P20 grade steel is a versatile, low-alloy tool steel that is characterized by its excellent moldability, machinability, and toughness. It is widely used in the manufacturing industry, particularly in mold making for injection molding and die casting due to its unique balance of strength and ductility. P20 steel is pre-hardened, which allows it to be used directly without the need for further heat treatment, saving time and cost in the production process. This article aims to provide a detailed overview of P20 grade steel, including its composition, properties, applications, and benefits.
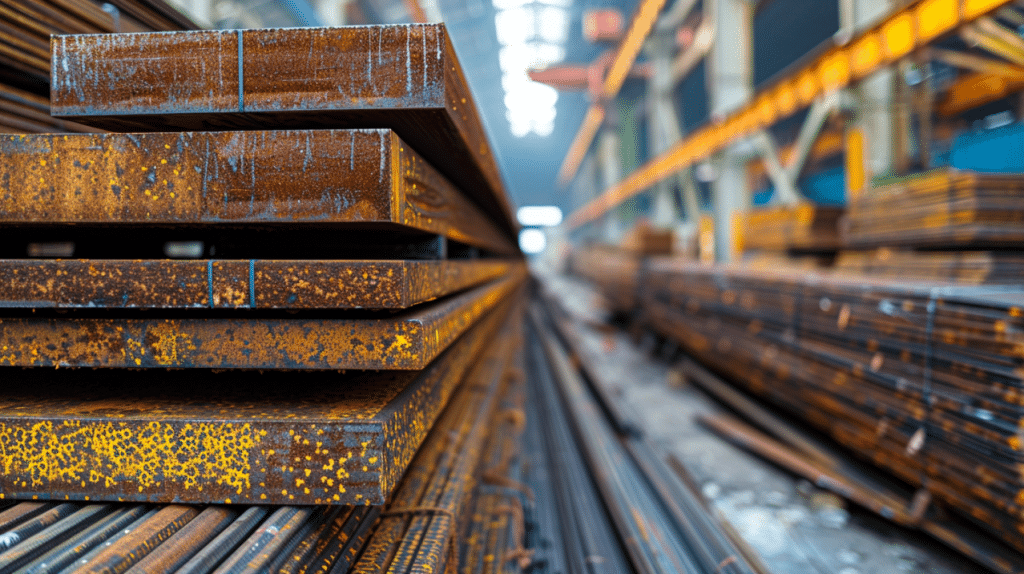
What Is P20 Grade Steel
P20 grade steel is a versatile, low-alloy tool steel that is characterized by its good machinability at relatively high hardness levels. It falls under the category of mold steels and is known for its excellent combination of toughness, strength, and dimensional stability in heat treatment. This makes it particularly well-suited for manufacturing a variety of molds and dies, especially for plastic injection molding applications.
P20 steel comes pre-hardened, which significantly reduces the need for further heat treatment processes after machining or forming. This pre-hardening also contributes to consistency across parts and dies made from P20, ensuring uniform performance during use. In addition to this, the steel’s capability to be polished to a high finish is beneficial for industries where aesthetics are just as important as functionality, such as consumer goods manufacturing.
Being a mold steel, P20 grade exhibits an optimal balance of alloying elements. While not overly alloyed like some high-performance tool steels, its composition provides enough wear resistance and toughness for many standard applications in mold making. Furthermore, its relatively straightforward composition allows it to be modified with sulfur or other additives to enhance specific properties such as machinability or corrosion resistance for particular applications.
The versatility of P20 grade steel extends beyond mold-making into other industrial applications where similar characteristics are valued. For instance, its resistance to indentation (hardness) coupled with ductility makes it suitable for various engineering components that require precision under abrasive conditions or high-impact environments.
P20 grade steel stands out as a preferred material choice in the realm of tool and mold making due to its pre-hardened state, balanced chemical composition offering a mix of toughness and strength, and ability to undergo modifications to meet specific application needs.
Chemical Composition Of P20 Steel
- Iron (Fe): Constitutes the majority of the alloy’s volume.
- Carbon (C): Approximately 0.28-0.40%, crucial for determining hardness and strength.
- Chromium (Cr): About 1.4-2.0%, provides wear and corrosion resistance.
- Molybdenum (Mo): Around 0.30-0.55%, enhances toughness and hardenability.
- Manganese (Mn): Within 0.60-1.00%, facilitates forging process.
- Silicon (Si): Found in 0.20-0.80%, improves tensile strength and aids deoxidization.
- Sulphur (S) and Phosphorus (P): Limited to below 0.05% to minimize adverse effects.
- Nickel (Ni): Occasionally present in minimal amounts, not a standard component.
