P20 steel plate is a versatile, pre-hardened mold steel known for its exceptional machinability, weldability, and dimensional stability. Utilized extensively in the plastic injection moulding and die casting industries, it offers an optimal blend of hardness, toughness, and resistance to abrasive wear. This guide aims to provide a comprehensive overview of P20 steel plate applications, processing techniques, and tips for achieving optimum performance in industrial settings.
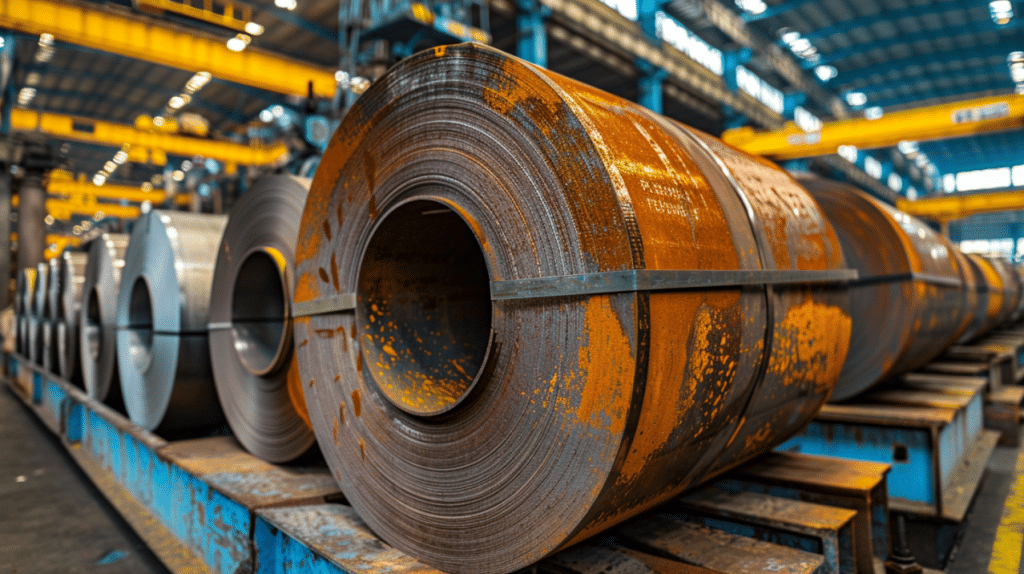
What Is P20 Steel Plate
P20 steel plate is recognized globally as a versatile, low-alloy tool steel that characterizes notable toughness at moderately elevated temperatures. The designation ‘P20’ refers specifically to a standard mold steel grade, which has been effectively utilized in the manufacturing of various plastic injection molds due to its exceptional combination of hardness, machinability, and weldability.
The P20 steel plate is distinguished by its balanced composition, which plays a crucial role in achieving a uniform hardness across the piece. This characteristic not only facilitates an ease of use during machining processes but also substantially enhances the finished product’s durability and longevity. Employed primarily within the realms of tool making and mold production, this particular grade of steel finds extensive application across many sectors including but not limited to automotive manufacturing and consumer goods production.
Unique among tool steels for its composition that includes chromium, manganese, and molybdenum, P20 stands out for its pre-hardened state. This property means it does not require further heat treatment before being put to work, setting it apart from many other tool steels that need rigorous heat treating processes to reach full utility.
This feature greatly simplifies the fabrication process of tools and dies from P20 steel plate, allowing manufacturers to save significant time and resources. Furthermore, its excellent machinability contributes towards more precise finishes with less waste material during the fabrication phase. Furthermore, P20’s welding properties are commendable; thanks to its alloying elements providing enhanced cohesion during welds thus minimizing potential weaknesses in mold structures.
Composition Of P20 Steel Plate
At the core of P20 steel’s composition is carbon and chromium. Carbon content in P20 steel typically ranges around 0.28 to 0.40%, which contributes to the material’s strength and hardness. Chromium, present at approximately 1.4 to 2.0%, enhances corrosion resistance, an essential trait for tools exposed to adverse conditions or materials.
Manganese and molybdenum are also integral components of P20 steel, found at levels around 0.60 to 1.0% and 0.30 to 0.55% respectively. Manganese improves the steel’s forgeability and weldability, making it easier to shape and join pieces without compromising their structural integrity. Molybdenum works alongside chromium; it increases tensile strength at high temperatures, ensuring that tools maintain their shape under stress.
