S50C steel and P20 are two commonly used materials in the field of mold making and mechanical parts manufacturing. Both materials possess unique properties that cater to specific applications, making the choice between them crucial for achieving optimal performance and durability in finished products. This article aims to delineate the differences between S50C steel and P20, focusing on their chemical composition, mechanical properties, applications, and overall performance in various industrial contexts. By understanding these distinctions, manufacturers can make informed decisions regarding material selection for their specific needs.
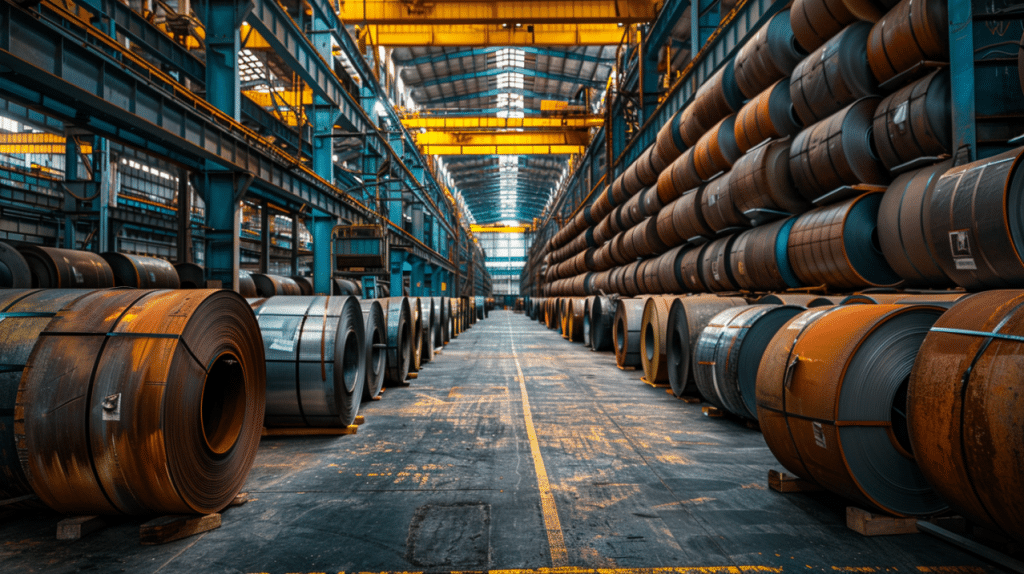
What Is S50c Steel?
S50c steel is a high-quality, medium carbon steel known for its strength and hardness. Primarily, this type of steel is recognized for its remarkable balance between durability and malleability, making it highly suitable for various industrial applications. With a carbon content close to 0.50%, the composition of S50c steel enhances its ability to be tempered and quenched, contributing significantly to its mechanical properties.
The designation ‘S50c’ refers to its classification in the Japanese JIS standard, indicating that it is primarily part of the carbon steel family. This grade of steel is meticulously produced to meet stringent quality standards, ensuring consistency in its properties across batches. The presence of medium carbon content plays a pivotal role in defining the characteristic strength and toughness of S50c steel.
Due to its well-balanced properties, S50c steel finds extensive use in the manufacturing sector. It’s particularly favored for applications requiring a combination of strength and impact resistance without compromising on machinability. Typical uses include mold making, base plates, and industrial machinery components where durability under stress is crucial.
Aside from its primary constituents—iron and carbon—S50c may also contain trace amounts of other elements such as manganese, phosphorus, and sulfur. These additional elements are kept at minimal levels to ensure that they do not adversely affect the steel’s quality but instead contribute positively to its overall mechanical characteristics and workability.
One of the standout features of S50c steel is its adaptability in heat treatment processes. By carefully adjusting these processes, manufacturers can enhance or tailor specific attributes like hardness or tensile strength according to precise requirements. This level of customizability makes S50c an invaluable material in fields requiring bespoke solutions without sacrificing performance or durability.
Composition Of S50c Steel
S50c steel belongs to the category of medium carbon steels, with a carbon content close to 0.50%. This significant amount of carbon plays a pivotal role in enhancing the hardness and strength of the steel, making it suitable for products where resistance and durability are necessary. Besides carbon, S50c steel also contains traces of silicon and manganese.
Manganese is present in S50c steel at approximately 0.60-0.90%. It serves to improve the steel’s strength while also enhancing its forgeability and toughness. This balance ensures that the material doesn’t just offer high durability but is also workable under various manufacturing processes.
Silicon levels in S50c steel are around 0.15-0.35%. Silicon acts as a deoxidizer in the steel-making process, which means it helps to purify the metal by removing oxygen bubbles during solidification. Consequently, this increases the metal’s strength and reduces the risk of imperfections within the material’s structure.