Element | Content (%) |
---|---|
C | 0.28-0.40 |
Mn | 0.60-1.00 |
Si | 0.20-0.80 |
Cr | 1.40-2.00 |
Mo | 0.30-0.55 |
Cu | 0.25 |
P | 0.03 |
S | 0.03 |
Physical And Mechanical Properties Of P20 Steel
- Physical Properties of P20 Steel:
- Toughness: Remarkable toughness enables P20 steel to withstand significant stress without cracking or breaking, particularly valuable for durable molds enduring repeated cycling.
- Mechanical Properties of P20 Steel:
- Tensile Strength: Typically in the range of 900-1100 MPa, allowing P20 steel to handle heavy loads without failure.
- Yield Strength: Moderate, capable of resisting deformation under load.
- Elongation at Break: Approximately 15-20%, indicating its ductility and adaptability under tensile forces.
- Impact Resistance: Exhibits excellent resilience against sudden forces or shocks, ideal for tools and dies subjected to high impact conditions.
- Hardness: Pre-hardened P20 steels usually have a hardness level around 28-34 HRC (Rockwell Hardness), suitable for many tooling applications with the option for further heat treating if higher hardness levels are needed.
Property | Metric | Imperial |
---|---|---|
Hardness, Brinell (typical) | 300 | 33 |
Hardness, Rockwell C (typical) | 30 | 30 |
Tensile strength, ultimate | 965-1030 MPa | 140000-150000 psi |
Tensile strength, yield | 827-862 MPa | 120000-125000 psi |
Elongation at break (in 50 mm (2″)) | 20.0% | 20.0% |
Compressive strength | 862 MPa | 125000 psi |
Charpy impact (V-Notch) | 27.1-33.9 J | 20.0-25.0 ft-lb |
Poisson’s ratio | 0.27-0.30 | 0.27-0.30 |
Elastic modulus | 190-210 GPa | 27557-30457 ksi |
Density | 7.85 g/cc | 0.284 lb/in3 |
Applications Of P20 Steel
P20 grade steel exhibits a unique set of characteristics that make it an ideal choice for a broad range of applications. Its popularity primarily stems from its excellent machinability, impressive durability, and relatively low cost. The practical uses of P20 steel span across various industries, reflecting its versatility and reliability as a material.
In the realm of toolmaking, P20 steel is highly valued for its ease of machining and ability to hold a sharp edge. This makes it a top choice for creating molds that are used in plastic injection molding processes. The resistance to wear and tear ensures that these molds can withstand repeated use without significant degradation, leading to consistent product quality over time.
Beyond toolmaking, P20 steel finds utility in the manufacturing of die holders, bolster plates, and other components within stamping dies. Its toughness allows it to endure the high pressures and abrasive conditions inherent in metal stamping operations. Moreover, the uniform hardness of P20 steel contributes to its widespread use in this context, providing a balance between strength and flexibility needed for intricate shaping processes.
The automotive industry also benefits from the properties of P20 grade steel. Parts such as panel molds and other large injection-molded components are commonly fabricated from this material due to its ability to maintain structural integrity under stress. This attribute is crucial in ensuring that automotive parts meet safety standards while minimizing production costs.
In aerospace applications, P20 steel is occasionally selected for the manufacture of specific non-critical parts where its mechanical properties align with the requirements of the application. While not as common in this sector compared to others, its inclusion showcases the adaptability of P20 steel across different technological and engineering fields.
Given these wide-ranging applications, P20 grade steel proves itself as a versatile material option capable of meeting diverse industrial needs. Its blend of machinability, toughness, and cost-effectiveness positions it as a preferred choice among manufacturers seeking efficiency without compromising on quality or performance.
