Navigating the complex world of steel materials can be a daunting task, with various types and grades each presenting unique properties and applications. Among the most commonly used are alloy steel and carbon steel—two categories that, while similar in some aspects, possess distinct differences crucial for engineers, designers, and fabricators to understand. This article delves into the intricacies of alloy steel versus carbon steel, elucidating their composition, mechanical properties, and typical uses. Join us as we unravel these two stalwarts of the steel industry to help you make informed decisions for your next project.
What is Alloy Steel?
Alloy steel is a category of steel that has been enhanced with the addition of various alloying elements to improve its mechanical properties. These elements, which include metals such as chromium, nickel, vanadium, and molybdenum, as well as non-metals like silicon and phosphorus, are added in different proportions to the iron and carbon base that makes up traditional steel. The composition of alloy steels ranges widely depending on the specific elements used and their concentrations.
The primary objective behind the creation of alloy steels is to amplify certain desirable qualities within the material such as strength, hardness, toughness, wear resistance, corrosion resistance, or hot hardness. Each element contributes distinct characteristics: for instance, chromium increases hardness and tensile strength while also improving corrosion resistance; nickel adds toughness; vanadium enhances shock resistance; and molybdenum can increase strength at high temperatures.
What Are the Properties of Alloy Steel?
Alloy steel is distinguished by its significant variety of mechanical and physical properties, which can be tailored according to the addition of various alloying elements. The blend of alloying components such as chromium, nickel, manganese, and vanadium with base iron and carbon imparts distinctive characteristics to the steel that are not found in traditional carbon steels.
Property | Description |
---|---|
Tensile Strength | Alloy steels have higher tensile strength due to the presence of other materials. |
Hardness | Increased hardness can be achieved with certain alloys for better wear resistance. |
Toughness | Improved toughness helps in resisting fractures and cracks during stress. |
Ductility | Certain alloys maintain or enhance ductility, allowing deformation without fracture. |
Corrosion Resistance | Elements like chromium provide resistance to rust and corrosion. |
Wear Resistance | Enhanced resistance to surface wear for applications such as tools and parts. |
These properties make alloy steel adaptable for use in a wide range of applications where specific mechanical attributes are required. For example, altering the quantities of manganese can improve hardness which is favorable for construction materials, while chromium increases corrosion resistance desirable for use in harsh environments.
Each element contributes uniquely: Nickel can increase toughness; molybdenum can assist in maintaining strength at high temperatures; while vanadium often enhances hardness and makes it suitable for cutting tools.
It’s also noteworthy that these properties come with varying degrees of formability and weldability, depending if the alloys lead to a ferritic, austenitic or martensitic microstructure after heat treatment. Some types allow easier shaping or joining processes, while others may necessitate specific techniques due to increased strength or reduced ductility.
What Are the Types of Alloy Steel?
Alloy steel is primarily categorized into two groups based on the presence and concentration of various alloying elements: low-alloy steels and high-alloy steels. Each type possesses distinct characteristics which determine its suitability for specific applications.
Low-Alloy Steels
These typically contain less than 8% alloying elements and are known for their enhanced mechanical properties compared to carbon steel. The addition of elements like chromium, nickel, molybdenum, vanadium, or manganese in small quantities improves hardness, tensile strength, corrosion resistance, and ability to withstand impact. Low-alloy steels are often used where weight reduction and strength are critical.
Element | Percentage |
---|---|
Chromium | ≤ 3% |
Nickel | ≤ 3% |
Molybdenum | ≤ 1% |
Vanadium | ≤ 0.5% |
Manganese | ≤ 2% |
High-Alloy Steels
In contrast to low-alloy variants, high-alloy steels have greater than 8% alloy content. They can exhibit enhanced corrosion resistance and can be created with very specific properties for specialized applications. Stainless steels form a significant part of this category due to their substantial chromium content that imparts remarkable resistance to oxidation and corrosion.
Element | Percentage |
---|---|
Chromium | ≥ 10-20% |
Nickel | Variable |
Molybdenum | Variable |
Within these two primary categories lies a multitude of subcategories defined by the specific alloying element combinations which optimize the material for different environment stresses such as heat tolerance or abrasion resistance:
- Chromium-Molybdenum (Cr-Mo) Steels: Especially strong and often used in the oil and gas industries.
- Nickel-Chromium (Ni-Cr) Steels: Known for toughness at low temperatures.
