P20 and A36 steel are two commonly used materials in the manufacturing and construction industries, each possessing distinct properties and applications. Understanding the differences between these two types of steel is crucial for selecting the appropriate material for specific projects or components. This article aims to delineate the primary distinctions between P20 and A36 steel, covering aspects such as chemical composition, mechanical properties, heat treatment procedures, and typical uses.
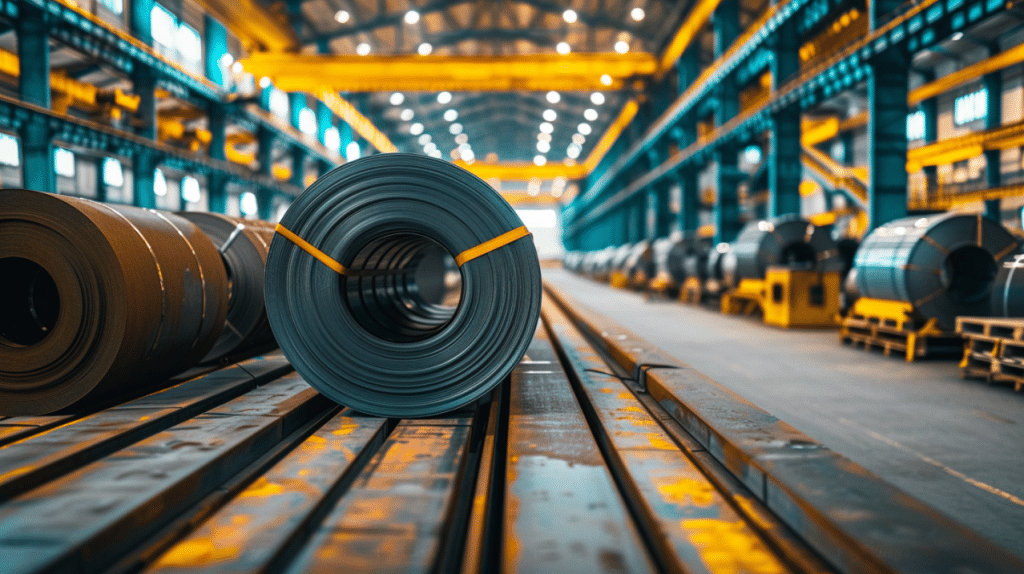
What Is P20 Steel?
P20 steel is a versatile mold steel known for its remarkable balance of strength, ductility, and thermal conductivity. This pre-hardened material exists as a standard in the world of toolmaking and mold manufacturing, offering users a reliable base for producing a wide range of tools and parts. The chemistry of P20 steel is designed to provide an optimal blend of hardness and toughness, ensuring it can withstand the rigors of injection molding and die casting processes.
At its core, P20 steel exhibits properties that make it highly favorable for applications requiring a fine surface finish alongside superior dimensional stability. Its ability to be machined into complex shapes with minimal wear on cutting tools makes it a preferred choice among engineers and manufacturers. Furthermore, P20 steel’s capacity to undergo various heat treatment processes allows for further enhancement of its mechanical properties, thereby extending the longevity of the molds or parts crafted from it.
In industrial applications, this type of steel finds prominence due to its adaptability in the face of intricate design requirements and demanding production schedules. The inherent qualities of P20 steel not only facilitate efficient manufacturing cycles but also contribute significantly to reducing overall project costs. By minimizing the need for excessive post-production treatments typically associated with harder steels, P20 stands out as an economical yet high-performing material option within the metallurgy field.
Moreover, P20 steel’s popularity extends beyond just its performance characteristics; it is also appreciated for its relatively easy handling during the machining process. Manufacturers value this trait as it translates into less time spent on adjustments and more focus on achieving precision in end products. Whether used in creating prototypes or full-scale production molds, P20 steel proves itself as an indispensable material that ingeniously combines workability with outstanding finished product quality.
Composition Of P20 Steel
The composition of P20 steel is a crucial aspect that defines its properties and suitability for various applications. P20 steel is categorized under the class of tool steels, which are alloy steels commonly used in toolmaking. This type of steel stands out due to its distinctive alloy composition, primarily designed for high hardness and ductility.
P20 steel predominantly contains carbon, which plays a vital role in determining the hardness and strength of the steel. The carbon content in P20 is carefully balanced to ensure it provides the desired mechanical properties without becoming too brittle. Alongside carbon, chromium is added to enhance corrosion resistance and improve the steel’s hardenability. This addition of chromium is significant because it allows the steel to maintain its strength even under harsh working conditions.
