In the pantheon of versatile and widely used materials in engineering and metallurgy, 4140 alloy steel is a standout candidate due to its remarkable balance of strength, toughness, and versatility. This comprehensive guide aims to provide a thorough understanding of the properties, applications, and processing techniques that make 4140 alloy steel a go-to option for numerous industries.
What Is 4140 Alloy Steel?
4140 alloy steel is a chromium-molybdenum alloy steel that falls under the standard designation system for steels developed by the American Iron & Steel Institute (AISI). It is known for its outstanding toughness, high torsional strength, and good fatigue strength. The versatility of 4140 comes from its ability to be heat treated to a wide range of hardness and strength levels, which makes it suitable for a broad variety of applications.
As an alloy steel, 4140 contains a range of elements in specified amounts that enhance its mechanical properties. These elements include chromium, molybdenum, manganese, silicon, carbon, and small quantities of sulfur and phosphorus. The presence of these alloying elements provides better performance characteristics compared to carbon steel.
The “41” in the grade designation indicates that this material is a chrome-molybdenum or chromoly steel which has certain advantages such as corrosion resistance compared to other steels. This type of steel has found widespread use across various industries due to its mix of ductility, abrasion resistance, and toughness. Notably used in sectors requiring materials capable of withstanding excessive stress and strain without compromising integrity or performance, 4140 stands out as a reliable choice for engineers and manufacturers.
4140 Grade Designation
The grade designation of 4140 alloy steel is an identifier that reveals its main characteristics through a systematic numbering system used by the Society of Automotive Engineers (SAE) and the American Iron and Steel Institute (AISI). The numbers in 4140 indicate specific aspects of the steel’s classification:
- The first digit “4” indicates that this steel belongs to the molybdenum steel series. Molybdenum steels are known for their strength, hardness, and resistance to wear and impact.
- The second digit “1” designates the presence of secondary elements. In this case, “1” signifies that there is a secondary alloying element aside from carbon, which enhances certain characteristics such as tensile strength and heat treatability.
- The last two digits “40” specify the average carbon content present in the alloy. This value represents a carbon percentage of 0.40% by weight. The amount of carbon directly influences hardness after heat treatment as well as material properties like tensile strength and response during tempering.
Beneath is a representation of what each number stands for within the grade designation:
Number Position | Meaning | Specifics |
---|---|---|
First Digit | Series/Type of Alloy | 4 – Molybdenum steel series |
Second Digit | Secondary Alloying Element(s) | 1 – Indicates one secondary alloying element |
Last Two Digits | Average Carbon Content (multiplied by 100) | 40 – Represents 0.40% average carbon content |
What Are the Properties of 4140 Alloy Steel?
4140 alloy steel is renowned for its excellent balance of strength, toughness, and wear resistance. These properties stem from its specialized chemical makeup and treatment processes. Below is a breakdown that details the various attributes contributing to 4140 alloy steel’s performance in demanding applications.
Property | Details |
---|---|
Tensile Strength | High tensile strength enabling it to withstand significant stress. |
Toughness | Good toughness which allows it to endure sudden impacts without fracturing. |
Wear Resistance | Exceptional wear resistance due to its high chromium content. |
Hardness | It can achieve high hardness levels when heat treated correctly. |
Ductility | Moderate ductility, permitting some elongation during use. |
Impact Resistance | Capable of resisting impact at varying temperatures after proper heat treatment. |
Mechanical Properties of 4140 Steel
The mechanical properties of 4140 alloy steel are what make it highly sought after in various industries. These properties include tensile strength, yield strength, hardness, and elongation which directly affect the steel’s performance in applications. The wide acceptance of 4140 is due to its excellent hardness-to-toughness ratio, providing superior strength while maintaining a certain level of pliability.