- Manganese Steels: Noted for their impact strength and wear-resistance.
- Silicon-Manganese (Si-Mn) Steels: Offer additional spring-like qualities.
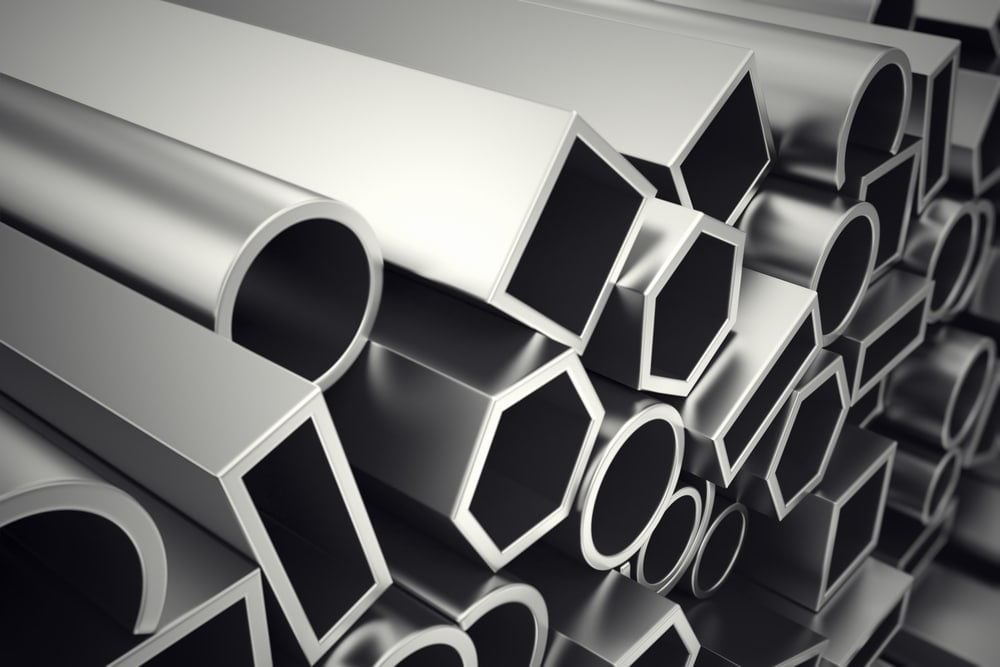
Common Applications of Alloy Steel
In the diverse world of material science, alloy steel stands out for its extensive use across various industries due to its adaptable characteristics. The applications of alloy steel are numerous and vary greatly depending on the combination of elements used in its creation, which impart different properties to the final product. Below is a representation, albeit not exhaustive, of where you might find alloy steel in everyday life as well as in specialized sectors:
Industry/Application Area | Examples |
---|---|
Automotive Manufacturing | Gears, axles, crankshafts, and chassis components made from alloy steels achieve the necessary strength and toughness. |
Aerospace | Requirements for light weight without compromising on durability make alloy steels suitable for components such as jet turbine engines and spacecraft hulls. |
Construction | Beams, plates, rebars and other supportive structures benefit from high-strength low-alloy (HSLA) steels, designed to withstand heavy loads and adverse conditions. |
Energy Sector | Power plants rely on alloy steel pipes that can handle high temperature and pressure; also used for oil rigs and in renewable energy infrastructure like wind turbines. |
Rail Transport | Rails made from alloy steels resist wear and deformation; likewise bogies and couplings employ these materials for their resilience under stress. |
Tooling | High speed steels (a subset of tool steels), those containing tungsten or molybdenum, are valued in production of drills, saw blades, and milling cutters. |
Military & Defense | Armored vehicles prioritize hardened alloys for protection while maintaining manoeuvrability; firearms benefit from specific wear-resistant alloys in barrels and actions. |
What is Carbon Steel?
Carbon steel is an iron-carbon alloy with a carbon content of up to 2.1% by weight, making it one of the most widely used steel types. As a fundamental form of steel, it can be categorized based on its carbon content: low, medium, and high. Low-carbon steel contains less than 0.3% carbon, medium-carbon steel has approximately 0.3% to 0.6%, and high-carbon steel typically ranges from 0.6% to 1%. An even higher carbon content may lead to what’s known as ultra-high carbon steel, with up to 2.1% carbon.
The influence of its predominant element—carbon—deeply affects the material’s mechanical properties, such as its hardness and tensile strength. The proportion of carbon plays a crucial role in determining how the metal behaves under heat treatment and thus, its final application.