Additionally, silicon resides in the composition, usually from 0.20 to 0.80%. This element optimizes deoxidation processes during manufacturing, vital for achieving purity and clarity in the finished product’s surface.
Nickel can be found as well, albeit at a lower percentage (approximately 0.85 to 1.15%), yet plays a crucial role by enhancing toughness across various temperatures — an important factor for molds subjected to cyclic heating and cooling during their service life.
Mechanical Properties Of P20 Steel Plate
One of the primary characteristics of P20 steel plate is its impressive hardenability. This property ensures that the steel can be hardened through thermal treatments, achieving a uniform hardness even in thicker sections. Such an attribute is particularly beneficial when producing large molds or components where consistent performance across the part is critical.
In terms of tensile strength, P20 exhibits a robust profile, lending it the ability to withstand high levels of stress without succumbing to deformation or failure. This strength plays a crucial role in extending the lifetime of tools and dies fabricated from P20 steel plate, especially under cyclic loads or pressures.
Moreover, P20 steel plate possesses excellent ductility. This feature allows it to be formed into complex shapes without losing its toughness or accruing damage. For manufacturers, this means more versatile design possibilities and easier machining processes.
The impact resistance of P20 also stands out as a notable property. Even in pre-hardened states, it demonstrates significant resilience against sudden forces or shocks. Such resistance is valuable in safeguarding tools and components during demanding operations or accidental drops.
Finally, fatigue resistance contributes to the enduring appeal of P20 steel plate among tool makers. Its ability to withstand repeated cyclic stresses without exhibiting signs of wear or failure ensures reliability and longevity in finished products, minimizing downtime and maintenance requirements.
Comparative Analysis With P20 Steel Plate and Other Common Tool Steels (D2, A2)
P20 steel is renowned for its good machinability, excellent dimensional stability during heat treatment, and uniform hardness. This makes it an ideal choice for intricate moulds requiring detailed work without the risk of deformation. The balance between chromium, molybdenum, and nickel grants P20 a unique position in terms of weldability and polishability compared to its counterparts.
On the other hand, D2 steel is known for its high wear resistance and ability to retain a sharp edge, attributed to its higher chromium content which gives it high hardenability. This characteristic makes D2 suitable for cutting tools that encounter abrasive materials but can lead to challenges in machinability and grinding due to its rigidity.
A2 steel falls somewhere between P20 and D2 regarding wear resistance and toughness. It offers a balanced combination that many tool makers appreciate: decent machinability along with good dimensional stability post-heat treatment. A2’s air-hardening property also simplifies the heat treatment process compared to P20’s requirement for preheating and tempering cycles.
Ultimately, the choice between P20, D2, and A2 hinges on the specific requirements of the application at hand. While P20 excels in situations where flexibility, polishability, and welding are paramount; D2 stands out when wear resistance takes precedence; meanwhile, A2 offers a midway point with moderate wear resistance but better machinability than D2.
Applications Of P20 Steel Plate
The primary use of P20 steel plate is found in the plastic injection molding industry. It serves as a standard material for mold bases and tooling due to its excellent machinability, uniform hardness across sections, and minimal distortion during the heat treatment process.
P20 steel plate is also frequently utilized in the making of die holders, backers, casings, and support tooling. The automotive sector relies on this steel for forming complex parts with fine surface finishes. Its durability and resilience make it suitable for constructing core and cavity plates for soft plastics molds. Additionally, the presence of sulfur enhances its machinability without significantly affecting its mechanical properties, which is particularly beneficial when crafting intricate details.
Beyond these primary uses, P20 steel finds applications in sectors requiring high precision and robustness from their components. This includes but is not limited to the aerospace industry for non-structural parts, general tooling applications where good polishability is a requirement, and even in manufacturing pre-forming tools.
Each application benefits substantially from P20’s blend of properties – providing a balance between ease of machining and structural integrity after processing. Noteworthy is its employment in low-volume production tools where flexibility in materials used can offer cost-effective solutions without compromising on quality or performance.
