In the realm of toolmaking and engineering, choosing the correct material for a specific application is foundational to achieving desired performance outcomes. Two prominent materials often under consideration are P20 steel and AISI 4140 steel. Both are widely used due to their distinct properties, catering to differing needs within tool making, manufacturing, and engineering designs. This article aims to delineate the primary differences between P20 steel and AISI 4140, focusing on their chemical composition, mechanical properties, applications, and overall performance characteristics. Understanding these distinctions is crucial for making an informed material selection that aligns with the specific requirements of a given project.
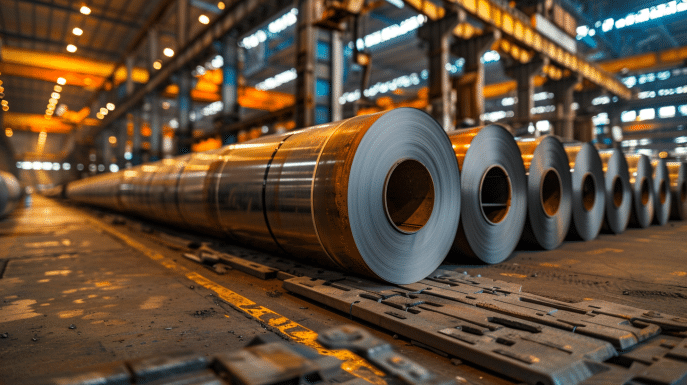
What Is 4140 Steel?
4140 steel is a versatile alloy that stands out in the family of chromium-molybdenum steels. Known for its excellent balance between strength and toughness, this steel grade is often referred to by its AISI designation – 4140. Its properties make it a favored choice in a wide range of industries, including automotive, aerospace, and manufacturing.
At its core, 4140 steel boasts a notable composition. The presence of chromium enhances its corrosion resistance while molybdenum contributes to the material’s strength and heat resistance. These elements work in harmony to grant 4140 steel an admirable set of mechanical properties suitable for demanding applications.
The versatility of 4140 steel extends further into its treatability. It exhibits an exceptional ability to be hardened by heat treatment which significantly increases its toughness and wear resistance. This characteristic is central to its widespread use in applications that require a durable material capable of withstanding high-stress conditions.
Moreover, 4140 steel showcases good machinability in both its annealed and hardened state. This trait makes it relatively easy to shape and manufacture into various components without sacrificing performance or durability. Its adaptability does not end there; 4140 can also undergo welding processes with appropriate precautions, offering engineers and designers even greater flexibility in their projects.
Composition Of 4140 Steel
- Iron: Primary base of 4140 steel, providing the fundamental metallic properties.
- Chromium (0.8 to 1.1% by weight): Enhances durability and corrosion resistance, acting as a protective barrier against environmental degradation.
- Molybdenum (0.15 to 0.25% by weight): Increases strength and heat resistance, maintaining structural integrity under high temperatures or stress.
- Manganese (0.75 to 1% by weight): Improves hardenability and tensile strength, and aids in removing sulfur compounds during production.
- Carbon (approximately 0.38-0.43% by weight): Affects hardness and strength, with higher levels increasing strength but reducing weldability and ductility.
- Silicon (around 0.15-0.30%): Serves as a deoxidizer in the steel making process, also may influence strength and hardness.
- Phosphorus (up to 0.035%): Generally considered an impurity; efforts are made to keep its content as low as possible to avoid brittleness.
- Sulfur (up to 0.040%): Like phosphorus, it’s kept to a minimum due to its potential to create brittleness and affect weldability negatively.
Properties Of 4140 Steel
- Balanced Composition: 4140 steel is a medium-carbon alloy steel known for its strength, toughness, and ductility, along with wear and abrasion resistance.
- High Tensile Strength: Depending on heat treatment, it can exceed 140 KSI, though averages around 95 KSI without treatment, allowing for performance customization.
- Remarkable Hardness: Achieves up to 197 Brinell (approx. Rockwell C20) in a normalized state, with potential for significant increase post-heat treatment.
- Toughness and Ductility: Maintains respectable levels even after hardness-increasing heat treatment, ensuring it doesn’t become excessively brittle.
- Impact Resistance: Robust across various temperatures, with improvements upon tempering at higher temperatures.
- Fatigue Strength: Exhibits a strong ability to resist failure under cyclic loading, crucial for components like rotating shafts and gears.
- Adaptability Through Heat Treatment: Offers a range of hardness options, enhancing its suitability for diverse applications and environments.
What Is P20 Steel?