Despite the term “alloy” being generally associated with a mixture of elements, in the context of metallurgy, even carbon steels are considered alloys due to their iron and carbon composition combined with trace amounts of other elements that are inherently present or added for desired properties.
Although additional elements such as manganese are commonly found within carbon steel, their levels are typically regulated so that they do not exceed certain percentages to maintain characteristic qualities attributed specifically to pure or nearly-pure carbide compositions.
Carbon steel’s simplicity in composition makes it a foundational material for various industries due to its relative affordability and readiness for use in diverse manufacturing contexts without requiring significant quantities of costly alloying materials—a notable distinction from its more complex alloyed counterparts.
What Are the Properties of Carbon Steel?
Carbon steel, as its name suggests, is a type of steel where the main alloying element is carbon. Its properties are primarily determined by the amount of carbon it contains, which impacts its strength, ductility, and hardness. In table form, the essential properties of carbon steel can be delineated as follows:
Property | Description |
---|---|
Tensile Strength | Higher carbon content increases tensile strength. |
Ductility | Generally decreases as carbon content increases. |
Hardness | Increases with higher carbon levels; less hard than many alloy steels. |
Machinability | Good machinability in lower carbon steels; can become problematic as carbon content rises due to increased hardness. |
Weldability | Better for low-carbon steels; diminishes with increasing carbon content due to risk of cracking. |
Impact Resistance | Reduces with higher carbon content; improved upon by tempering processes at low temperatures. |
These properties result from different concentrations of carbon within three subspecies (low, medium, and high), affecting their performance and suitability for various applications.
Low-carbon steel tends to be soft and pliable but lacks strong structural integrity compared to higher-carbon variants. Conversely, high-carbon steel is quite hard and resistant to abrasion but becomes brittle and less ductile—qualities that might impede certain manufacturing processes or render them unsuitable for particular purposes without secondary treatments such as annealing.
Carbon’s influence on steel reaches into microscopic characteristics: it affects grain size and shape within the metal matrix; these crystalline structures contribute decisively to overall mechanical behaviors observed in different kinds of carbon steels.
What Are the Types of Carbon Steel?
Carbon steel, an alloy composed primarily of iron and carbon, is classified into three main categories based on its carbon content and other alloying elements. These types determine the steel’s properties, making each suited for specific applications.
- Low Carbon Steel (Mild Steel):
- Carbon Content: Up to 0.30%
- Characteristics: High ductility, excellent weldability, good machinability
- Applications: Construction materials, automotive body parts, pipes
- Medium Carbon Steel:
- Carbon Content: 0.30-0.60%
- Characteristics: Balances ductility and strength; good wear resistance
- Applications: Railroad tracks, gears, structural components
- High Carbon Steel:
- Carbon Content: 0.60-1.25%
- Characteristics: High strength, high hardness; less ductility
- Applications: Cutting tools (knives), springs, high-strength wires
The differing carbon content significantly affects each type’s behavior under various conditions such as heat treatment or when subjected to mechanical stresses. Lower carbon steels are usually easier to form and shape while higher carbon variants can be hardened more effectively offering superior wear resistance but at the cost of reduced flexibility and increased brittleness. The choice among these types thus depends on the balance between hardness and toughness required in the end use of the material.