Moreover, small quantities of phosphorus and sulfur might be present as well; however, these elements are controlled within tight limits due to their tendency to affect negatively on certain material properties like ductility and toughness. Typically, phosphorus content is kept below 0.035% and sulfur content below 0.035%, ensuring that their impact on S50c’s performance is minimalized.
Applications Of S50c Steel
One common application of S50c steel is in the manufacturing of heavy-duty machinery parts. The material’s high strength and ability to withstand stress make it a preferred choice for components that are subject to intense forces or wear. This includes gears, axles, and hydraulic clamps where reliability under pressure is paramount.
Additionally, S50c steel is extensively utilized in the automotive industry. Parts such as crankshafts, connecting rods, and brake discs benefit from this steel’s resilience to fatigue and temperature variations. Its capacity to undergo rigorous heat treatments also allows for enhanced performance characteristics tailored to demanding automotive applications.
In the realm of mold making, especially for plastic injection molds, S50c steel serves as an excellent base material. Its uniform hardness ensures a consistent surface finish that can endure prolonged molding cycles without significant degradation. The ability for precise machining also aids in creating complex mold designs with tight tolerances.
Beyond these specific applications, S50c steel’s adaptability makes it suitable for a broad range of general engineering tasks. From structural components to intricate tools and dies, its balanced set of properties facilitates both creativity and functionality in design execution.
Pros Of S50c Steel
- Excellent wear resistance: Due to its high carbon content, S50c steel exhibits exceptional wear resistance, reducing wear and tear in demanding conditions.
- Shape retention under stress: S50c steel maintains its shape even under heavy loads or repeated forces, ensuring reliability and longevity in components.
- Good weldability: Despite its high carbon content, S50c steel can be welded satisfactorily with proper preparation and technique, offering flexibility in design and assembly processes.
- Good machinability: With the right tools and settings, S50c steel can be machined efficiently, allowing for high precision and quality in manufacturing processes.
- Cost-effectiveness: S50c steel is affordable compared to some alternative materials with similar properties, making it a preferred choice for projects with budget constraints.
Cons Of S50c Steel
- Lower weldability: Due to its higher carbon content, S50c steel can be challenging to weld effectively, leading to increased susceptibility to cracking during the welding process if not handled with appropriate preheating and post-heating techniques.
- Susceptibility to temper brittleness: S50c steel may experience temper brittleness after tempering at certain temperatures, reducing its toughness and making it more prone to fracturing under impact or stress conditions.
- Limitations in durability and flexibility: While offering good strength and hardness characteristics, S50c steel might not always provide the optimal balance of durability and flexibility needed for some applications, necessitating critical assessment of application-specific demands.
- Complexity in heat treatment processes: Heat treatment processes for adjusting the mechanical properties of S50c steel can be intricate due to its carbon content and susceptibility to thermal shock, requiring precise control over temperature parameters and cooling rates, which emphasizes the need for expertise in handling such materials.
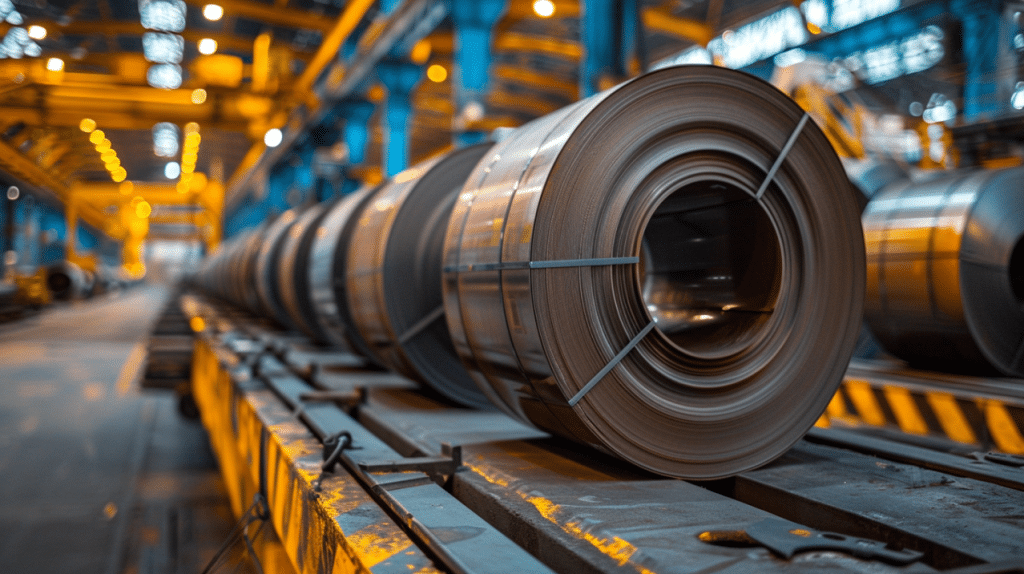
What Is P20 Steel?
