P20 steel is a versatile, low-alloy tool steel widely used in various applications due to its excellent machinability, good polishability, and uniform hardness properties. Understanding the hardness of P20 steel is crucial for manufacturers and engineers as it directly impacts the material’s performance in mold making and other tooling applications. This article provides a comprehensive overview of the hardness characteristics of P20 steel, along with factors that influence its hardness and implications for its use in the industry.
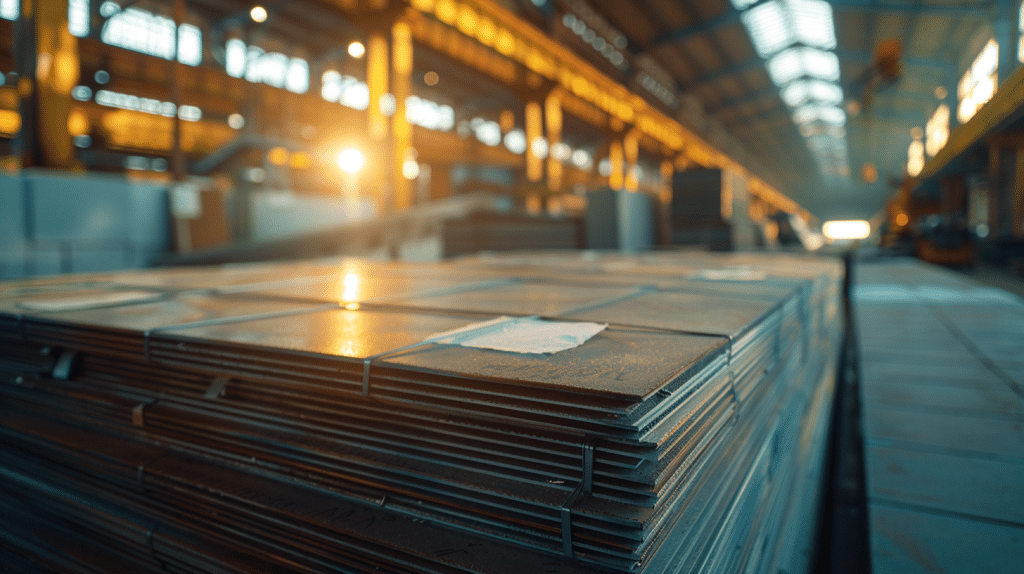
What Is P20 Steel?
P20 steel is a widely recognized mold steel, belonging to the category of pre-hardened plastic mold steels. Largely utilized in the manufacturing industry for making plastic molds and die-casting dies for zinc, P20 steel stands out due to its remarkable blend of properties such as good machinability, exceptional polishability, and strong toughness. This versatility makes it a preferred choice for crafting a vast array of molds that require high precision and longevity.
The composition of P20 steel is finely tuned to deliver its distinct characteristics. It typically contains a moderate amount of carbon (0.28 – 0.40%), which contributes to its hardness and strength while maintaining good machinability. The presence of chromium (1.40 – 2.00%) enhances its resistance to wear and corrosion, adding to the durability of tools crafted from this steel. Moreover, elements like manganese (0.60 – 1.00%) are incorporated to improve its hardenability without compromising on ductility or toughness.
Nickel (0.85 – 1.15%) forms another critical component of P20’s composition, serving to increase toughness—a crucial trait for mold materials that must withstand cyclic stress during operation without fracturing. In addition, small quantities of molybdenum (0.15 – 0.25%) are added to refine the material’s grain size and enhance uniformity in physical properties across the tool, ensuring reliable performance under varying conditions.
This strategic composition renders P20 steel particularly effective in applications requiring high wear resistance coupled with excellent dimensional stability during heat treatment processes—an invaluable advantage in mold-making where precision is paramount.