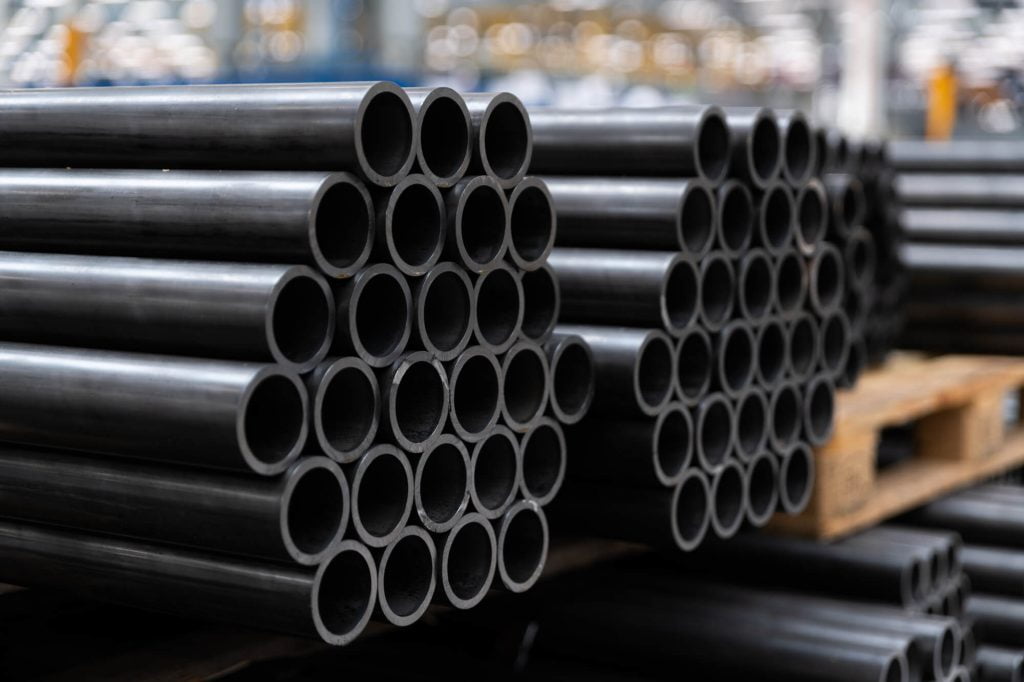
Common Applications of Carbon Steel
Carbon steel, with its versatility and wide range of properties, is utilized in numerous industries and for a myriad of applications. Its ability to be forged into strong products makes it a popular choice where strength and durability are paramount. Owing to the variations in carbon content, ranging from mild to ultra-high carbon steels, the applications can vary significantly. Here’s an overview of the common uses segmented by industry:
Industry | Common Applications of Carbon Steel |
---|---|
Construction | Beams, Rebar, Pipes, Bolts, Nails |
Manufacturing | Machinery parts, Automotive components, Tools |
Energy | Oil and gas pipelines, Wind turbine towers |
Transportation | Railroad tracks, Shipbuilding |
Consumer Goods | Kitchen appliances, Cutlery |
Carbon steel remains a cornerstone material across diverse sectors due to its varied grades offering different properties that cater effectively to specific application requirements.
Advantages of Alloy Steel Compared to Carbon Steel
Alloy steel offers several distinctive advantages over carbon steel, which stem primarily from the addition of various alloying elements that enhance its performance:
Advantage | Description |
---|---|
Enhanced Strength | Alloy steels often have a higher strength due to the presence of elements like manganese and nickel. |
Improved Hardness | These steels can achieve greater hardness, which is essential in wear resistance for tools and machinery. |
Increased Durability | The added toughness provided by alloying elements helps prevent fractures and increases lifespan under stress. |
Better Corrosion Resistance | Elements such as chromium provide an increased resistance to corrosion and oxidation. |
Versatility in Applications | Due to their properties, alloy steels are suitable for various applications including aerospace, automotive, and construction. |
Elevated Tensile Strength | Alloying enables these steels to withstand greater forces before deforming or breaking. |
Enhanced Thermal Conductivity | Certain alloy steels conduct heat more efficiently, benefiting high-temperature processes. |
These advantages demonstrate how strategically adding certain elements to steel can significantly broaden its application range and improve its performance in demanding situations. Companies seeking steel with specific characteristics often turn to alloy steel varieties tailor-made for particular environments or stresses where typical carbon steel might not suffice.
Disadvantages of Alloy Steel Compared to Carbon Steel
Alloy steel, while boasting a range of enhanced properties, presents certain disadvantages when compared to carbon steel. Below is a detailed comparison outlining these shortcomings.