Here is an overview of these key mechanical properties:
Property | Value |
---|---|
Tensile Strength | Typically ranges from 655 MPa to 950 MPa |
Yield Strength | Approximately 415 MPa to 655 MPa |
Hardness (Brinell) | Generally falls between 197 and 237 HBW |
Elongation | Around 25.7% in 50 mm |
Reduction of Area | Up to approximately 56.9% |
Charpy Impact (Typically tested at -29°C) | Varies but often around27 J |
Tensile strength refers to the maximum amount of tensile stress that the material can withstand before failure. This gives an indication of how much load the steel can handle under tension.
Yield strength measures the stress at which a definitive amount of plastic deformation (typically a permanent change in shape) occurs. A higher yield strength means the material can return to its original shape after being stressed up to that point.
Hardness defines resistance to indentation and wear. It is measured using the Brinell scale for steels like 4140, which have a medium hardness range. Elongation measures how much the material will deform lengthwise before fracturing and is expressed as a percentage.
Lastly, it’s noteworthy that although possessing commendable tensile and yield strengths suitable for many engineering applications, when tempered or heat treated correctly, these values can significantly increase—underscoring why understanding heat treatment processes is essential for leveraging this material’s full potential for specific uses.
In applications where materials must resist impact or sudden loads, such as gears and crankshafts in automotive uses, toughness testing like Charpy impact becomes quite relevant. The measure represents how much energy a material sample absorbs during fracture at high-speeds ensuring its aptitude for areas where physical impacts occur.
What Is the Chemical Composition of 4140 Alloy Steel?
The chemical composition of 4140 alloy steel is a critical aspect that defines its characteristics and suitability for various applications. Below is the typical chemical composition of 4140 alloy steel:
Element | Percentage (%) |
---|---|
Carbon (C) | 0.38 – 0.43 |
Silicon (Si) | 0.15 – 0.35 |
Manganese (Mn) | 0.75 – 1.00 |
Chromium (Cr) | 0.80 – 1.10 |
Molybdenum (Mo) | 0.15 – 0.25 |
Sulfur (S) | Max 0.040 |
Phosphorus (P) | Max 0.035 |
It’s important to note that while these values are typical, they may slightly vary depending on the manufacturer or specific grade requirements.
- Carbon:
- Increases hardness and strength.
- Decreases ductility and impact resistance.
- Requires careful balance for intended use cases.
- Silicon:
- Added as a deoxidizing agent.
- Contributes to increased strength without affecting ductility adversely.
- Manganese:
- Enhances the depth of hardening.
- Improves hot working properties.
- Chromium:
- Increases response to heat treatment.
- Elevates high-temperature strength.
- Improves hardenability and abrasion resistance.
- Molybdenum:
- Increases toughness and strength.
- Improves hardenability, allowing oil quenching in thicker sections.
- Sulfur and phosphorus:
- Kept at minimal levels.
- Higher concentrations can lead to embrittlement and negatively affect desirable properties.

What Is the Carbon Content of 4140 Alloy Steel?
The carbon content of 4140 alloy steel is one of its critical defining factors, contributing substantially to the material’s hardness and strength characteristics. Typically, the carbon percentage in 4140 steel ranges between 0.38% to 0.43%. This proportion places it within the medium-carbon category of steels, balancing ductility and strength effectively. It is essential to maintain this specific range as variations can lead to significant changes in the steel’s properties, affecting its suitability for various applications.
Element | Carbon (C) |
---|---|
Content | 0.38-0.43% |
Understanding the carbon content is pivotal for metallurgists and engineers when selecting a steel grade for a particular application, as it directly influences attributes such as tensile strength, wear resistance, and ability to undergo heat treatment processes successfully. Higher carbon contents can lead to increased hardness after quenching and tempering but may also reduce weldability and increase brittleness; thus, striking a balance is key. The carbon percentage in 4140 alloy steel has been optimized for a comprehensive range of industrial applications requiring both strength and toughness.