The Hardness Of P20 Steel (In Rockwell, Brinell, And Vickers Scales)
The hardness of P20 steel is a critical factor to consider for its applications in tooling and mold making. This property greatly influences the material’s resistance to wear and deformation under stress, key attributes for its intended uses. The hardness of P20 steel can be measured using different scales: Rockwell, Brinell, and Vickers. Each scale provides valuable insights into how the material will perform under specific conditions.
Starting with the Rockwell scale, often abbreviated as HRC when referring to the C scale, which is most applicable for measuring the hardness of P20 steel. In general, P20 steel has a hardness range on the Rockwell scale from 28HRC to 32HRC after quenching and tempering processes. This range indicates a moderate level of hardness that is optimal for plastic injection molds due to its balance between hardness and toughness.
Moving on to the Brinell hardness test, which employs a different method by applying a known load (usually measured in kilograms) over a hard indenter ball made out of tungsten carbide. For P20 steel, Brinell hardness values are typically found within the range of approximately 280HBW to 320HBW. This test offers an alternative perspective on material density and resistance compared to Rockwell measurements but correlates well across these materials.
Lastly, we discuss Vickers hardness—a method involving an indenter in a pyramid shape applied with a specific force onto the material surface. The Vickers test is valuable because it can provide accurate readings even on small parts or thin surfaces where other tests might not be viable. For P20 steel, Vickers hardness values are generally similar to those from Brinell testing but offered in different units; they fall in an approximate range from around 290HV to 330HV.
How To Measure P20 Steel Hardness
There are three primary methods used to measure the hardness of P20 steel: Rockwell, Brinell, and Vickers scales. Each method offers unique insights into the material’s properties, enabling manufacturers and engineers to make informed decisions about its application.
The Rockwell hardness test is perhaps the most widely utilized due to its quick execution and minimal material damage. It measures the depth of penetration by a diamond or ball indenter under a major load, after a minor preload is applied. The result is reported as an HRC value (Rockwell C Hardness), which is a direct indicator of P20 steel’s resistance to plastic deformation.
Conversely, the Brinell hardness test determines hardness by measuring the diameter of an indentation left by a hardened steel or carbide ball pressed against the specimen under a known load. This method provides an HB value indicative of material hardness and is particularly useful for testing materials with heterogeneous or coarse structures.
The Vickers hardness test, on the other hand, allows for precise measurements over a wide range of hardness levels by employing a pyramid-shaped diamond indenter. The size of the square indentation produced under load is measured using a microscope, from which the HV (Vickers Hardness) value is calculated. This versatility makes it applicable for evaluating very hard materials like P20 steel following heat treatment or processes that alter its properties.
Regardless of which testing method is chosen, proper preparation of the specimen’s surface is crucial for accurate results. Irregularities such as scratches or uneven finishes can lead to erroneous readings.
Factors Influencing The Hardness Of P20 Steel
P20 steel is renowned for its optimal balance of toughness, hardness, and machinability. However, the hardness of this tool steel can vary depending on several factors. Understanding these elements is crucial for industries that demand specific hardness levels in their P20 steel applications.
Chemical Composition
One primary factor influencing the hardness of P20 steel is its chemical composition. P20 steel typically contains carbon, chromium, molybdenum, and manganese. The precise alloying percentages can alter the material’s hardness. Higher carbon content tends to increase the hardness levels but might reduce the steel’s toughness. Alloying elements like chromium and molybdenum enhance wear resistance and strength, contributing to overall hardness.
Manufacturing Process
The manufacturing process also plays a vital role. Melting techniques, forging or rolling temperatures, and cooling rates directly impact the microstructure of P20 steel. A controlled manufacturing process ensures uniform distribution of carbides within the matrix, which is essential for achieving consistent hardness across the material.
Heat Treatment
Heat treatment processes significantly affect P20 steel’s hardness. Annealing, quenching, and tempering are commonly used methods to adjust the properties of P20 steel. The heat treatment protocols—temperature ranges used during quenching and tempering periods—are finely tuned to achieve desired hardness levels without compromising toughness.