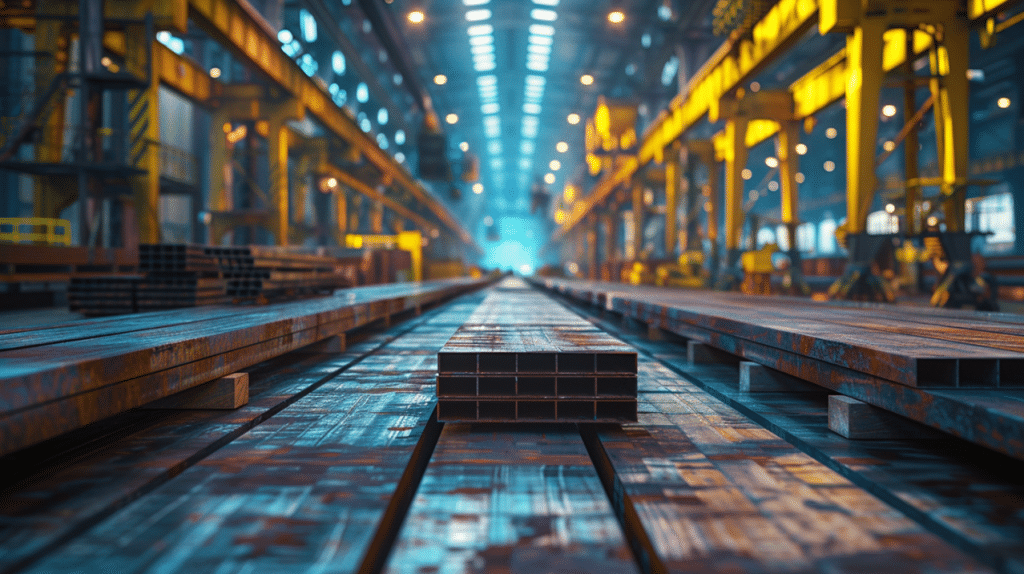
Machinability and Weldability
Machinability of P20 Grade Steel
P20 grade steel is revered for its excellent machinability among tool steels, attributed largely to its uniform hardness throughout the material. This quality ensures that when machined, the steel exhibits minimal resistance, a feature that significantly reduces wear on cutting tools and machinery. As a result, it allows for high-speed machining operations without compromising the integrity or finish of the final product. Manufacturers can achieve precise dimensions and smooth surfaces with relative ease, making P20 an ideal candidate for intricate moldings and detailed tooling applications.
The alloy composition of P20 steel plays a crucial role in enhancing its machinability. The presence of chromium, molybdenum, and nickel in balanced proportions aids in maintaining consistent hardness and reduces brittleness which can be a bane during machining processes. However, despite its favorable properties, working with P20 requires adherence to optimal speeds and feeds to exploit its machinability fully. Employing appropriate cutting fluids can also improve results by reducing temperatures and friction during machining tasks.
Weldability of P20 Grade Steel
In addition to its machinability, P20 grade steel offers commendable weldability characteristics. This trait is particularly valuable in industries where modifications or repairs on molds and dies are frequent requirements. P20’s pre-hardened state contributes significantly here since it permits welding without the need for preheating—a step often vital for other higher-grade steels to prevent cracking.
When welding P20 steel, utilizing low hydrogen electrodes is recommended to prevent potential cracking issues associated with hydrogen embrittlement. Techniques such as TIG (Tungsten Inert Gas) welding are particularly well-suited for this material due to their capacity for precision and control over heat input, further minimizing the risk of thermal distortion or defects in the weld area.
Although P20’s weldability simplifies maintenance and repair tasks considerably, achieving optimum results necessitates skillful application of welding techniques and adherence to specified parameters including proper electrode selection and control over cooling rates post-welding.
In essence, the superior machinability and weldability attributes of P20 grade steel not only streamline manufacturing processes by offering enhanced work efficiency but also ensure high-quality outcomes in mold-making industries. These properties contribute markedly towards reducing production downtime through faster machining rates and convenient repair capabilities—which ultimately translates into cost savings and increased productivity levels.
Heat Treatment
Heat treatment processes are pivotal in modifying the physical and mechanical properties of P20 grade steel, making it more suitable for specific applications. The heat treatment of P20 steel entails a series of thermal operations including hardening, tempering, and annealing, aimed at achieving the desired level of hardness, toughness, and strength.
The process generally starts with preheating to mitigate thermal shock during hardening. Preheating is done in two stages: first at 500-800°C followed by a second stage heating at 840-870°C. Subsequently, the material is austenitized at a temperature range of 840-870°C where it is fully transformed into austenite. This step is crucial as it determines the final mechanical properties of the steel.
Following austenitization, the P20 steel undergoes quenching. Quenching involves rapid cooling usually in oil or forced air to achieve a martensitic structure. This sudden drop in temperature enhances the hardness and tensile strength but at the expense of ductility and toughness.
To alleviate this brittleness caused by quenching, tempering is employed as a subsequent stage. During tempering, the P20 steel is heated to temperatures typically between 550°C and 650°C depending on the desired properties. The process allows for some recrystallization and transformation of unstable martensite into tempered martensite, thereby improving toughness while slightly reducing hardness.
Annealing could also be performed as an alternative heat treatment method to obtain maximum machinability rather than optimized strength or toughness. This involves heating up to around 760°C – 780°C followed by slow cooling which results in a structure that’s softer but easier to machine.
Each step within these heat treatment processes must be carefully controlled including maintaining time durations and cooling rates to ensure that the final product meets specified requirements in terms of its physical and mechanical characteristics.
