In the intricate world of materials science, alloy steels stand out for their tailor-made properties and wide-ranging applications. Among these nuanced metals, 8740 alloy steel emerges as a material of exceptional strength and versatility. This comprehensive guide delves into the essence of 8740 alloy steel, exploring its composition, characteristics, heat treatment processes, and the plethora of industrial applications it underpins.
What is 8740 Alloy Steel
8740 alloy steel is a grade of alloy steel that offers a harmonious blend of toughness, strength, and wear resistance due to its specific chemical composition. Named under the AISI (American Iron and Steel Institute) nomenclature, the “87” denotes a nickel-chromium-molybdenum series steel, while “40” represents an average carbon content in the range of 0.38-0.43%.
Primarily recognized for its richness in nickel content compared to other similar grades, which contributes significantly to its overall hardenability and toughness characteristics, this type of alloy steel is also well-regarded for having sufficient chromium content – enhancing corrosion resistance properties.
The presence of molybdenum further refines the material’s strength at high temperatures and augments the hardenability which allows the steel to maintain favorable mechanical properties over varied temperature ranges. This combination makes 8740 an ideal candidate for parts requiring both deep hardening and high strength.

Pros of 8740 Alloy Steel
The advantages associated with 8740 alloy steel stem from its balanced and tailored chemical composition, giving it properties that are highly sought after in critical engineering applications. Listed below are the key benefits that make 8740 alloy steel a preferred material for various industries:
**Pros ** | Explanation |
---|---|
Exceptional Hardness and Strength | Through heat treatment processes, this alloy achieves high hardness and strength, essential for wear-resistant applications. |
Good Toughness | It maintains good toughness which is crucial to prevent catastrophic failure when subjected to stress or impact. |
Enhanced Fatigue Resistance | The steel demonstrates superior resistance to fatigue, ideal for parts that experience repeated loading cycles. |
Remarkable Wear Resistance | Its ability to resist abrasions contributes significantly to the longevity of components made from this material. |
Improved Machinability | Even with its strength, 8740 alloy steel offers better machinability compared to many other high-strength steels. |
Superior Atmospheric Corrosion Resistance | A certain level of resistance against oxidation ensures durability when exposed to atmospheric conditions. |
Excellent Dimensional Stability | During heat treatment, the dimensional changes are minimal which allows for precision in manufacturing. |
The combination of these properties lends itself well to applications requiring robust materials that can withstand challenging service conditions without compromising their integrity or performance over time.
Cons of 8740 Alloy Steel
Despite the many advantages that 8740 alloy steel offers, it has several drawbacks that may limit its applications or increase costs in certain scenarios. A summarized representation of these cons appears below, detailing their relevance in certain contexts.
Cons | Explanation |
---|---|
Limited Corrosion Resistance | Due to its chemical composition, 8740 alloy steel is not inherently resistant to corrosion, which necessitates additional treatments like coating or plating for corrosive environments. |
Machinability Considerations | While machinable, 8740 requires careful handling and precise tooling given its toughness and strength properties, potentially leading to increased manufacturing costs. |
Weldability Concerns | Preheating and post-weld heat treatment are often required when welding high-strength alloys like 8740 to prevent cracking, thereby adding complexity to fabrication processes. |
Reduced Performance at Elevated Temperatures | The mechanical properties of 8740 can degrade at higher temperatures when compared with some other alloys designed specifically for high-temperature performance. |
These factors must be taken into consideration during the design phase of components intended for use in challenging environments or complex manufacturing processes where these characteristics can become problematic. Selecting this material involves a balance between its benefits and limitations based on the specific requirements of the intended application.