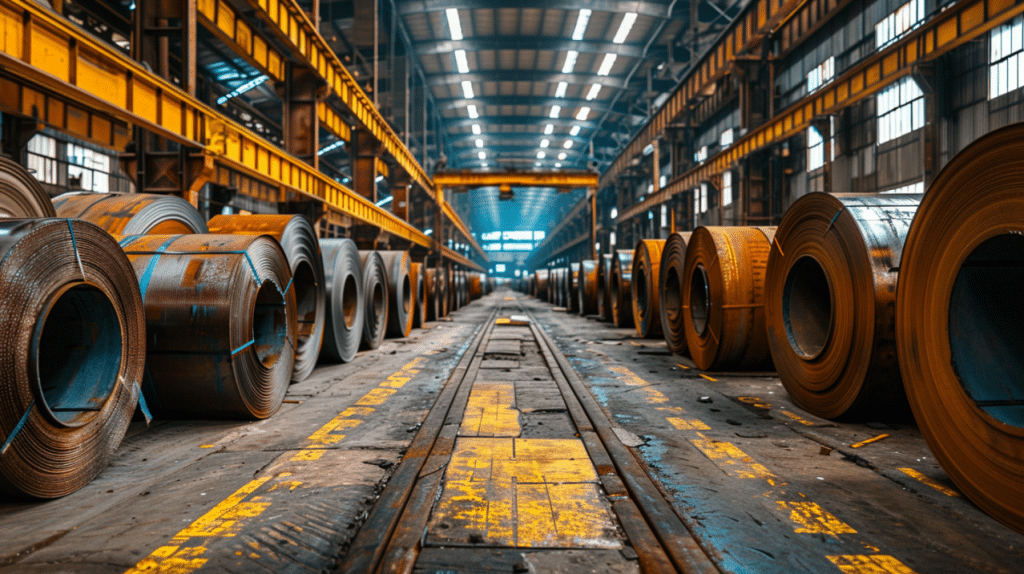
Machining Guidelines Of P20 Steel Plate
P20 steel’s machinability allows for the use of both traditional and modern machining methods. However, considering its weldability and relatively low carbon content compared to other tool steels like D2 or A2, certain adaptations in technique are beneficial. High-speed steel (HSS) or carbide tools can be employed effectively, but selecting the right cutting fluids is essential to reduce wear and prevent overheating.
Before initiating the machining process, understanding the material’s condition is crucial. Pre-hardened P20 steel plates can be machined directly without further heat treatment; this quality significantly reduces processing time and cost. It’s advisable to maintain a consistent machining speed that aligns with the tool material. Overly aggressive speeds might lead to premature tool wear or even damage to the steel surface.
The tool path strategy also plays a significant role in optimizing machining operations on P20 steel plates. Employing techniques such as climb milling can enhance surface finish and extend tool life by distributing the load more evenly. Additionally, incorporating regular breaks or ‘peck’ cycles when drilling deep holes ensures better chip evacuation and reduces heat build-up.
Tool geometry needs particular attention when working with P20 steel. Tools with positive rake angles are preferred as they aid in reducing cutting resistance and thus minimize heat generation. Moreover, applying adequate coolant flow is indispensable for maintaining temperature control during intensive machining tasks. Coolants not only dissipate heat but also assist in flushing away chips from the cutting zone, preventing potential re-cutting that might degrade the workpiece quality.
Finally, after completing the machining operations on a P20 steel plate, it is advisable to conduct an inspection of both the workpiece and tools used. Checking for signs of wear or damage can inform adjustments for future runs, ensuring continuous improvement in machining efficiency and outcome quality.
Heat Treatment and Surface Finishing of P20 Steel Plate
P20 steel plate, known for its remarkable versatility and superiority in molding applications, requires specific heat treatment processes to achieve optimal performance. The heat treatment of P20 steel involves several critical steps designed to enhance its mechanical properties, including hardness, toughness, and dimensional stability.
Initially, the procedure commences with preheating at a temperature range between 500°C to 800°C. This step is crucial for gradually raising the temperature of the steel to avoid thermal shock. Subsequently, austenitizing follows, where the material is heated to a higher temperature range typically between 840°C to 870°C. Maintaining this temperature ensures uniformity in the transformation of the steel’s microstructure.
Quenching is the next vital phase in the heat treatment process. Here, rapid cooling is accomplished using a suitable medium such as oil or forced air. This step is essential for locking in the desired mechanical properties by transforming austenite into martensite. To alleviate stresses induced during quenching and to improve toughness, tempering is performed post-quenching by heating the steel to a lower temperature range around 550°C to 650°C before cooling it down gradually.