Manganese and silicon are also present in P20 steel’s composition. Manganese improves the hot working properties and increases hardenability, making the steel more resistant to cracking during water quenching processes. Silicon contributes to strengthening the material and also helps in reducing oxidation at high temperatures.
Moreover, molybdenum is another important element found in P20 steel. It significantly increases tensile strength at high temperatures, thereby improving toughness and wear resistance. Molybdenum’s presence enhances the material’s performance when subjected to thermal stresses, making it an ideal choice for mold-making applications where thermal stability is required.
Nickel is occasionally added to this alloy mix to further augment its toughness and resistance to thermal fatigue. This makes P20 particularly valuable in applications where molds or dies undergo repeated heating and cooling cycles.
The specific blend of these elements gives P20 steel its desired properties such as hardness after heat treatment, good machinability before heat treatment, and excellent polishability. This unique combination makes it highly favored for use in various industries including plastic injection molding and die casting.
Applications Of P20 Steel
P20 steel finds extensive use in various sectors, primarily due to its excellent moldability and relatively low cost, which make it an ideal material for tooling and mold making. Its applications range widely from manufacturing molds for plastics to die casting tools for aluminum, zinc, and magnesium alloys. The steel’s versatility also extends to the production of numerous industrial parts and components.
In the realm of injection molding, P20 steel stands out as a preferred choice. The material’s ability to be machined into complex shapes and sizes with precision makes it invaluable for creating intricate plastic parts and components. These characteristics ensure minimal wear on the molds, thereby extending their lifespan and reducing downtime for repairs or replacements.
Additionally, P20 is often employed in the manufacturing of die holders, backers, bolster plates, and other structural parts of injection mold and die sets. Its resilience under cyclic stresses and strains encountered during the molding process highlights its suitability for applications that demand a balance between toughness and hardness.
The adaptability of P20 steel is further showcased in its application across several industries beyond tool making. For instance, it is used in constructing carrier frames and guide rails within the automation industry due to its excellent machinability and durability. Industries that demand precise dimensions and reliable performance find P20 steel to be an asset that significantly enhances operational efficiency.
Advantages Of Using P20 Steel
- Impressive hardness: Ensures durability and long-lasting performance in tools and molds subjected to continuous wear.
- Enhanced machinability: Allows for easy shaping and molding without compromising quality or structural integrity.
- Remarkable resilience against thermal fatigue: Essential for applications involving repeated heating and cooling cycles, ensuring retention of shape and strength over time.
- Uniform hardness after quenching and tempering processes: Crucial for maintaining consistent performance throughout the tool or mold’s service life, minimizing the risk of failure or breakage.
- Pre-hardened state: Eliminates the need for further heat treatments, streamlining the production process and reducing associated costs.
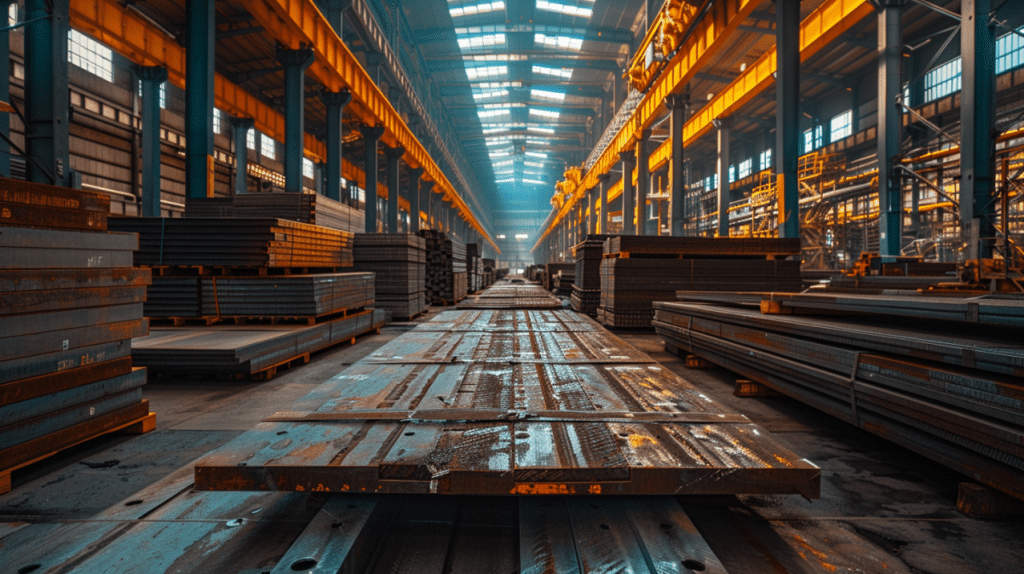
What Is A36 Steel?