Disadvantage | Description |
---|---|
Cost | Alloy steel typically costs more than carbon steel due to the addition of various alloying elements and the complex processing required to produce these specialized materials. |
Machinability | Higher alloy content can make machining more difficult compared to the relative ease with which carbon steels can be machined. This can also result in higher tool wear and maintenance costs. |
Weldability | The presence of alloys such as chromium and nickel can complicate welding processes for alloy steels when compared to plain carbon steels, often requiring specialized procedures. |
Heat Treatment Complexity | Alloy steels usually require more complex heat treatments for achieving desired mechanical properties, hence increasing production time and cost. |
Comparisons Between Alloy Steel and Carbon Steel
When examining the differences between alloy steel and carbon steel, various characteristics must be considered:
Aspect | Alloy Steel | Carbon Steel |
---|---|---|
Strength | Enhanced by additional alloying elements. | Generally strong but less than alloy steel. |
Versatility | High due to varied alloys for specific needs. | Less versatile; few compositional variations. |
Durability | Improved resistance to wear and corrosion. | Good durability but prone to rust. |
Processing Requirements | Often requires more complex heat treatment. | Easier to work with due to simpler composition. |
Hardness | Can be extremely hard depending on alloys used. | Hard but may require treatments for higher hardness levels. |
Cost | Typically more expensive due to alloying materials. | Less expensive; involves lower material costs. |
Thermal Conductivity | Lower compared to carbon steel due to alloying elements. | Higher which makes it better for applications requiring heat dissipation. |
Tensile Strength | Generally higher, benefiting from added alloys. | Depends on the carbon content; can vary significantly. |
Applications | Aerospace, automotive, energy sector, etc. | Structural applications, tools, machinery parts, etc. |
The amalgamation of these characteristics presents a composite understanding of how alloy steels compare against their carbon counterparts in diverse respects such as mechanical strength and economic considerations like cost efficiency.
In scenarios prioritizing higher strength or environmental resistances—like exposure to corrosive elements or extreme wear—alloy steel stands out as a superior choice owing its robust material properties influenced by the incorporation of various alloys.
On the other hand, when simplicity in processing or cost-effectiveness is paramount — especially in projects that do not demand the heightened performance attributes of alloys — carbon steel serves as an apt selection due primarily to its straightforward composition and relative affordability.
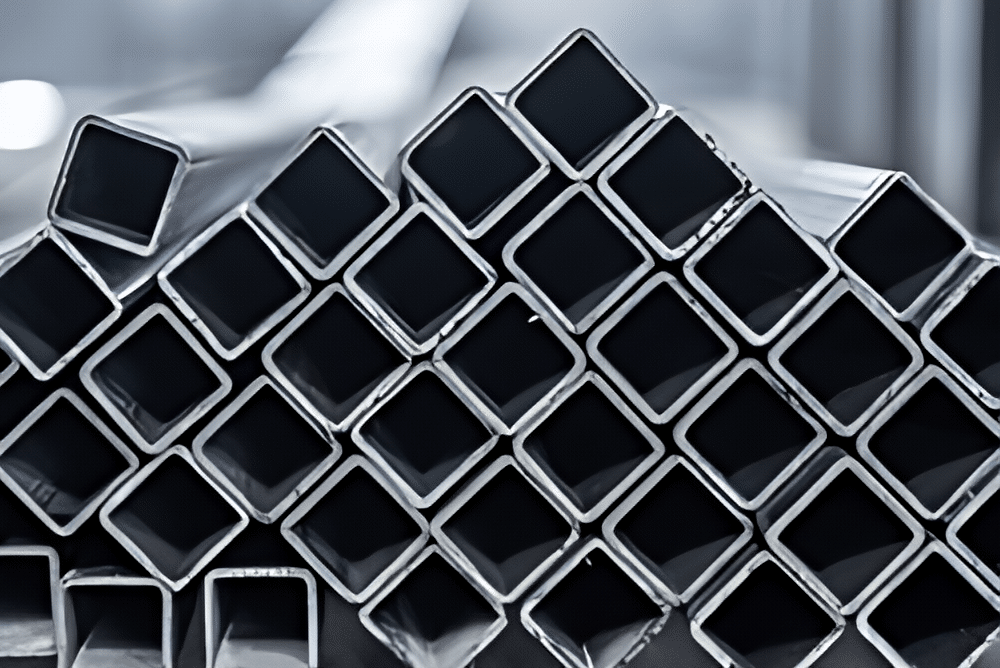
Mutual Alternatives to Alloy Steel and Carbon Steel
In the materials industry, both alloy steel and carbon steel have their distinct uses. However, there’s a necessity for alternatives that can offer characteristics of both or address specific engineering requirements beyond what these steels can provide. Below is an overview of some mutual alternatives to alloy steel and carbon steel, outlining their unique attributes that serve as replacements in certain applications.