Thermal cycling during heat treatment leads to phase transformations in P20 steel—alterations from austenite to martensite phases—that determine the final hardenability of the material. Specifically designed cooling processes help in obtaining a desirable combination of high strength and adequate ductility.
Environmental Factors
Furthermore, environmental factors during storage or application can influence the microstructural stability of P20 steel over time. Exposure to extreme temperatures or corrosive environments may gradually alter its structural integrity and hence its measured hardness.
Mechanical Working
Lastly, mechanical working post-manufacturing such as machining or grinding can induce surface hardening effects due to localized plastic deformation increasing torsional stress resistance but could potentially introduce stress concentrations affecting overall durability if not properly managed.
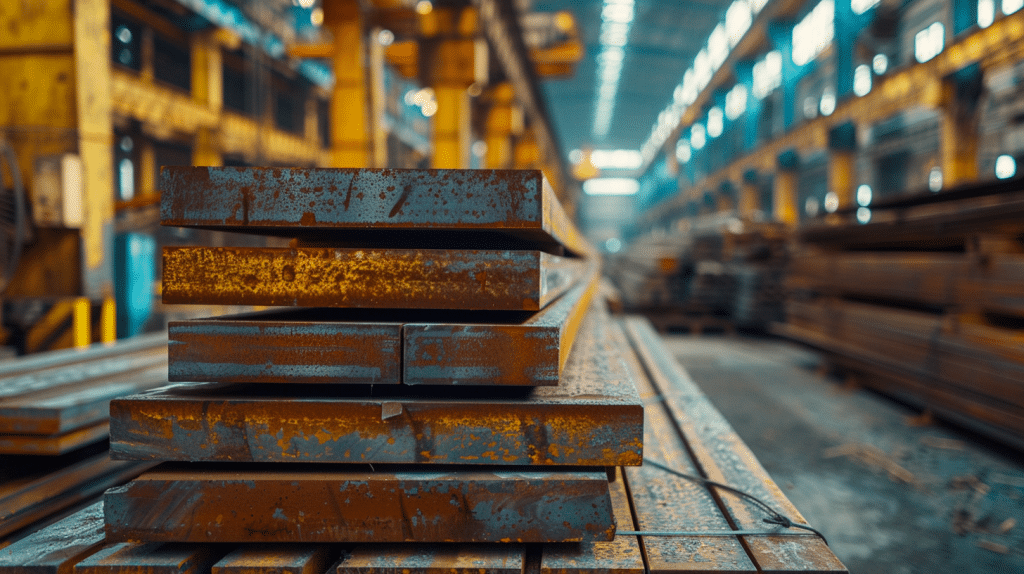
Hardness Comparative Analysis With Other Popular Tool Steels (Like D2, H13, And A2)
P20 steel is widely recognized for its balanced combination of hardness and machinability. It typically exhibits a lower hardness range in comparison to other tool steels, which can be an advantage depending on the application. The Rockwell Hardness (HRC) of P20 steel usually falls within the 28-32 HRC range.
D2 steel, known for its high wear resistance and hardness, often registers a higher Rockwell Hardness value, approximately between 55-62 HRC. This significant difference makes D2 a preferred option for applications requiring extreme durability and resistance to wear.
H13 steel is another frequently utilized tool steel, celebrated for its impressive heat resistance and toughness. Its hardness is somewhat moderate compared to D2 but higher than that of P20. You would typically find H13’s hardness in the range of 46-52 HRC. This characteristic makes it well-suited for hot work applications where thermal stresses are common.
A2 tool steel offers a balance between wear resistance and toughness. It usually shows a Rockwell Hardness value slightly above that of P20 but lower than both D2 and H13, generally around 57-62 HRC. This blend allows A2 to perform well in various applications requiring durable yet somewhat flexible tools.
Each tool steel has been engineered with specific properties and strengths in mind; thereby making direct comparisons can be misleading if not viewed through the lens of application-specific requirements. When selecting an appropriate tool steel, factors like working temperature conditions, desired wear resistance levels, machinability needs, and operational stress levels must all be taken into account alongside raw hardness values.