A36 steel, widely recognized in the industry and engineering works as a standard structural steel, plays a critical role across various construction and fabrication sectors. This material stands out for its versatility and accessibility, making it a staple in building frameworks, bridges, and an assortment of general structural projects. Its prominence is rooted in its well-balanced blend of strength, formability, and affordable cost.
At the heart of A36 steel’s extensive application lies its simple yet effective composition. Primarily carbon steel, A36 incorporates minimal amounts of alloying elements. This modest alloy composition ensures that while the material retains adequate strength and hardness for numerous structural uses, it also maintains excellent formability. Consequently, this makes A36 steel an ideal candidate for welding practices and manipulations necessitated across varied construction endeavors.
The characteristics of A36 steel do not solely rest upon its physical attributes but also extend into its uniformity and predictability in performance under various conditions. These features significantly contribute to its preference among professionals in construction who seek reliability and compliance with standards such as those set by ASTM International. The adaptability and efficiency of A36 steel further cement its status as one of the fundamental materials contributing to the robust infrastructure seen worldwide today.
Composition Of A36 Steel
A36 steel, known for its structural applications, exhibits a distinct composition that underpins its widespread utility in various industrial and construction sectors. This carbon steel grade is characterized by its composition of primarily iron, accompanied by a small percentage of carbon (between 0.25% to 0.29% by weight), making it amenable to a variety of fabrication processes due to its excellent weldability and machinability.
In addition to iron and carbon, A36 steel also includes small quantities of other elements that enhance its mechanical properties and usability. Manganese content ranges from 0.75% to 1.20%, aiding in the steel’s strength and hardness; sulfur and phosphorus are present in trace amounts (usually less than 0.05%), which aid in improving machinability but must be limited to maintain strength.
Moreover, A36 may contain other elements such as silicon (up to 0.40%) and copper (up to 0.20%), providing additional benefits like improved formability and corrosion resistance, respectively. The presence of these elements collectively contributes not only to the robustness and ductility of A36 steel but also enhances its resistance against wear and tear in various environmental conditions.
Understanding the unique blend of elements in A36 steel reveals why this material is favored for manufacturing, infrastructure projects, architectural framing, and countless other applications where strength, flexibility, and durability are paramount. This detailed insight into A36’s chemical makeup demonstrates how its balanced composition facilitates a broad spectrum of uses while ensuring reliable performance across diverse applications.
Applications Of A36 Steel
A36 steel, recognized for its strength and versatility, finds its utility in a myriad of projects across various industries. This carbon structural steel is often chosen for its weldability and formability, making it a staple in construction and engineering projects.
In the construction industry, A36 steel is predominantly used in building frameworks, including beams, columns, and platforms. Its capability to support structures under heavy loads while maintaining integrity makes it an optimal choice for skyscraper frames, bridges, and parking garages. The material’s robustness ensures safety and longevity of the structures it supports.
Beyond large-scale infrastructure, A36 steel also plays a significant role in manufacturing. From automobile components to machinery parts, this material’s adaptability to different forms and sizes without compromising on strength is highly valued. Manufacturers appreciate A36 steel for its ability to be easily joined with other materials, which is crucial for complex assemblies.
Furthermore, the agricultural sector benefits from A36 steel through the fabrication of farm equipment such as tractors and plows. The harsh conditions encountered in farming necessitate durable materials capable of withstanding wear and tear; A36 steel meets these requirements adeptly.
Metalworking projects also see an extensive use of A36 steel due to its straightforward machinability. Whether it’s creating metal artworks or custom tools, hobbyists and professionals alike find this material accommodating to their needs.
Advantages of Using A36 Steel
- Excellent Weldability: The low carbon content simplifies welding processes, reducing the need for special techniques or preheating.
- Good Machinability: Despite being mild, A36 steel maintains good machinability, facilitating easier cutting, shaping, and finishing operations.
- Strong Mechanical Properties: Exhibits good strength and hardness levels, providing a reliable foundation for various structural applications.
- Cost Effectiveness: Widely available with competitive pricing, offering economical procurement and maintenance costs due to its durability.
- Adaptability: Suitable for a range of conditions and applications, from construction frameworks to machinery parts, allowing for customization according to project needs.