Alternative Material | Description | Key Properties | Typical Applications |
---|---|---|---|
Stainless Steel | A group of iron-based alloys containing at least 10.5% chromium, offering enhanced corrosion resistance. | Corrosion resistance, formability, strength. | Kitchen equipment, medical devices, architectural structures. |
Tool Steel | A type of carbon and alloy steel that is particularly well-suited for making tools due to its hardness, resistance to abrasion, and ability to retain shape at high temperatures. | Hardness, abrasion resistance, heat resistance. | Cutting tools, molds for casting metals/plastics. |
Titanium | A low-density element with strong corrosive-resistant properties thanks to a protective oxide layer that forms in air. | High strength-to-weight ratio, corrosion resistance. | Aerospace components, medical implants, sporting goods. |
Aluminum Alloys | Lightweight metals mixed with elements like silicon or copper to improve strength without adding much weight. | Lightweight, good thermal/electrical conductivity. | Packaging (foil), transportation (vehicles), construction (frames). |
Nickel Alloys | Metals made primarily of nickel combined with other elements such as chromium and molybdenum. | Excellent heat and corrosion resistance. | Chemical processing equipment, jet engine components, |
What Are the Similarities Between Alloy Steel and Carbon Steel?
Although alloy steel and carbon steel are distinct in composition and properties, they share some fundamental similarities.
Both types of steel are primarily made up of iron and carbon as their principal constituents. This common base provides both materials with certain inherent characteristics that are typical of steels, such as the ability to conduct heat and electricity, though to varying degrees.
Another similarity is their malleability. When heated to high temperatures, both alloy steel and carbon steel can be formed into various shapes through processes like forging, rolling, or pressing. This property makes them versatile materials suitable for a variety of manufacturing methods.
Regarding machinability, both alloy steel and carbon steel can generally be cut, drilled or machined with relative ease compared to other metals. This allows for precise fabrication that’s necessary in countless applications.
Both types of steels also undergo similar treatments like annealing, hardening, and tempering – thermal processes designed to impart specific mechanical properties or improved workability.
Lastly, sustainability is another aspect where these steels overlap; they are both recyclable without degradation in quality, supporting eco-friendly practices in most industrial sectors worldwide.
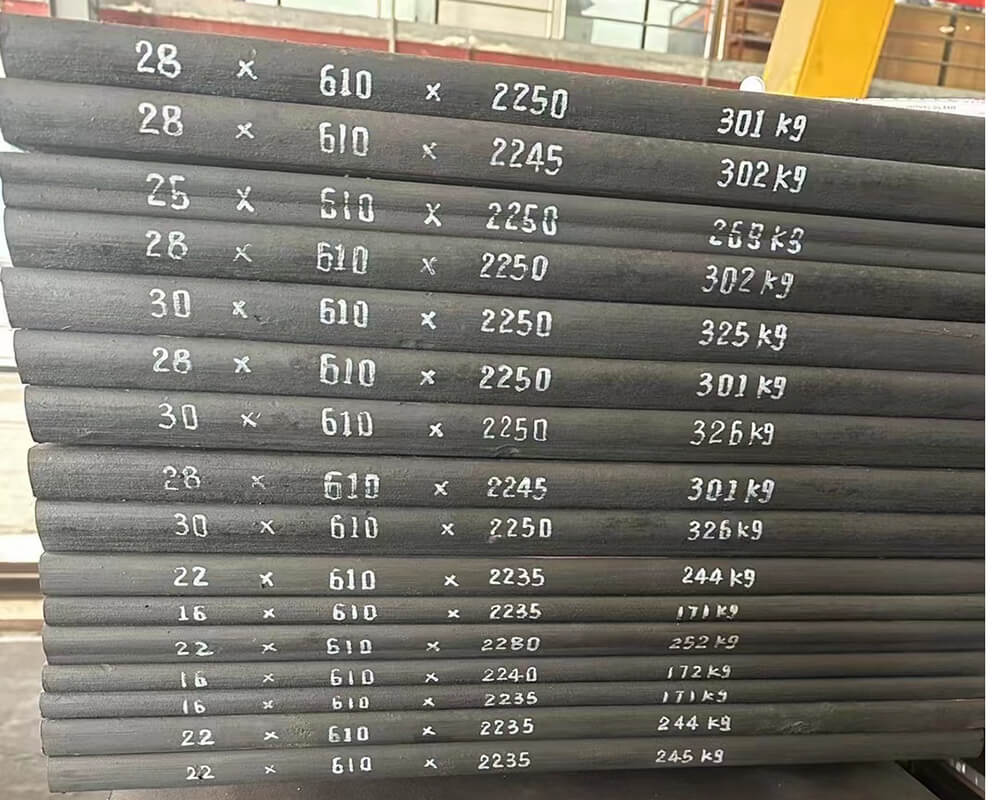
What Are the Other Comparisons for Carbon Steel Besides Alloy Steel?