Pros of 4140 Alloy Steel
Advantages | Description |
---|---|
Excellent Strength-to-Weight Ratio | Enables the design of lighter, high-strength components, particularly in aerospace and automotive industries. |
High Surface Hardness Through Heat Treatment | Achieves high surface hardness, enhancing wear resistance, making it ideal for gear and engine parts. |
Exceptional Impact Resistance | Demonstrates exceptional impact resistance, even at low temperatures, suitable for applications requiring resistance to sudden stress or impact. |
Good Machinability | Has good machinability compared to other alloy steels, facilitating efficient manufacturing processes. |
Weldability | Fair weldability, but can weld well with proper preparation without compromising structural integrity post-welding. |
Corrosion Resistance | Offers better corrosion resistance than many low-alloy steels due to its chromium content. May require additional coatings or treatments for extreme conditions. |
Versatility in Forms | Available in various forms such as bars, plates, flat sheets, and forgings, adaptable to diverse industries and design requirements. |
Cons of 4140 Alloy Steel
Disadvantages | Explanation |
---|---|
Hardness Trade-off | Achieving high hardness reduces toughness, making it less suitable for applications requiring both properties evenly balanced. |
Machinability | Although better than many other alloys, machining 4140 can still be challenging in its hardened state and may require specialized tools. |
Weldability Concerns | Preheat and post-weld heat treatment processes are essential due to the risk of cracking during welding; this complicates the fabrication process. |
Distortion During Heat Treatment | If not properly controlled, heat treatment can lead to dimensional changes or distortions in components made from 4140 steel. |
Susceptibility to Corrosion | Without protective coatings or treatments, 4140 is prone to rusting, which limits its use in corrosive environments. |
Cost Factor | Depending on market availability and demand, alloy steels like 4140 can be more expensive than plain carbon steels due to their enhanced properties. |
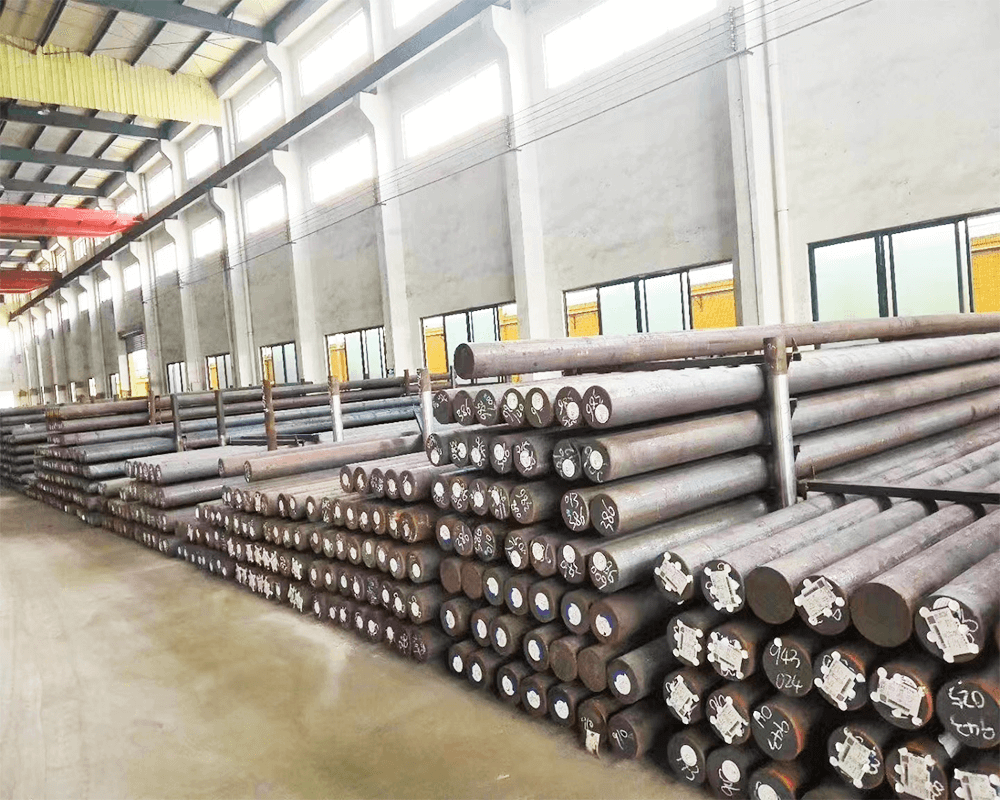
What Is 4140 Alloy Steel Used For?