Key Differences Between P20 and A36 Steel
Chemical Composition and Material Properties
P20 steel is a mold steel primarily used in the plastic industry due to its excellent hardness and abrasion resistance. It contains elements like chromium, molybdenum, and nickel, enhancing its wear resistance. A36 steel, however, is a carbon structural steel comprising iron and small amounts of sulfur, phosphorus, silicon, and copper, known for its good weldability.
Mechanical Properties
P20 steel offers high toughness at moderate strengths, ideal for holding polished finishes in molded plastics. A36 steel boasts an excellent balance between strength and ductility, making it suitable for construction applications requiring bending and forming capabilities.
Weldability and Machinability
P20 steel requires pre-heating to prevent cracking during welding due to its alloy content but machines well due to its uniform hardness. A36 steel exhibits exceptional weldability with standard methods, simplifying construction tasks without requiring pre-heating.
Cost Considerations
P20 steel, tailored for specialized tooling applications, typically comes at a higher price compared to A36 steel, which benefits from wider availability and thus more competitive pricing.
Market Availability
P20 steel’s niche application areas may limit its availability compared to the widely used A36 steel, which is readily available from most suppliers globally.
Factors To Consider When Choosing Between P20 And A36 Steel
Choosing between P20 and A36 steel for a project involves considering several critical factors to ensure you select the most appropriate material for your specific needs. Each type of steel has its unique characteristics, making them suitable for different applications.
Intended Application
The first factor to consider is the intended application of the steel.
- P20 steel is widely used in plastic injection molds due to its excellent hardenability, toughness, and wear resistance.
- A36 steel is known for its good weldability, formability, and strength, making it a common choice for structural applications such as building frames or bridges.
Mechanical Properties
Another important consideration is mechanical properties, including strength, hardness, ductility, and impact resistance.
- P20 offers superior hardness and toughness compared to A36, which could be crucial depending on the nature of the application.
Weldability and Machinability
Weldability and machinability are also key factors to assess.
- A36 steel stands out for its excellent weldability with no preheating necessary; it also presents good machinability.
- P20 steel might require more specialized techniques for welding and machining due to its alloying elements enhancing its hardness and wear resistance.
Cost Considerations
Cost considerations cannot be overlooked either when choosing between these two materials.
- A36 steel is generally less expensive than P20 due to differences in alloy content and manufacturing processes required to produce each type of steel.
Availability
Lastly, availability on the market might influence your decision.
- While both types of steels are generally available worldwide, regional variations can affect delivery times and costs significantly.
For time-sensitive projects or where cost reduction is paramount, opting for readily available materials can prevent delays and additional expenses.
What Is The Steel Grade A36 Equivalent To?
In the European standard, A36 material closely matches the properties of S275JR steel according to the EN 10025-2 specification. This makes S275JR a direct equivalent in terms of chemical composition and mechanical properties.
Additionally, the global standards offer equivalents such as the Chinese Q235 which shares similar characteristics to A36 in aspects like tensile strength and yield. Japan has its own equivalent in the form of SS400 according to JIS G 3101. Each of these international equivalents maintains compatibility with A36, ensuring its applicability in a range of contexts worldwide, from bridge construction to manufacturing of durable goods.
Is A36 Steel the Same as 1018?
A36 steel and 1018 steel are two of the most common types of carbon steel used in various applications, yet they harbor distinct differences in their composition and properties. A36 steel is primarily known for its good weldability, strength, and ability to be heat treated for hardening purposes. It primarily finds its application in structural and construction projects due to its higher carbon content and strength.
On the other hand, 1018 steel, with its lower carbon content, showcases better machinability and can be welded more easily than A36, making it favorable for projects that require intricate shapes and detailed work. While both materials can be used interchangeably in some situations due to their similar properties, they are not the same. The choice between A36 and 1018 would, therefore, hinge on the specific requirements of the project, including strength, weldability, and the level of detail needed in the machining process.
What Is P20 Steel Equivalent To?
This type of tool steel aligns with the AISI P20 (American Iron and Steel Institute), DIN 1.2311 (German Institute for Standardization), and 40CrMnMo7 (European designation).
In Conclusion
In conclusion, while P20 and A36 steel possess distinct characteristics tailored to their specific applications in tool making and construction respectively, choosing the right one depends on the requirements of your project.
Should you seek expert advice or wish to explore a wide range of steel options for your next venture, do not hesitate to reach out to our specialists who are ready to assist you. Start your journey towards selecting the ideal material by contacting us today.