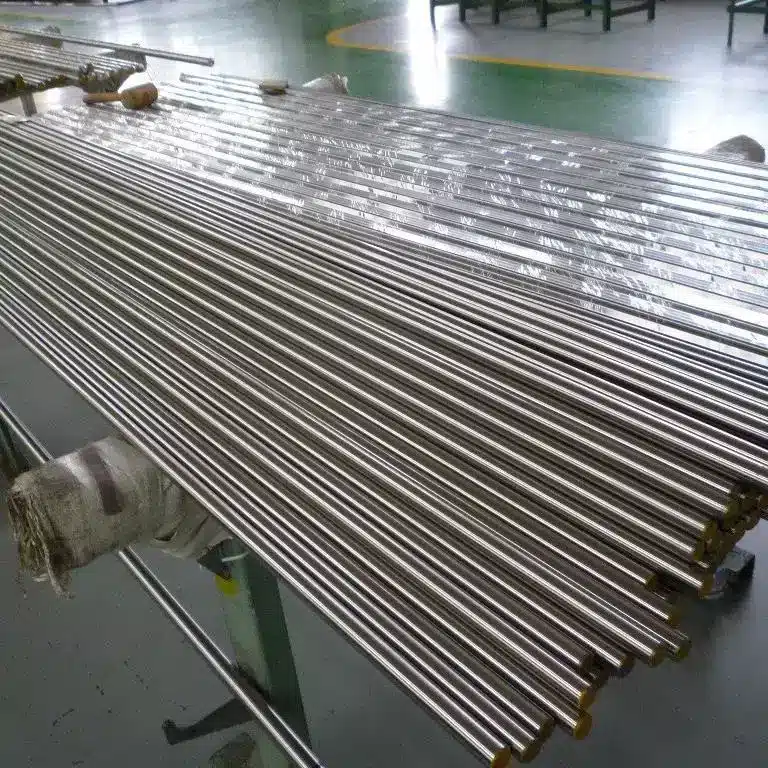
Chemical Composition of 8740 Alloy Steel
The chemical composition of 8740 alloy steel is meticulously balanced to provide the desired mechanical properties that make it suitable for critical engineering purposes. In particular, nickel increases toughness; chromium enhances hardness and resistance to wear and corrosion; while molybdenum contributes to strength and hardenability. Below is the typical chemical composition of 8740 alloy steel:
Element | Percentage (%) |
---|---|
Carbon (C) | 0.38 – 0.43 |
Manganese (Mn) | 0.75 – 1.00 |
Silicon (Si) | 0.15 – 0.35 |
Chromium (Cr) | 0.40 – 0.60 |
Nickel (Ni) | 1.65 -2.00 |
Molybdenum (Mo) | 0.20 – 0.30 |
Sulfur (S) | Max 0.040 |
Phosphorus (P) | Max 0.035 |
This careful combination gives rise to a versatile material with an optimal mix of ductility, hardness, and fatigue resistance required in various manufacturing applications.
Minor variations in the concentrations of these constituents can occur depending on specific grade requirements or customized needs for particular applications, but such adjustments are strictly controlled within industry standards to ensure quality and consistency in performance characteristics.
Physical Properties of 8740 Alloy Steel
The density of 8740 alloy steel typically hovers around 7.85 g/cm³.
Property | Value |
---|---|
Density | ~7.85 g/cm³ |
Mechanical Properties of 8740 Alloy Steel
Property | Description | Typical Values (Post-Heat Treatment) |
---|---|---|
Tensile Strength | Maximum stress steel can withstand while being stretched or pulled before failing or breaking. | 640 MPa to 850 MPa |
Yield Strength | Stress at which the material begins to deform plastically. | 540 MPa to 725 MPa |
Elongation | Measure of how much the material can deform before fracture. | 17% to 22% |
Hardness | Resistance to indentation and scratching; important for wear resistance. | Rockwell C28-C34 |
Impact Toughness | Ability to absorb energy during fracture. | Relatively high impact values |
Fatigue Strength | Endurance under cyclical loading, crucial for rotating machinery components. | Critical for dynamic stress endurance |
These properties make 8740 alloy steel highly desirable for applications requiring a combination of strength, toughness, wear resistance, and fatigue endurance across various industries.
Thermal Properties of 8740 Alloy Steel
8740 alloy steel is known for its high toughness and strength, also exhibits specific characteristics when subjected to heat.
The coefficient of thermal expansion for 8740 alloy steel is a critical factor to consider, as it determines how much the material will expand or contract with changes in temperature. Typically, the value ranges between 6.6 to 11.9 (10^-6/°C) from room temperature up to 500°C. This knowledge allows engineers to anticipate dimensional changes in components made from this alloy when exposed to different temperatures during service.
Thermal conductivity is another essential parameter that describes the capacity of 8740 alloy steel to conduct heat. This property directly affects its ability to evenly distribute thermal energy, impacting processes such as welding and heat treatment. Generally, the thermal conductivity at room temperature lies around 42.7 W/(m·K), showing decent potential for applications requiring heat dissipation.
In matters concerning specific heat capacity, 8740 alloy steel presents a value that typically ranges in the vicinity of 419-502 J/(kg·K) at room temperature. This measure helps predict how much energy is needed to raise the temperature of a unit mass by one degree Celsius and indicates how sensitive the alloy is to changes in ambient temperature conditions.
Furthermore, briefly touching on melting point without veering away from our focus on thermal attributes — this steel has a melting range spanning approximately between 1427°C and 1540°C (2600°F – 2804°F). The critical knowledge of melting point ensures that careful control is maintained during high-temperature applications such as forging and casting.