Due to its impressive combination of strength, toughness, and wear resistance, 4140 alloy steel is extensively used across various industries.
Industry | Applications |
---|---|
Automotive | Gears, crankshafts, spindles, fixtures |
Aerospace | Landing gear components, structural parts |
Oil and Gas | Drill collars, valves, fittings |
Agriculture | Machinery parts subjected to stress |
Military | Vehicle armor plates |
Tool Making | Forging dies, hammers |
In the automotive realm, engineers favor 4140 for its excellent fatigue strength and high-impact toughness; it’s ideal for crafting high-stress parts like gears and crankshafts that require both durability and responsiveness under duress. The aerospace sector appreciates 4140’s reliable performance in landing gear assemblies and other structural components where failure is not an option.
In oil and gas exploration and production environments where components like drill collars undergo severe stress cycles while ensuring operational integrity is paramount, the resilience provided by 4140 alloy steel makes it a standard choice. Moreover, this alloy proves trustworthy in agricultural machinery due to its ability to withstand the rigorous demands of farming equipment which often deal with variable loads.
The military industry seeks out materials offering maximum protection with minimum weight burden—4140’s characteristics make it suitable for manufacturing vehicle armor plates keeping soldiers safe without encumbering vehicles’ mobility.
When it comes to creating tools that repeatedly strike or shape metal workpieces—like forging dies—machinists rely on 4140 because of its ability to absorb repetitive shocks without deforming or cracking.
With these diverse uses illustrating just a few instances of its applicability, 4140 alloy steel demonstrates itself as an exceptional material wielding broad practicality across many spheres of human endeavor.
How Is 4140 Alloy Steel Made?
The production of 4140 alloy steel involves a series of steps that transform raw materials into the high-grade steel known for its excellent characteristics. Below is an overview of the typical manufacturing process:
Step | Description |
---|---|
1. Iron Ore Processing | To begin, iron ore is reduced in a blast furnace to produce pig iron, the basic raw material required for steel production. |
2. Combining Elements | The pig iron is then combined with scrap iron, and other elements including carbon, chromium, manganese, and molybdenum are added to create the specific chemical composition desired for 4140 alloy steel. |
3. Melting and Refining | These materials are melted together in an electric arc furnace (EAF) or a basic oxygen furnace (BOF). Following melting, the metal undergoes refinements to remove impurities and adjust its chemical composition accurately. |
4. Casting | The purified molten metal is then cast into long slabs or blooms through continuous casting or ingot casting methods. |
5. Primary Forming | While still hot, these slabs or blooms are passed through rollers to obtain specific shapes like bars, rods or sheets during primary forming processes such as hot rolling. |
6. Heat Treatment | After initial forming steps, heat treatment processes such as quenching and tempering are applied to achieve the desired mechanical properties of strength and toughness in 4140 steel. |
7. Secondary Forming and Finishing | Depending on the final product requirements, secondary processes may include cold rolling or drawing through dies to refine dimensions further and improve surface finish. |
8. Inspection and Testing | Throughout this process, rigorous inspection takes place to ensure quality standards are met at every stage before it leaves the manufacturing facility. |
Machinability Rating of 4140 Alloy Steel
The machinability rating of 4140 alloy steel reflects how easily it can be cut into a desired final shape and size, a crucial aspect in manufacturing processes. This value is indicative of the ease with which the material can be drilled, milled, turned on a lathe, or ground without compromising its integrity.