Surface finishing plays a pivotal role in enhancing P20 steel’s wear resistance and aesthetic appearance. Common surface finishing techniques include polishing and coating with protective layers. Polishing enhances mold release properties while reducing corrosion susceptibility by removing surface irregularities. Coatings can further elevate wear resistance and reduce maintenance needs; common coatings include nitriding and chrome plating which impart additional surface hardness and corrosion protection.
Regular maintenance through appropriate treatments secures both functionality and longevity of P20 steel plates in demanding tooling applications. These carefully calibrated procedures ensure that P20 tooling plate meets stringent operational standards required for high-performance tool steels.
Maintenance And Care For P20 Steel Plate
Maintaining and caring for P20 steel plate is paramount in extending its lifespan and ensuring it remains in optimal working condition. Proper maintenance routines not only prevent premature wear but also contribute to the consistent performance of tools crafted from this material.
Regular cleaning is a fundamental step in maintaining P20 steel plates. It involves removing any residues, such as oils, coolants, or workpiece materials, that may have accumulated during machining processes. Use soft cloths or brushes and compatible cleaning solvents to avoid abrasive damage to the surface of the plate.
Lubrication plays a crucial role in preserving P20 steel. After each cleaning session, applying a thin layer of protective oil can help in preventing rust and corrosion, especially when the plates are stored for an extended period. Selecting the right type of oil is essential; lightweight machine oils often offer adequate protection without leaving heavy residues.
Inspection routines are indispensable in identifying early signs of wear or damage on P20 steel plates. Regularly examining the surface for scratches, dents, or any form of deformation aids in addressing issues before they escalate into significant problems. Implementing a schedule for these inspections ensures that checks are neither overlooked nor delayed.
When it comes to storage, keeping P20 steel plates in a controlled environment can greatly influence their longevity. Avoid areas prone to moisture exposure or drastic temperature changes as these conditions can accelerate corrosion processes. Ideally, store these plates in dry, temperature-stabilized spaces to mitigate potential environmental damages.
Lastly, handling practices should be optimized to minimize risk to the steel plates. Using appropriate lifting equipment and techniques reduces chances of dropping or improperly stacking the plates, which could lead to surface damage or warping.
By adhering to these maintenance and care guidelines for P20 steel plate, users can ensure their tools remain durable and reliable over time. Proper upkeep not only safeguards the investment made into acquiring this premium tool steel but also supports consistent manufacturing quality by preventing tool failure due to material degradation.
Common Challenges And Solutions
When working with P20 steel plate, professionals encounter a range of common challenges. Understanding these hurdles thoroughly can pave the way for more efficient and effective use of this versatile tool steel.
Challenge: Machinability
P20 steel’s unique composition is designed for excellent machinability, but its hardness can pose challenges. Utilizing proper tooling and adjusting machining parameters such as speed, feed rate, and depth of cut are critical steps for navigating this challenge.
Solution: Employ carbide or cermet tools for their enhanced wear resistance and toughness. Additionally, implementing a stable setup and using coolants can significantly improve machining performance.
Challenge: Heat Treatment Distortion
During the heat treatment process, P20 steel plates may experience distortion due to uneven heating or cooling rates.
Solution: To minimize distortion, ensure uniform heating and control the cooling process carefully. Preheating before hardening can also help in reducing thermal stresses that lead to distortion.
Challenge: Surface Oxidation
P20 steel is susceptible to surface oxidation if not properly protected during heat treatment or when exposed to harsh environments.
Solution: Applying protective coatings or using controlled atmospheres during heat treatment can effectively shield the surface from oxidation. Regular maintenance and proper storage conditions also play crucial roles in preventing rust formation.
Challenge: Welding Difficulties
Welding P20 steel requires special attention due to its alloying elements which make it prone to cracking if not handled correctly.
Solution: Use low hydrogen welding methods and preheat the material before welding to reduce the risk of cracking. Selecting the appropriate filler material that matches the base metal’s properties is also vital for achieving strong welds.
In Conclusion
The P20 steel plate’s versatile characteristics make it an indispensable asset for tooling applications where durability and performance are paramount.
Discover how our range of P20 steel plates can elevate your projects to new heights. Explore our collection today and experience the difference in quality and service that sets us apart.