Property | Value at Room Temperature (Approx.) | Temperature Range | Importance and Applications |
---|---|---|---|
Coefficient of Thermal Expansion | 6.6 – 11.9 (10^-6/°C) | Room Temperature to 500°C | Predicting dimensional changes in components with temperature variations. |
Thermal Conductivity | 42.7 W/(m·K) | Room Temperature | Ability to evenly distribute thermal energy in processes like welding and heat treatment. |
Specific Heat Capacity | 419-502 J/(kg·K) | Room Temperature | Energy required to raise temperature by one degree Celsius, affecting sensitivity to temperature changes. |
Melting Point | 1427°C – 1540°C (2600°F – 2804°F) | High-Temperature Applications | Critical for maintaining control during forging and casting processes. |
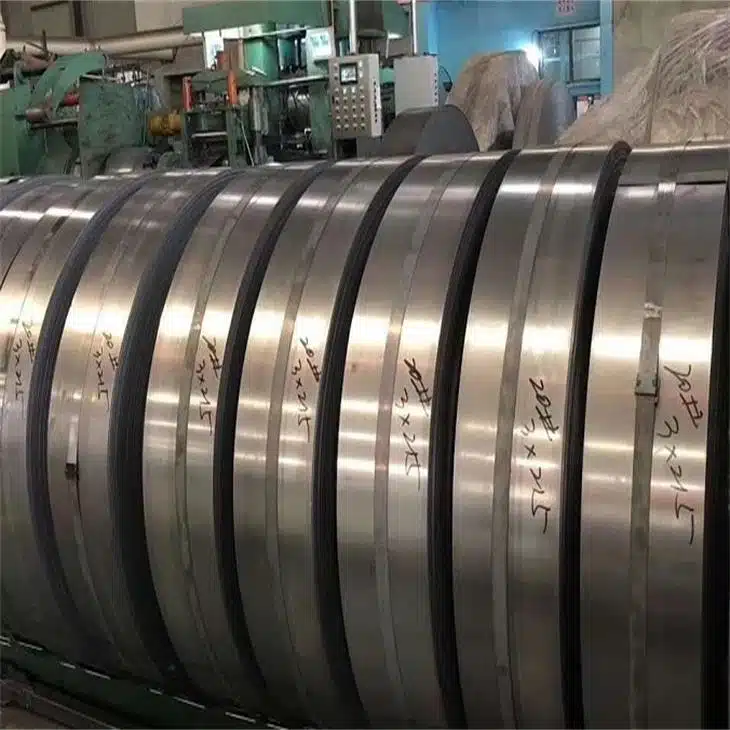
What is 8740 alloy steel used for?
Industry | Uses |
---|---|
Aerospace | Aircraft gears, fasteners, structural components |
Automotive | Axles, crankshafts, gearsets |
Oil and Gas | Drilling parts that require high toughness |
Motorsports | High-performance engine components |
Industrial Machinery | Heavy-duty gears, spindles |
Equivalent Materials to AISI 8740 Alloy Steel
Below is a table that lists several materials considered to be equivalent or closely comparable to AISI 8740 alloy steel:
EN (European Standard) | DIN (German Standard) | JIS (Japanese Standard) | BS (British Standard) | Industry Specifications |
---|---|---|---|---|
40NiCrMo2-2 | 34CrNiMo6 | SNCM240 | 832M13 | AMS 6325, AMS 2012 |
– | 41CrNiMo7-3-2 | – | EN24 / EN24T | SAE J404, SAE J412 |
– | WNr.1.6565 | – | – | ASTM A29, ASTM A322 |
These equivalents may vary slightly in their specific composition and heat treatment processes but typically offer broadly similar mechanical performance characteristics. It must be noted that even if the basic materials mentioned can substitute AISI 8740 within certain applications, it’s essential to review all specifications including the desired heat treatment and final application requirements before making a selection.
While interchangeability is often possible on paper, real-world applications will dictate thorough validation testing to ensure equivalency in performance within the intended engineering context.
What Material is Used in the AMS 6322?
AMS 6322 is a specification for a nickel, chromium, and molybdenum alloy steel known as AISI 8740. This material is widely recognized for its high tensile strength and toughness, which are achieved through a heat treatment process that results in a consistent hardened surface while maintaining a robust core. The inclusion of elements such as nickel, chromium, and molybdenum within the chemical composition of this alloy provides it with enhanced characteristics suited to rigorous applications.
In conclusion
In conclusion, 8740 Alloy Steel offers a remarkable balance of strength, toughness, and wear resistance, suitable for a broad range of industrial applications. Understanding the properties and potential of this versatile steel is pivotal to making informed choices for your manufacturing processes or engineering projects.
We invite you to deepen your knowledge and discover the full benefits that 8740 Alloy Steel can provide. Our team of experts is dedicated to guiding you through the selection process and ensuring that the material meets your specific requirements. Whether you are looking for custom solutions or seeking guidance on the best applications for this alloy, we are here to assist.
Don’t hesitate to leverage our expertise. Visit our website or contact us directly to explore how we can help you harness the full potential of 8740 Alloy Steel for your endeavors. Allow us to be part of your journey in achieving exceptional performance and durability in your products. Reach out today – we look forward to collaborating with you and contributing to your success.