Typically, the machining industry uses comparatives index numbers to rate materials; with 100% being the baseline set against a free-cutting carbon steel (1212 grade).
Material | Machinability Rating (%) |
---|---|
1212 Carbon Steel (Baseline) | 100 |
4140 Alloy Steel | 65 – 70 |
4140 alloy steel generally has a machinability rating in the range of approximately 65 to 70 percent when annealed. This rating means that it’s relatively more challenging to machine than softer steels but more manageable compared to some harder steel alloys.
This property is afforded by its composition that balances high hardness for wear resistance while maintaining adequate toughness. The actual machinability can vary within this range depending on the heat treatment applied to the steel—pre-hardened forms may present different characteristics than those that are annealed.
When machining this material, proper tools must be selected including carbide-tipped or other high-speed cutting instruments designed for harder materials; otherwise, there could be excessive wear or tool breakage due to contact with the tough surface. Additionally, coolants or lubricants are often employed during machining operations to reduce tool wear and manage heat generated from metal-on-metal contact.
Thermal Properties of 4140 Alloy Steel
The thermal properties of 4140 alloy steel determine its behavior and stability under thermal stresses and environmental temperature changes. These characteristics are crucial for engineers and metallurgists when planning the heating and cooling processes during production, as well as predicting performance in applications where temperatures may fluctuate.
A key aspect of these properties is the coefficient of thermal expansion, which describes how the material expands when heated and contracts when cooled. For 4140 alloy steel, this coefficient varies depending on the temperature range. At room temperature up to about 500°F (260°C), the coefficient is approximately 6.78 x 10^-6 per °F (12.2 x 10^-6 per °C). This rate increases slightly at higher temperatures.
Another significant thermal property is the material’s thermal conductivity, which measures its ability to conduct heat through its body. This also varies with temperature but it averages around 42.6 W/(m·K) at a room temperature that is around 68°F (20°C).
The specific heat capacity, which quantifies how much energy it takes to raise the unit mass of a material by one degree in temperature, for 4140 steel is approximately 0.114 BTU/lb°F (0.475 kJ/kg°C).
Combining these elements gives us a brief overview of how the material will react in various thermal scenarios:
Property | Value at Room Temperature |
---|---|
Coefficient of Thermal Expansion | ~6.78 x 10^-6 /°F (12.2 x 10^-6 /°C) |
Thermal Conductivity | ~42.6 W/(m·K) |
Specific Heat Capacity | ~0.114 BTU/lb°F (0.475 kJ/kg°C) |
Such properties are essential when considering heat treatment processes like quenching or tempering and can critically influence manufacturing methods like welding, as well as performance in thermally variable environments such as automotive or aerospace applications where metals often undergo rapid and repeated heating and cooling cycles.
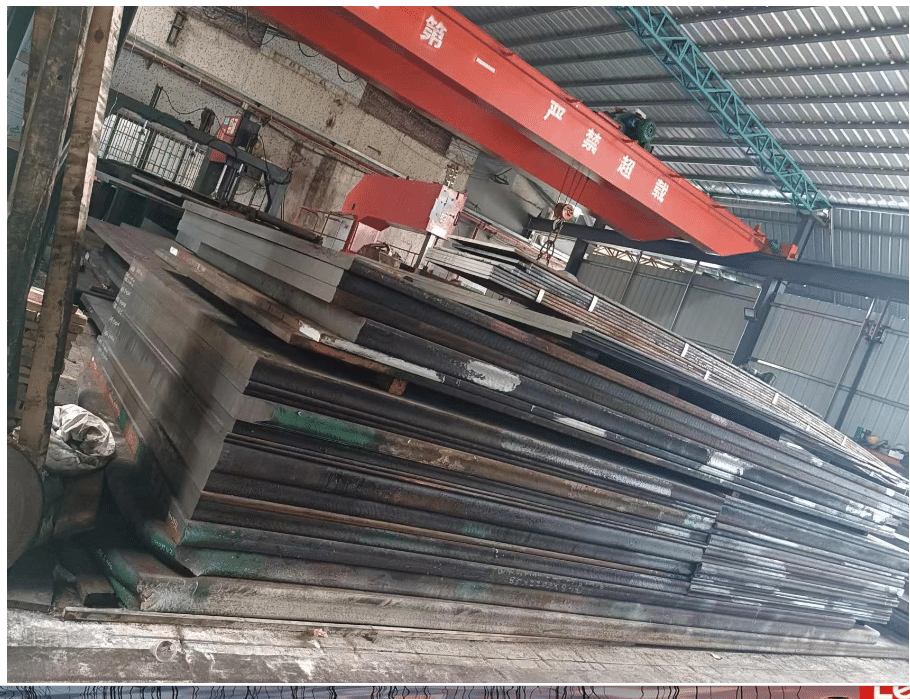
What Are Equivalents of 4140 Alloy Steel?