P20 steel is a broadly used mold steel, renowned for its excellent balance of durability, toughness, and machinability. It is specifically designed to meet the demands of various industrial applications, most notably in the plastic injection molding industry. This grade of steel has garnered recognition for its outstanding performance in creating large molds, where uniformity and consistency are key.
The composition of P20 steel plays a pivotal role in its desirable properties. It typically contains carbon (C), silicone (Si), manganese (Mn), chromium (Cr), molybdenum (Mo), and in some cases, nickel (Ni). These elements work synergistically to enhance the steel’s hardness, resistance to wear, and ability to be polished to a high finish. The presence of chromium and molybdenum significantly contributes to its excellent hardenability and strength.
P20 steel’s versatility extends to a wide range of applications beyond mold making. Its use is prevalent in tooling applications where resilience against abrasion is required. Additionally, it serves well in die casting dies, forging dies, upsetters, as well as machinery parts where precision and stability are crucial.
One of the prominent advantages of using P20 steel lies in its ease of machinability. Mold makers appreciate the fact that it can be machined with relative ease compared to other tool steels, which helps reduce production times and costs. Moreover, P20 does not require a stringent heat treatment process before use; this distinctive quality makes it more convenient for manufacturers who seek efficiency without compromising quality.
However, while P20 steel offers considerable benefits regarding machinability and initial cost savings, it’s important for potential users to weigh these against any specific project requirements they might have. Each application’s unique demands will determine whether P20’s attributes align well with the intended purpose.
Composition Of P20 Steel
This mold steel is typically formulated from several key elements that define its characteristics. The primary component is iron, making up the majority of the alloy’s base. Alongside iron, carbon is present in a relatively low percentage, usually around 0.28% to 0.40%. This modest amount of carbon contributes to the steel’s hardness while still allowing it to retain good machinability.
Chromium plays a crucial role in P20 steel, with a percentage ranging between 1.40% and 2.00%. Chromium enhances the steel’s hardness, tensile strength, and ability to resist wear and abrasion. It also improves the steel’s resistance against corrosion and oxidation at high temperatures.
Manganese is another essential element found in P20 steel, typically around 0.60% to 1.00%. It functions to improve the hardenability of the steel, contributing to its strength and resistance against shock loads.
In addition to these main components, there are traces of other elements such as molybdenum (approximately 0.30% to 0.55%) and silicon (around 0.20% to 0.80%). Molybdenum aids in increasing temperature strength and hardenability whereas silicon supports deoxidization processes during steel production and helps improve overall structural integrity.
It’s crucial to note that this precise blend of elements provides P20 steel with its notable qualities of uniformity in hardness across large sections, excellent polishability for aesthetic finishes, and reliable through-hardening when heat treated properly.
Applications Of P20 Steel
In the realm of plastics, P20 steel takes center stage as the preferred choice for mold making. Its ability to be polished to a high sheen makes it ideal for creating molds that require smooth finishes, such as those used in the injection molding process for plastics. This characteristic is particularly beneficial when producing high-quality plastic components that demand precise dimensional tolerances.
Beyond the plastics industry, P20 steel finds its place in die casting. Its sturdy composition ensures it withstands the rigorous conditions of die casting processes, marking it as an excellent choice for manufacturing dies that are exposed to high pressure and temperatures. Such resilience amplifies its application scope, encompassing not just plastic moldings but also metal castings.
Tool making is another sector where P20 steel shows substantial aptitude. Tools and dies crafted from this material exhibit enhanced strength and longevity, crucial attributes that make P20 a go-to material. Whether it’s forming tools or jigs and fixtures, the use of P20 steel underlines efficiency and durability.
Pros Of P20 Steel
- Versatility and adaptability: P20 steel is highly versatile and adaptable in various manufacturing scenarios, particularly in the plastic injection molding industry.
- Pre-hardened condition: It comes in a pre-hardened state, eliminating the need for further heat treatment and reducing lead time and costs.
- Uniform hardness: The pre-hardened condition ensures uniform hardness across workpieces, ensuring consistent performance.
- Excellent machinability: P20 steel exhibits excellent machinability, minimizing wear on tools and allowing for high-speed operations, resulting in precise finishes.
- Toughness and strength: It possesses commendable toughness and strength, providing durability under cyclic loading conditions and reducing the risk of cracking.
- Weldability: P20 steel is highly weldable using conventional techniques without predisposing it to flaws or deformities.
- Competitive pricing: Despite its numerous strengths, P20 steel remains competitively priced in the market, offering a cost-effective solution with minimal maintenance requirements over time.