P20 steel emerges as a notable player in the tool steel category, primarily appreciated for its remarkable mold quality. This type of steel is widely recognized for its superb machinability and polishability features, which serve the demands of various industries. The key aspect that sets P20 steel apart is its adaptability to modifications during the production phase, enabling manufacturers to achieve precision in shaping and detailing without compromising the integrity of the material.
Crafted through a meticulous process that includes melting in an electric arc furnace followed by cooling to forge a robust structure, P20 steel offers a balanced composition that contributes to its distinctive characteristics. These processes ensure that P20 retains exceptional purity and consistency across batches, making it a preferred choice for tasks requiring a high degree of accuracy and finish.
The versatility of P20 steel extends beyond its physical attributes. It is also known for its thermal stability, which is crucial during the manufacturing process as it reduces risks associated with thermal fatigue. This attribute makes P20 an ideal choice for crafting intricate molds that necessitate precise temperature control to prevent defects.
Moreover, P20 steel’s resilience against abrasive wear adds another layer of reliability for manufacturers. In environments where materials are subjected to continuous friction and other wear-inducing conditions, P20 stands up well, maintaining its integrity longer than many other types of steel would under similar circumstances.
P20 steel positions itself as a formidable choice within the tooling industry due to its superior machinability, excellent polishability, consistent quality across batches, thermal stability, and resistance to wear. Its ability to be easily modified while retaining strength makes it conducive for detailed work where precision is paramount.
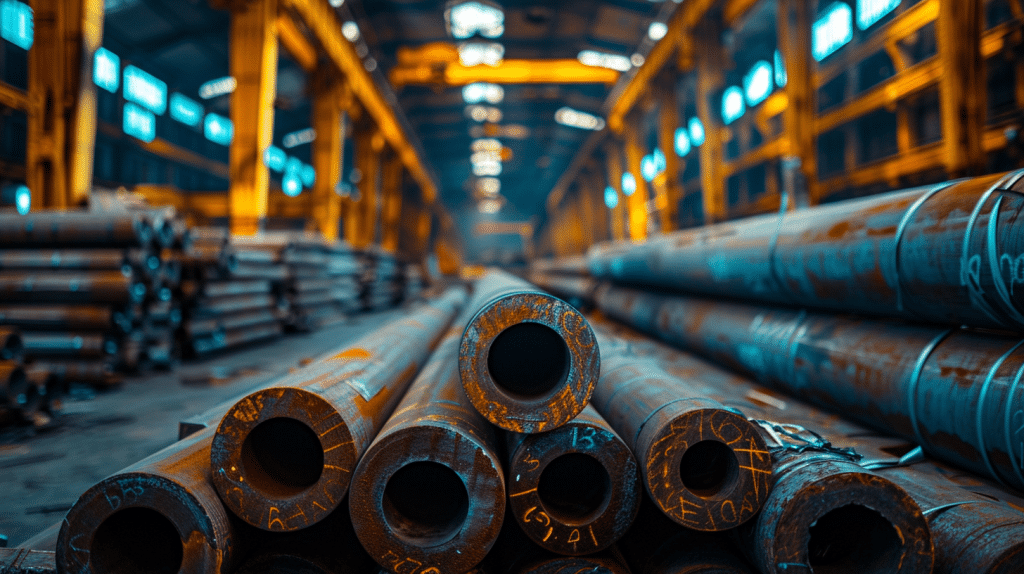
Composition Of P20 Steel
- Iron (Fe): Predominant base metal in the alloy.
- Carbon (C): Typically 0.28–0.40% by weight, enhancing hardness and strength.
- Chromium (Cr): Usually 1.4–2.0%, providing corrosion resistance, hardenability, and wear resistance.
- Molybdenum (Mo): Generally 0.30–0.55%, improving strength under high temperatures and stability during heat treatment.
- Nickel (Ni): Typically 0.85–1.15%, enhancing toughness and strength without sacrificing machinability.
- Manganese (Mn): About 0.60–1.00%, improving hardenability, strength, and steel cleanliness by removing oxygen during manufacturing.
- Silicon (Si): Approximately 0.30–0.50%, reducing melting temperatures and aiding in casting processes while increasing overall strength.
Properties of P20 Steel
- Hardness: Typically supplied at a hardness range of 280 to 320 Brinell (BHN), facilitating easier machining while still being capable enough to withstand wear and tear.
- Toughness: Enhanced by its unique chemical composition, which includes a moderate amount of chromium and nickel, enabling it to endure cyclic stress loads without succumbing to fatigue or failure.
- Machinability: Exhibits superior machinability due to its pre-hardened state and balanced alloy composition, allowing for smooth operations during milling, grinding, and polishing processes.