When debating alternatives to carbon steel, other than alloy steel, there are various materials with unique properties suitable for different applications. Here we shall compare carbon steel with some of these alternative metals and materials:
Carbon Steel | Stainless Steel | Cast Iron | Aluminum |
---|---|---|---|
Comprised predominantly of iron and carbon, often with a carbon content up to 2.1% by weight. | An iron alloy with at least 10.5% chromium which enhances corrosion resistance. | Rich in carbon (>2%) which is generally present as graphite flakes; also contains silicon and manganese. | A lightweight metal with very low density, highly resistant to corrosion naturally because of its oxide film. |
Tends to rust and requires protective coatings or treatments for corrosion resistance. | Does not readily corrode, rust or stain with water as ordinary steel does. | Brittle and cannot withstand high stress; excellent wear resistance and compressive strength. | Non-toxic, non-magnetic and non-sparking; ductile but significantly less strong than steels without alloying. |
Ideal for structural components like beams and heavy supports due to its high strength and durability. | Used where both the properties of steel and resistance to corrosion are required; commonly used in cutlery, medical devices. | Commonly used in large structural components that are meant to be stationary like engine blocks, cookware. | Widely used in transportation (aircraft industry), packaging and construction due to its light weight. |
Other comparisons for carbon steel might include tool steels – specialized high-quality steels designed to become tools – or even non-metallic materials such as plastics or composites when assessing materials from a broader perspective including factors such as weight reduction or insulation properties.
What Are the Other Comparisons for Alloy Steel Besides Carbon Steel?
When comparing alloy steel with materials other than carbon steel, various metals and non-metals come into play, each with their unique set of properties and contributions to varying applications. Notable comparisons include stainless steel, aluminum alloys, titanium alloys, and even polymers or composites. Below is a comparison table illustrating how alloy steel stacks up against some of these different materials based on selected attributes:
Material Type | Corrosion Resistance | Weight | Cost | Strength-to-Weight Ratio | Thermal Expansion |
---|---|---|---|---|---|
Alloy Steel | Moderate | Heavier | Moderate | High | Moderate |
Stainless Steel | High | Heavier | Higher | Moderate | Low |
Aluminum Alloys | High | Lighter | Varies | Lower | High |
Titanium Alloys | Very High | Lighter | Higher | Very High | Low |
Polymers/Composites | Vary Widely | Lightest | Varies depending on type and grade | Varied | Low |
Stainless steel is renowned for its corrosion resistance due to the presence of chromium content which forms an invisible layer that prevents oxide formation. Although it has less strength compared to some high-strength alloy steels, stainless steel remains a popular material in environments where corrosion resistance is paramount.
Aluminum alloys are prized for their light weight and corrosion resistance, making them an ideal choice in aerospace and transportation industries where reducing weight while maintaining strength is essential. They do exhibit higher thermal expansion rates compared to alloy steels which can be an important consideration in precision applications.
Titanium alloys offer an exceptional strength-to-weight ratio along with excellent corrosion resistance. These properties make them especially attractive for aerospace and medical implant manufacture. However, they often come at a significantly higher cost than both carbon and most alloy steels.
Polymers and composites can be engineered to provide specific characteristics such as high tensile strength or enhanced thermal stability but generally are not as universally strong or heat resistant as metals. Their usage spans across automotive components to consumer goods where design flexibility is highly valued.
Each of these materials could be considered alternatives to alloy steel depending on the application requirements including environmental conditions, mechanical stress demands, and budget constraints among others. The selection hinges on finding the right balance between performance needs, physical properties tolerances, as well as economic considerations tied to material costs and longevity expectations.
In conclusion
In conclusion, the distinction between alloy steel and carbon steel is a critical consideration for any project that requires strength, durability, and specific performance characteristics. While alloy steels offer a mix of versatility and enhanced properties due to the addition of various elements, carbon steels provide a balance of cost-effectiveness and mechanical qualities sufficient for numerous applications.
Making an informed decision requires not only understanding these differences but also having access to expert guidance tailored to your unique requirements. We invite you to leverage our depth of knowledge and the comprehensive selection we offer by visiting our website or reaching out directly. Our team is dedicated to helping you determine the most suitable materials that align with your objectives. Take action today—explore our resources, or contact us so we can collaboratively ensure that your material choices lead to success in all your endeavors.