Cons Of P20 Steel
- Susceptibility to Moisture: P20 steel is prone to rust and corrosion when exposed to environments with high moisture levels or corrosive elements, necessitating strict control over storage conditions and potentially requiring additional protective measures during use.
- Temperature Sensitivity: P20’s structural integrity can be compromised when subjected to temperatures outside of its optimal working range, making it less suitable for applications requiring extreme temperature resilience compared to other steel varieties.
- Machinability Challenges: While P20 generally exhibits good machinability, it may struggle to meet the precision and finish requirements of complex machining operations, requiring careful handling to avoid defects and achieve high-quality finishes.
- Cost Considerations: While offering a good balance of performance characteristics for its price point, budget constraints or project specifications may lead to consideration of alternative materials offering either cost advantages or specialized properties tailored to specific demands.
What Is The Difference Between S50c Steel And P20
When comparing S50c steel and P20 steel, it’s essential to examine their differences across several dimensions: strength and durability, weldability and machinability, heat treatment processes, and surface treatment compatibility. These factors play a crucial role in determining the appropriate material for specific applications.
Strength and Durability Comparison
S50c steel is known for its high strength, thanks to its medium carbon content. It offers excellent wear resistance which makes it suitable for parts subjected to high stress. Its durability is a result of its composition and structure, allowing it to withstand heavy loads without deforming.
In contrast, P20 steel, being a mold steel designed specifically for plastic injection molds and die casting dies, also shows admirable strength. However, its focus on toughness more than outright wear resistance distinguishes it from S50c. P20’s alloying elements enhance its ability to absorb shocks making it less prone to cracking under dynamic loading conditions.
Weldability and Machinability
Weldability refers to how easily a material can be welded without developing defects. S50c steel poses certain challenges in this area due to its higher carbon content which requires preheating and post-weld heat treatments to avoid cracks. Machinability-wise, while workable, it does present some challenges in terms of tool wear.
P20 steel is engineered for ease of machining with relatively lower carbon content compared to S50c and the presence of alloying elements such as chromium and molybdenum that improve machinability. Its weldability is also noteworthy because it does not usually require special treatments before or after welding unlike high-carbon steels.
Heat Treatment Processes and Outcomes
Heat treatment enhances the mechanical properties of metals by altering their microstructure through controlled heating and cooling cycles. S50c steel benefits greatly from heat treatment processes like quenching and tempering which significantly increase its hardness and strength but at the cost of some ductility.
On the other hand, P20 steel also responds well to heat treatment with prehardening being a common practice aimed at providing mold makers with a ready-to-use material that doesn’t necessitate further hardening processes thereby simplifying manufacturing steps while maintaining adequate hardness.
Surface Treatment Compatibility
Surface treatments are applied to enhance certain properties such as corrosion resistance or aesthetic appeal. S50c’s carbon content allows for efficient carburizing or hardening surface treatments increasing wear resistance even further. This aspect makes it an attractive option when additional surface robustness is required.
P20 steel’s already good resistance against corrosive elements means lesser demand for protective surface treatments in typical applications; however, it can still benefit from nitriding which provides hard surfaces ideal for molds without compromising on toughness.
Selecting Between S50c Steel And P20: Factors To Consider
When faced with the decision of choosing between S50c steel and P20 for a project, several critical factors come into play. Understanding these can significantly impact the outcome of your venture.
Project Requirements (Durability, Strength, Resistance)
The first aspect to consider is the specific requirements of your project in terms of durability, strength, and resistance. Each type of steel boasts unique properties that make it suitable for different applications. S50c steel is known for its excellent wear resistance and strength, making it ideal for high-stress environments where components are subject to continuous wear. On the other hand, P20 steel is recognized for its outstanding toughness and ability to withstand cyclic stresses, which is essential in mold-making processes where dimensional stability under heat treatment is crucial.
Budget Constraints And Cost Analysis
Your budget plays a substantial role in determining the choice between S50c and P20 steels. Generally, the cost can vary based on availability, demand, and raw material prices at the time of purchase. Conducting a thorough cost analysis will help identify which option delivers the required performance at a more economical price point. This involves considering not only the initial expense but also long-term maintenance and replacement costs.
Availability And Sourcing Considerations
Finally, consider the availability and sourcing of these materials. Depending on your geographical location or global market dynamics at any given time, one type of steel may be more readily accessible than the other. Ensuring a consistent supply chain for your chosen material is vital to prevent project delays or increases in cost due to scarcity.
In Conclusion
In summary, the main distinctions between S50C steel and P20 lie in their chemical compositions, mechanical properties, and applications, making each suited for specific industrial purposes.
Explore our comprehensive range of S50C and P20 steel products to find the perfect material for your next project. Contact us for expert guidance and to ensure you make the best choice tailored to your needs.