4140 alloy steel is recognized for its versatility and excellent balance of strength, toughness, and abrasion resistance. Its numerous equivalents worldwide follow various standards, allowing for international accessibility and substitutability in many sectors, including automotive, oil and gas, and engineering applications. Below is a table displaying some common global equivalents of 4140 alloy steel:
Standard | Country | Equivalent Grade |
---|---|---|
AISI/SAE | United States | 4140 |
EN | Europe | 42CrMo4 (1.7225) |
JIS | Japan | SCM440 |
DIN | Germany | 42CrMo4/1.7225 |
BS | United Kingdom | 708M40 |
GOST | Russia | 38XM |
What Are the Common Forms of 4140 Alloy Steel Material?
4140 alloy steel is available in a variety of forms to suit different applications and manufacturing processes. Each form provides specific advantages, lending itself well for particular uses based on shape, size, and fabrication requirements. The common forms of 4140 material include:
Form | Description |
---|---|
Round Bar | A long, cylindrical metal bar stock that has many industrial and commercial applications. Typically used in gears, spindles, fixtures, and collars. |
Flat Bar | A flattened long strip of metal used where a precise shape and tolerances are not critical but toughness is necessary. Commonly applied in parts such as connecting rods or brackets. |
Square Bar | Shaped like a square and often used for fittings, keys, machine parts, and structural components. |
Plate | A flat piece of steel with greater thickness than sheet; utilized in automotive gears and clutches as well as heavy machinery components. |
Sheet | Thinner than plate steel, sheets are used where corrosion resistance is needed more than bulk strength or hardness. |
Tube/Round Tube | Available in different sizes for use in mechanical applications where lighter weight and better corrosion resistance are required alongside high strength. |
Each of these material forms can be further processed – cut to size, forged into shapes, rolled into rings – providing flexibility in design for engineers and fabricators when working with 4140 alloy steel. Whether the requirement calls for resistance to stress or large loads at lower temperatures or excellent toughness at high temperatures, the diverse range of available forms ensures there’s an appropriate version of 4140 alloy steel to meet those specific needs.
The Difference Between 4140 Alloy Steel and 8620 Steel
Both steels are part of the low-alloy family, which means they contain various elements including chromium, molybdenum, and nickel, but in different proportions.
Property | 4140 Alloy Steel | 8620 Steel |
---|---|---|
Chemical Composition | Approx. 0.40% carbon, 1% chromium, 0.2% molybdenum | Approx. 0.20% carbon, 0.5% chromium, 0.7% nickel, 0.2% molybdenum |
Carbon Content | Higher | Lower |
Core Hardness (after hardening & tempering) | High | Medium |
Tensile Strength | Higher (potentially over 130 KSI) | Lower (~90 KSI typical) |
Toughness | Good | Better due to lower hardness |
Wear Resistance | Excellent | Good |
Core Applications | Shafts, gears, forgings | Gears, camshafts, fasteners |
Both steels undergo a heat treatment process to achieve desired mechanical properties; however, due to its higher carbon content and overall alloying elements that contribute to hardenability, the heat-treated condition of 4140 yields a much tougher and stronger product compared to that of the nickel-rich 8620 steel.