Tool Steel | Hardness (HRC) | Hardness (Vickers – HV) | Hardness (Brinell – HB) |
---|---|---|---|
P20 | 28-32 | 290-330 | 280-320 |
D2 | 55-62 | 610-750 | 600-740 |
H13 | 46-52 | 460-530 | 450-520 |
A2 | 57-62 | 610-740 | 600-730 |
Advantages Of P20 Steel In Terms Of Hardness And Machinability
P20 steel is renowned for its balance of hardness and machinability, making it a preferred choice in various tooling applications. This alloy, known for its impressive blend of properties, offers distinct advantages relevant to both these critical aspects.
The hardness of P20 steel plays a pivotal role in its application for mold making and other tooling requirements. Its ability to achieve a uniform hardness across the material enhances its wear resistance, prolonging the life of tools and molds made from it. This feature ensures that tools can withstand extended periods of usage without degrading in quality or performance.
On the aspect of machinability, P20 steel stands out due to its exceptional ease of machining. Despite its hardness, it can be shaped and modified with less wear on cutting tools, reducing downtime and maintenance costs associated with tool replacement. The alloy’s machinability also allows for intricate designs to be crafted with precision, ensuring that tight tolerances are met for complex parts.
Another advantage tied to the machinability of P20 steel is its minimal distortion during processing. Even after extensive machining or heat treatment processes, the dimensional stability of P20 steel remains intact. This characteristic is crucial in maintaining the accuracy and alignment of parts over time.
Regarding both hardness and machinability, P20 steel presents an optimal solution that supports efficient manufacturing processes while ensuring durability and precision. These attributes collectively make P20 steel a valuable resource in sectors requiring high-quality molds and dies such as automotive, consumer electronics, and plastic injection molding industries.
This comparative data elucidates P20 steel’s position on the scale of hardness relative to its counterparts. Its lower HRC range indicates a softer profile compared to D2 and A2 tool steels but offers superior machinability and weldability traits, making it desirable for certain tooling applications.
This compiled information aids in making informed decisions regarding material selection based on hardness criteria among other considerations like toughness, wear resistance, and machinability which are beyond the scope of this document but equally critical when assessing suitability for specific industrial uses.
Heat Treatment And Its Impact On P20 Steel Hardness
Heat treatment is a critical process in determining the final hardness and mechanical properties of P20 steel. This type of tool steel undergoes various heat treatment processes to achieve desired properties, including increased hardness, improved wear resistance, and enhanced durability. Understanding how these treatments impact the hardness of P20 steel is essential for selecting appropriate applications and ensuring optimal performance.
The primary heat treatment processes applied to P20 steel include annealing, quenching, and tempering. Annealing is conducted to relieve internal stresses, resulting in a more ductile material that’s easier to machine or weld. This process involves heating the steel to a specific temperature before slowly cooling it down, which can slightly reduce its overall hardness.
Quenching, on the other hand, significantly increases the hardness of P20 steel by rapidly cooling it from a high temperature. During quenching, the structure within the steel changes to form martensite, a much harder phase than the original one. However, this sudden increase in hardness can also make the steel brittle and more susceptible to cracking if not managed correctly.
Tempering is typically performed after quenching to strike a balance between hardness and toughness. By reheating quenched P20 steel to lower temperatures (below critical points), then cooling it at a controlled rate, tempering reduces brittleness while retaining much of the hardness gained from quenching. The exact temperature and time duration used during tempering can be adjusted based on the desired final properties of the P20 steel.
Additionally, stress relieving may be done post-tempering to minimize residual stresses without significantly affecting the material’s mechanical properties. This step ensures greater dimensional stability during machining or operational use.
