness, impact resistance, and thermal conductivity among other properties. Understanding these attributes is vital in selecting an alternative that will perform adequately under operational conditions.
Cost-Benefit Analysis: Perform a cost-benefit analysis considering not only the material cost but also fabrication expenses related to machining and welding characteristics, as well as long-term durability and maintenance requirements. This step is critical in determining whether transitioning from P20 steel is economically viable for your operation.
Availability Check: Confirm the availability of alternative materials in your region or through your supply chain. Ensuring that the chosen alternative is readily available minimizes disruptions to production schedules and avoids potential delays in project timelines.
Prototype Testing: Before fully committing to an alternative material, create prototypes for testing purposes. These tests should simulate real-world application environments to accurately assess how well the alternative performs relative to P20 steel under similar conditions.
Consulting Specialists: It might be beneficial to consult with material scientists or engineers who specialize in metal alternatives. Their expertise can guide you towards making an informed decision on which substitute not only meets but potentially exceeds P20 steel’s capabilities for your specific needs.
Training Staff: Educate your team about any changes in working properties when using the new material – this may include adjustments in machining parameters or welding techniques. Training ensures that staff are well-prepared to handle the new material effectively, minimizing errors and optimizing performance.
Is P20 Similar To 4140?
P20 steel is primarily used in the mold industry for plastic injection molds and die casting. It is a versatile, low-alloy tool steel that contains elements such as chromium, molybdenum, and nickel. Its composition ensures good machinability and has been specifically tailored to promote uniform hardness across large sections. This characteristic makes it an excellent candidate for molds that require a balance between strength and ductility.
On the other hand, 4140 steel belongs to the category of medium-carbon alloys and is known for its outstanding toughness, high torsional strength, good fatigue strength, and great resistance to wear. The constituents of 4140 include chromium, molybdenum, and manganese which are responsible for its enhanced properties. Unlike P20 steel designed mainly for mold work requiring polishing or texturing surfaces, 4140 finds broader applications in gears, axles shafts, bolts but less in precise molding scenarios.
While both steels share common alloying elements like chromium and molybdenum – which contribute to their hardenability – the proportions differ significantly. These variations directly impact not only their mechanical properties but also their suitability for specific tasks. For instance, P20’s niche largely encompasses applications demanding surface integrity combined with medium hardness; whereas 4140’s robustness makes it ideal for components demanding high strength under stress conditions.
What Is The European Equivalent Of P20 Steel?
In Europe, P20 steel is closely matched by 1.2311 and 1.2312 steels according to the European standard. These grades offer similar characteristics in terms of chemical composition and mechanical properties, which makes them practical substitutes in regions where European standards are preferred.
Both 1.2311 and 1.2312 steels contain a mixture of chromium, molybdenum, and manganese, which contributes to their excellent hardenability and toughness—a key reason they’re considered suitable equivalents to P20 steel. While these materials maintain close adherence to P20’s performance spectrum, there are slight variations that can influence choice depending on specific application needs.
Another aspect worth noting is the added sulfur content in 1.2312 steel, which improves machinability but could slightly affect polishability as opposed to 1.2311 and traditional P20 steel. This characteristic of 1.2312 makes it slightly more specialized depending on the final requirements of the mold or tool being produced.
What Is The Difference Between H13 and P20 Steel?
When comparing H13 steel to P20 steel, it’s essential to understand that both materials serve distinct purposes in the manufacturing world due to their unique chemical compositions and resulting mechanical properties. While P20 steel is celebrated for its adaptability in plastic injection molds due to its exceptional hardness and uniform tempering ability, H13 steel stands out in environments demanding high toughness at elevated temperatures.
H13 steel, an air-hardening tool steel, contains elements such as chromium, molybdenum, vanadium, and silicon. These components grant it excellent resistance to thermal fatigue cracking, a common issue in hot work applications like forging or die casting. Its composition enables it to withstand drastic temperature variations without sacrificing toughness or strength.
On the other hand, P20 steel, a pre-hardened mold steel, includes specific amounts of chromium, molybdenum and nickel. This blend not only provides good polishability but also enhances its machinability. Typically used in plastic injection mold bases and cavities due to its impressive balance between hardness and ductility at room temperature, P20 offers manufacturers a reliable option that doesn’t require further heat treatment after machining – a notable advantage for cost-efficiency.
The variance in their preferred applications arises predominantly from their differing responses to thermal stress. H13 exhibits superior hot hardness which makes it suited for high-heat settings—a characteristic less pronounced in P20 steel. Conversely, the advantageous machinability and stable characteristics of P20 at lower temperatures make it ideal for plastic molds rather than applications encountering extreme heat.
What Grade of Steel Is P20?
P20 steel is categorized as a low-alloy tool steel, known widely for its excellent balance of durability, toughness, and workability. This classification under tool steels signifies that P20 is primarily designed for mold making and tooling applications. The distinctive characteristics of P20 steel stem from its specific chemical composition, which incorporates elements such as chromium, molybdenum, and nickel.
In Conclusion
In conclusion, the exploration of alternatives to P20 steel demonstrates the potential for cost savings and performance improvements across various industrial applications.
For those interested in enhancing their operations or seeking more information on sustainable and efficient material options, we encourage you to reach out and explore how these alternatives can benefit your projects. Let us assist you in navigating the selection of materials that best suit your needs and objectives.