In machining aspects, while both have good machinability for a high-strength alloy steel, with proper tooling setups and speeds-and-feeds parameters accounted for their individual characteristics.
In essence:
- 4140: Offers a balance of strength, toughness, and wear resistance at a higher level due to elevated carbon content.
- 8620: Provides good core strength with an outer ductile layer thanks to case-hardening processes facilitating superior toughness for impact-prone applications.
What Is the Difference Between 4140 Alloy Steel and 1045 Steel?
4140 alloy steel and 1045 steel are both iron alloys, with various differences concerning their composition, mechanical properties, and applications. The primary points of distinctions between these two materials can be summarized in the table below.
Criterion | 4140 Alloy Steel | 1045 Steel |
---|---|---|
Carbon Content | Medium carbon content (Approx. 0.40%) | Medium carbon content (Approx. 0.45%) |
Chromium & Molybdenum | Yes (Chromium around 1% and Molybdenum around 0.20-0.25%) | No |
Hardness | Higher due to alloying elements | Lower compared to 4140 |
Tensile Strength | Higher tensile strength | Lower tensile strength |
Impact Resistance | Better impact resistance; responds well to heat treatment | Poorer impact resistance |
Weldability | Moderate; requires pre and post-weld heat treatment | Good without additional preparations |
Applications | Gears, axles, shafts for higher stress applications | Machine parts not subjected to severe stresses |
Despite having similar carbon contents—4140 slightly less than 1045—the presence of chromium and molybdenum in the former makes it significantly different when measuring toughness, wear resistance, and fatigue strength. These added elements dramatically enhance its ability to withstand stress and resist abrasion which is crucial in dynamic applications that require durability alongside mechanical performance.
What Is the Difference Between 4140 Alloy Steel and 4130 Steel?
Characteristic | 4130 Alloy Steel | 4140 Alloy Steel |
---|---|---|
Chemical Composition | Lower carbon content (around 0.30%) | Higher carbon content (approximately 0.40%) |
Strength and Hardness | Lower strength and hardness compared to 4140 | Higher strength and hardness compared to 4130 |
Ductility | Higher ductility due to lower carbon content | Lower ductility due to higher carbon content |
Response to Heat Treatment | Good response to heat treatment but not as through-hardening as 4140 | Better through-hardening capability |
Weldability | Favorable for welding due to lower carbon content, less susceptible to weld cracking | Still weldable but may require more attention to welding process |
Typical Applications | Welded structures with high impact toughness requirements, aircraft engine mounts, welded tubing | Shafts, gears, bolts, tooling bars, applications demanding higher mechanical performance and durability |
While both alloy steels offer advantages such as good atmospheric corrosion resistance and retention of toughness at low temperatures, the broader hardenability of 4140 makes it preferable when strength is a primary consideration over weldability. Meanwhile, industries requiring intricate welding tend to lean towards using more easily welded yet still robustly resistant materials such as grade 4130 alloy steel.
In conclusion
4140 alloy steel stands as a remarkable engineering material, offering an exceptional balance of toughness, strength, and versatility. Its wide range of applications in industries such as aerospace, automotive, and manufacturing is a testament to its reliability and performance under demanding conditions.
Understanding the nuances of this alloy—from its chemical composition to heat treatment processes—is crucial for any business that seeks to leverage its properties for competitive advantage. Whether you’re embarking on a new project or optimizing an existing one, the correct implementation of 4140 alloy steel can be a game-changer.
We invite you to explore the full potential of 4140 alloy steel with our expertise guiding you every step of the way. Our website offers extensive resources and detailed insights into advanced steel solutions tailored for your unique applications. For personalized assistance or to answer any questions about how 4140 alloy steel can benefit your operations, please don’t hesitate to reach out.