- Dimensional stability under heat treatment: Resilience against distortions when subjected to temperature variations during the production cycle, accentuated by proper management during thermal cycles.
- Weldability: Offers straightforward welding characteristics compared to high-carbon equivalents, with simple precautions such as preheating and suitable welding techniques mitigating potential issues like cracking or porosity in welded joints.
What Is The Difference Between P20 Steel And 4140?
When comparing P20 steel to 4140, it is essential to consider their differences in chemical composition, mechanical properties, standards, cost, applications, heat treatment processes, and weldability. These factors significantly influence the choice between the two for specific projects or applications.
Chemical Composition
P20 steel and 4140 differ primarily in their chemical compositions. P20 is classified as a mold steel and contains elements such as chromium, molybdenum, and nickel that enhance its ability to be polished and machined. Specifically designed for plastic injection mold applications, its composition is tailored for excellent machinability and polishability. On the other hand, 4140 steel is an alloy steel that includes chromium, molybdenum, and manganese. This combination results in high tensile strength and toughness over a wide temperature range.
Mechanical Properties
Mechanically, 4140 exhibits higher tensile strength and hardness due to its increased carbon content compared to P20. This makes 4140 suitable for applications requiring high fatigue strength, impact resistance, and general toughness. Conversely, P20 offers superb machinability and dimensional stability which makes it ideal for crafting intricate molds where surface finish is critical.
Standard
In terms of standards, these steels adhere to distinct classifications across various industries and regions; P20 follows specific guidelines tailored for tool steels with considerations towards its application in mold making whereas 4140 adheres to standards applicable for general purposes alloy steels aimed at mechanical components subjected to high stress.
Cost Comparison
Comparatively speaking, P20 tends to be more expensive than 4140 due to its niche applications in tooling where specific properties like machinability and mirror-finish capability are prioritized. The cost factor can significantly influence material selection depending on budget constraints and project requirements.
Applications
The applications of each steel type diverge based on their unique characteristics. P20 is predominantly used in the plastic injection molding industry for creating precise molds with excellent finishes. Conversely, 4140’s superior strength attributes make it favored in the automotive sector for gears, axles as well as oil & gas industry components under high-stress conditions.
Heat Treatment And Weldability
Both types undergo different heat treatment processes reflecting their distinctive uses; P20 is usually tempered at lower temperatures to avoid altering its excellent machinability while still achieving desirable hardness. In contrast, 4140 benefits from a variety of heat treatments including annealing or quenching followed by tempering at different temperatures conducive to achieving targeted toughness levels. Weldability of each also varies; P20 being generally considered more challenging due to its carbon content leading potentially to cracks if not performed under precise conditions whereas 4140 boasts better weldability traits owing mainly to its adaptable nature under varied thermal conditions.
Choosing Between P20 and 4140 Steel
When faced with the decision of selecting between P20 and 4140 steel for a project, various factors come into play that influence which material is the best fit. Your choice between these two highly regarded materials hinges on understanding their unique traits and how they align with the demands of your specific application. This involves a thorough evaluation of both steels’ chemical compositions, mechanical properties, costs, applications, suitability for heat treatment, and weldability.
P20 steel, known for its excellent mold quality in plastic injection molding, stands out due to its exceptional balance of hardness and toughness. This makes it an ideal choice for tools and dies where a polished surface finish is crucial. On the other hand, 4140 steel is celebrated for its outstanding strength and versatility, which is attributable to its high chromium content. It thrives in applications that demand high fatigue strength and resistance to abrasion.
Cost considerations are pivotal in any material selection process. Generally speaking, P20 steel tends to be more expensive than 4140 due to its specialized composition designed for mold-making applications. However, investing in P20 could lead to longer tool life and better performance in specific scenarios, possibly offsetting the initial cost difference over time.
When it comes to applications, each material has its stronghold areas. P20 steel dominates in plastic injection molds and die casting due to its excellent machinability and surface finish after machining. Conversely, 4140 finds widespread use across various sectors – including automotive, oil and gas exploration equipment – thanks also to its adaptability under heat treatment which enhances strength or ductility depending on the need.
Heat treatment processes reveal further differences; P20 steel usually requires preheating before welding to minimize stress cracks. 4140 steel offers more flexibility with various heat treatment options that can extensively modify its mechanical properties.
In terms of weldability – a critical aspect in many engineering projects – 4140 provides better options owing to its versatile alloying elements that ensure stronger welds under properly managed conditions. However, both steels require specific attention during welding practices to maintain integrity.