Advantages Of Using P20 Grade Steel
- Excellent Machinability: P20 grade steel offers exceptional machinability, reducing manufacturing time and costs while maintaining precision in the final product.
- Outstanding Polishing Ability: The steel’s superior polishing ability results in high-quality surface finishes, making it ideal for molds requiring fine detailing and smooth finishes.
- Uniform Hardness: P20 steel exhibits uniform hardness throughout the workpiece, ensuring consistent performance and reducing the likelihood of defects in the final product.
- Dimensional Stability: During heat treatment processes, P20 steel maintains excellent dimensional stability, minimizing warping and distortion and allowing for tight tolerances and accurate dimensions.
- Good Weldability: P20 steel’s good weldability enables effective repairs and alterations without compromising structural integrity, making it adaptable to dynamic manufacturing environments.
Considerations And Limitations
- Hardness: P20 grade steel’s hardness is both an advantage and a limitation. While its pre-hardened state reduces the need for further heat treatment and expedites production timelines, this characteristic can also limit the material’s suitability for applications requiring extreme hardness or durability under severe conditions. Thus, when selecting P20 steel for a project, it’s imperative to thoroughly assess the operational demands of the application.
- Cost Implication: Another consideration is the cost implication of using P20 steel. Although P20 grade steel is relatively cost-effective due to its ease of machining and minimal need for heat treatment post-casting, initial acquisition costs can be high. This aspect is particularly critical for large-scale projects where material expenditures significantly impact overall budgeting.
- Thermal Conductivity: The thermal conductivity of P20 grade steel also presents limitations in applications subjected to high temperatures. Its performance may falter in environments where enhanced thermal stability is required, possibly affecting long-term reliability and functionality of components made from this material.
- Machinability and Weldability: Furthermore, while P20 steel offers good machinability and weldability, these properties do not necessarily translate across all variants or modified forms of P20 steel. Specialized applications might necessitate additional processing or alloying elements that could alter these properties adversely.
What Is The Difference Between P20 And 4140 Steel?
P20 grade steel is widely recognized for its excellent moldability, making it a preferred choice for the mold industry. It contains a mix of chromium, molybdenum, and nickel, which contributes to its high toughness and good machinability. This type of steel is pre-hardened, allowing it to be directly used for tooling without undergoing additional heat treatment processes. Its ability to maintain uniform hardness throughout even large sections makes P20 particularly advantageous for large plastic molds.
On the other hand, 4140 steel belongs to the category of alloy steels containing chromium, molybdenum, and manganese. Known for its outstanding toughness and high fatigue strength, 4140 is typically used in applications requiring high impact resistance or stress. Unlike P20, 4140 steel undergoes a heat treatment process to achieve desired mechanical properties. It offers versatility in terms of hardness levels through tempering or annealing methods. This adaptability makes it suitable for a myriad of uses beyond mold making such as gears, axles, and shafts where higher levels of strength and wear resistance are necessary.
When comparing these two types of steel directly regarding their chemical composition and mechanical properties, it’s clear that each has been optimized for specific applications. P20’s alloying elements give it superior polishability and photo-etching properties beneficial for clear plastic molds needing fine finishes. Meanwhile, 4140’s balanced composition provides a blend of ductility with high strength making it ideal when durability is critical.
One notable difference lies in their weldability; P20’s pre-hardened condition means welding should be performed with care to avoid altering its properties unfavorably. Conversely, 4140 can be more readily welded due to its adaptable heat-treated state but requires preheating and post-weld heat treatments to maintain integrity.
What Is P20 Steel Equivalent To?
P20 steel, used in various industries for precision and durability, has equivalents like Europe’s 1.2311 and 1.2312, Germany’s DIN 40CrMnMo7, and Japan’s SCM4. These alternatives offer similar properties, making them suitable replacements in automotive and electronics applications.
Is P20 A High Carbon Steel?
P20 steel is not considered high carbon steel because its carbon content is between 0.28% to 0.40%, which is lower than the over 0.60% found in high carbon steels. This makes P20 ideal for mold-making due to its great machinability and balance of strength and ductility.
Is P20 A Hardened Steel?
P20 steel, while pre-hardened, isn’t as hard as high-carbon steels but offers ease of machining and good durability for various applications. Its balance between machinability and hardness makes it a versatile choice for molds and dies, without being the hardest steel available.
In Conclusion
P20 grade steel represents a versatile, mold-quality alloy known for its balance between hardness and machinability, making it ideal for a variety of applications.
To learn more about how P20 steel can benefit your manufacturing process or to explore other material options, we invite you to reach out and speak with our experts. Don’t miss the opportunity to enhance your projects with the right materials; contact us today.