The combination of these heat treatment processes directly influences the Rockwell Hardness (HRC) or Brinell Hardness Number (BHN) achievable for P20 tool steel. Though specific values may vary depending on precise heat treatment parameters and alloy composition, treated P20 steel typically exhibits an HRC range suitable for many tooling and mold-making applications.
Machinability and Weldability of P20 Steel
P20 steel is renowned for its exceptional machinability. This characteristic stems from its uniform hardness and the presence of sulfur, which acts as a machinability enhancing element. The uniform distribution of hardness across the material ensures a consistent performance in machining operations, reducing the risk of irregularities or defects in the finished product. As a result, P20 steel can be machined with relative ease compared to other tool steels, making it a preferred choice in manufacturing processes that require intricate detailing and precision.
The weldability of P20 steel also stands out as a significant advantage. Due to its unique chemical composition, P20 steel retains excellent stability during welding, minimizing the risks associated with cracking or distortion post-welding. This stability is particularly beneficial in applications where maintaining dimensional accuracy post-welding is paramount. Moreover, preheating and post-heating welding practices can further enhance the weld integrity, ensuring that welded joints exhibit strength and durability comparable to the base metal.
For welding purposes, it’s recommended to employ low hydrogen electrodes or TIG/MIG processes to achieve optimal results. Employing these methods helps in preventing potential welding complications such as porosity or inclusion formations within the weld joint. Additionally, given P20’s pre-hardened state, there are limited concerns about undergoing extensive heat treatment procedures post-welding to achieve desired hardness levels—a factor that simplifies manufacturing processes significantly.
In summary, P20 steel’s machinability and weldability are central to its extensive usage across various industries. Its capability to be easily machined into complex shapes and sizes without losing structural integrity coupled with superior weldable characteristics makes P20 an indispensable material in tool making and other precision-required applications. These qualities not only facilitate efficient production lines but also contribute toward cost-effectiveness by minimizing tool wear and maintenance requirements.
Applications Of High-Hardness P20 Steel
P20 steel, celebrated for its balanced hardness and machinability, finds widespread application in various industrial sectors. Its versatility stems from a blend of high hardness and other mechanical properties that make it ideal for crafting tools and molds subjected to stringent work conditions.
In the automotive industry, P20 steel is frequently chosen for manufacturing mold components vital for creating parts with precise dimensions and smooth finishes. Due to its resistance to wear and cracking, it ensures the longevity of molding equipment, which is crucial in high-production environments.
Within the plastic injection molding sector, this steel grade shines as a preferred material for mold bases. Its hardness level allows it to withstand the abrasive nature of certain plastics and repeated cycles of heating and cooling without compromising structural integrity. Consequently, manufacturers benefit from extended mold life and reduced downtime.
P20’s utility extends into die casting processes as well, especially where aluminum or zinc alloys are involved. Here, the steel’s properties effectively combat thermal fatigue and maintain dimensional stability under high temperatures – essential traits for producing intricate components with tight tolerances.
In addition to these applications, P20 tool steel holds significance in making punches, dies, holders, tooling fixtures, and kerner blocks. The combination of toughness with uniform hardness across large sections ensures tools perform reliably over time despite intense operational pressures.
Lastly, industries focused on creating prototype models also capitalize on P20’s characteristics. The ability to achieve a fine surface finish directly out of the machine reduces the need for extensive manual polishing. This saves considerable time in the product development phase where modifications may be frequent but fast turnarounds are critical.
Across these applications, P20 steel stands out not only due to its hardness but also because it enables efficient machining – shaping detailed parts without excessive wear on cutting tools. As such, industries relying on precision engineering continue to favor P20 for both its performance under stress and cost-effectiveness over prolonged use.
In Conclusion
P20 steel is widely recognized for its impressive blend of hardness, ductility, and toughness, making it a preferred choice for mold manufacturing in various industrial applications.
Discover more about how P20 steel can elevate the performance and durability of your projects by exploring our comprehensive range of materials. Connect with us today to discuss your specific needs and learn more about the innovative solutions we offer.