Ultimately, the decision between P20 and 4140 steel comes down to balancing factors such as cost effectiveness against performance requirements tailored to your project’s specifics. Careful consideration of how each material’s characteristics align with your application’s demands will guide you toward making an informed choice that ensures success.
Which Is More Expensive, 4140 Steel Or P20 Steel?
P20 steel typically comes with a higher price tag compared to 4140 steel. This is largely due to the specialized composition and properties of P20 steel, making it preferable for specific applications, particularly in mold making. The cost difference reflects the material’s suitability for these niche requirements, where P20 offers advantages that justify its premium.
What Is The Main Advantage Of P20 Steel In Mold Applications?
P20 steel stands out in mold applications primarily due to its excellent machinability. This characteristic enables easier and more precise shaping into complex mold designs, thus optimizing the manufacturing process. Additionally, P20 steel offers a good balance of toughness and hardness, making it durable for use in producing high-quality molds. These properties significantly reduce the risk of cracking under stress, ensuring the longevity of the molds created with this material.
Can 4140 Steel Be Used For Mold Applications?
YES. 4140 steel can be used in mold applications. It is acknowledged for its toughness and high fatigue strength, making it suitable for molds that require durability and resistance to wear. Its adaptability in heat treatment also allows for tailored hardness levels, further enhancing its suitability for complex mold designs.
What Grade Of Steel Is P20?
P20 steel is classified as a mold steel, specifically designed for molding applications. It stands out due to its excellent machinability, relatively low cost, and ability to be polished to a high shine. These characteristics make P20 steel a popular choice in various tool and die applications.
What Is 4140 Steel Equivalent To?
4140 steel, known for its strength and versatility in the metallurgy sector, has equivalents in various standards and specifications globally. It corresponds to 1.7225 according to the European EN standard, and to 42CrMo4 in the ISO system. In the American AISI/SAE classification, it retains its 4140 designation, showcasing its widespread recognition and consistency across different geographic standards. Its uniform chemical composition and mechanical properties make it interchangeable within these equivalents, ensuring a broad understanding and application of its capabilities in industries worldwide.
What Is P20 Steel Equivalent To?
P20 steel is equivalent to several other tool steel grades that exhibit similar properties, primarily in terms of mold quality and durability. Its closest equivalents include AISI P20 steel, DIN 1.2311, and 3Cr2Mo. Each of these alternatives shares a comparable chemical composition and mechanical properties, making them suitable substitutes for applications requiring P20 steel. This equivalence allows for flexibility in material selection based on availability or specific project requirements.
Is 4140 Steel More Durable Than P20 Steel?
YES. 4140 steel generally offers higher durability compared to P20 steel.
This is primarily due to its composition and heat treatment process. 4140 steel, with its higher carbon content and incorporation of chromium and molybdenum, provides enhanced hardness and tensile strength.
These properties make it more resistant to wear and tear, which is crucial in applications requiring high durability.
In contrast, P20 steel, while beneficial for its moldability and uniform hardness, does not match the durability levels of 4140 steel for heavy-duty applications.
What Steel Is Stronger Than 4140?
There are several types of steel that are stronger than 4140 steel. This includes but is not limited to, steels such as A2, D2, and S7 tool steels. These materials have higher wear resistance and can retain their strength at elevated temperatures better than 4140 steel.
A2 steel, for instance, offers excellent toughness and good wear resistance, making it a strong candidate for use in environments where 4140 might falter. D2, known for its high carbon and chromium content, provides greater hardness and corrosion resistance, making it immensely stronger in terms of wear resistance. S7 steel stands out for its impressive impact resistance at both low and high temperatures, surpassing 4140 in toughness. Each of these alternatives possesses unique properties that cater to specific needs surpassing the capabilities of 4140 in various applications.
Can I Use P20 Steel For Applications Typically Reserved For 4140 Steel?
YES, P20 steel can be used for applications typically reserved for 4140 steel, but with considerations. P20 is a tool steel known for its toughness and low carbon content, which makes it excellent for use in mold applications. However, 4140 steel is an alloy steel that generally offers better tensile strength and wear resistance, which makes it suitable for a variety of mechanical applications.
While P20 can be a substitute in some scenarios, it is important to evaluate the specific requirements of the application. Mechanical properties, heat treatment capabilities, and cost should all be taken into account before making a decision.
In Conclusion
In summary, while both P20 and 4140 steel have their unique properties and applications, the decision between them hinges on the specific requirements of your project including hardness, toughness, and weldability.
Explore our extensive range of high-quality metals to find the perfect material for your needs. Contact us today to discuss your project with our experts and make an informed choice between P20 steel and 4140.